铜箔是电池中仅次于正极、负极和电解液 的关键材料,对电池的性能及成本指标影响较大。在锂电产业的发展过程中,负极集流体材料由压延铜箔到电解铜箔,厚度逐步降低,目前超薄电解铜箔的厚度已经低于4.5微米,后续大幅减薄的难度较大。为进一步提高密度降低成本,复合铜箔集流体材料逐渐成为产业界和投资界关注的热点,在建及规划产能巨大,其中一些问题值得关注和探讨。
复合铜箔,是指在PET/PP等有机材质薄膜基材的单面或双面表面上加工制作铜导电层后形成的一种新型材料(本文中的复合铜箔是特指双面复合铜箔)。相比传统铜箔,复合铜箔作为锂电负极集流体材料的优点主要在于铜材料消耗显著降低,重量明显下降,还能在一定程度上提升电池安全性,具有低成本、高能量密度和相对安全等优势。
由于高分子薄膜基材为不导电的绝缘体无法直接进行电镀,目前主要的复合铜箔生产工艺路线是先在基材薄膜上采用PVD真空镀膜方法进行导电预镀铜层加工,然后再采用传统湿法电镀铜层加厚(该套工艺简称为两步法)。
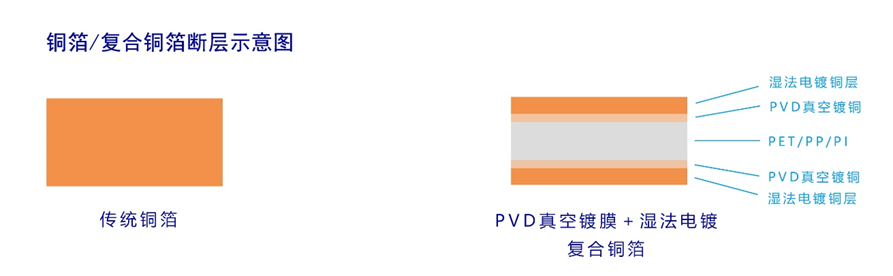
首先是在真空环境中,对3-5微米厚的PET/PP等聚合物薄膜基材表面进行活化预处理以改善基材表面质量、提升基材与金属涂层的结合力,然后采用PVD工艺(物理气相沉积工艺)在基材表面沉积一定的厚度(或者一定的方块电阻 简称方阻)的金属导电层(通常的铜层厚度范围为20nm-200nm,方阻范围为0.2欧姆-2.5欧姆);
在大气环境中,将第一步得到的预镀铜导电层薄膜转移至连续镀铜生产线,采用湿法电镀工艺加厚铜层至每面600-1000nm (0.6μm-1μm) ,从而得到所需的锂电复合铜箔集流体。(相应的一些膜层整理及后处理工序不在本文讨论范围内)。
即使性能指标优秀,成本问题也必将是大规模产业化发展复合铜箔的关键因素。复合铜箔的综合成本构成中,设备投资、材料及能源消耗是主要部分,两步法中的一些技术细节对这几项成本参数影响很大,值得关注和研究。
由于两步法涉及真空镀膜和连续湿法电镀两个不同的细分技术领域,各自专业性都很强,所以短时间内对复合铜箔的全制程进行准确判断并得出总成本最低的最优参数组合难度很大,可能还需要一段时间的摸索及各方面的共同努力。本文尝试从真空镀膜环节的两个具体问题入手,举例分析不同基材及几种预镀铜层参数对复合铜箔可能造成的成本影响,供行业内技术及研究人员参考,希望能够“抛砖引玉”为复合铜箔的产业发展起到一点促进作用。
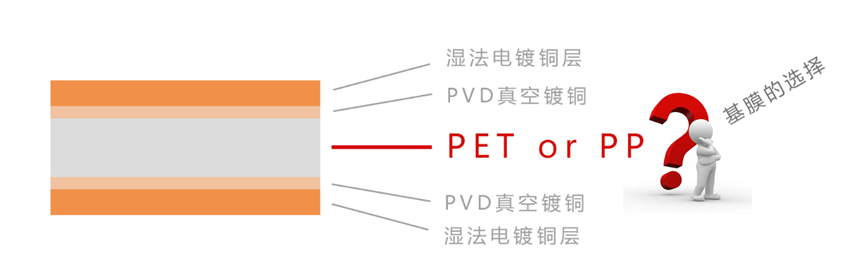
一、PET/PP基材的差异对PVD预镀铜环节影响较大
目前行业对于复合铜箔的技术指标参数还未形成标准化,对于有机材料基膜的选择当前仍不太明确,选择PET基膜的厂商较多,但也有一部分厂商选择PP基膜。由于PET和PP薄膜分属极性和非极性聚合物,表面特性差异大,这种差异对基材与铜膜之间的结合力有明显影响,从而导致与不同基材相对应的PVD镀膜设备的配置及产能指标存在很大不同。
目前特别针对PP基材的硬件及工艺设计,已经可以完全满足厂商提出的复合铜箔结合力要求。一般情况下,适用于PP基材的PVD镀膜设备可以兼容PET基材(可以视为基材通用型设备),但PET基材专用型镀膜设备无法兼容PP基材镀膜。由于PP基材在PVD设备中的高速在线活化预处理环节比较复杂,通用型设备的造价明显高于PET基材专用型设备;同时,一般情况下加工PP基材时的设计加工速度也都会低于PET基材加工速度。
因此,单独测算预镀铜导电层环节,不考虑PET/PP的基材成本差异,剩余部分二者的成本差可能会超过30%,值得关注。如果锂电行业用户尽早统一明确了基材种类和相应量化的技术指标,将能够加快相关PVD镀膜设备定型、降低设备投入成本,大大促进复合铜箔的发展。
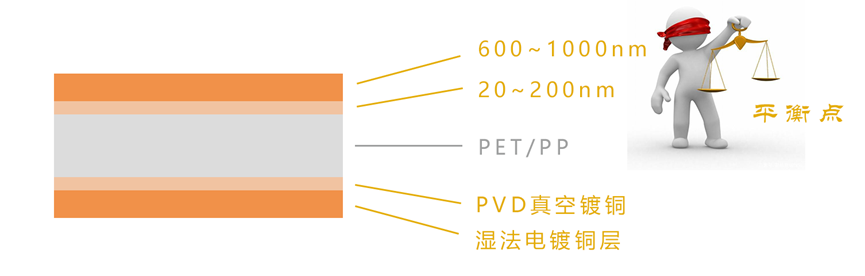
二、PVD真空镀铜与传统湿法电镀铜加厚的工艺参数匹配优化
第一步PVD真空镀铜(预镀铜导电层)环节是两步法中的关键和必要步骤,PVD制程具有环保洁净、占地面积小、自动化程度高的优点,该环节设备投入带来的折旧费、能源及材料消耗对最终的产品成本影响较大。PVD制程在大规模量产时,一定的条件范围内,单位面积产品的能源及材料消耗与预镀铜层厚度(或方阻)基本呈线性比例关系,由于单位面积的折旧费与设备产能近似呈比例关系,而设备产能与预镀铜层厚度成反比,所以单位面积折旧费与预镀铜层厚度(或方阻)也近似呈现线性比例关系。
PVD制程的技术特点决定了其在一定的范围内可以对膜层厚度进行灵活调节和控制,非常方便地得到所需要的最佳膜层方阻(通常在预镀铜导电层环节选择的参数范围是厚度20nm-200nm,方阻为0.2欧姆-2.5欧姆左右),因此可以根据第二步湿法电镀环节所需的最佳预镀铜层方阻数据对第一步的生产工艺参数进行选择匹配。
第二步湿法电镀铜加厚环节的成本通常与相关设备折旧(设备产能)、材料消耗、污水处理及人工场地成本等因素相关,与能源消耗(电费)关系不太敏感。预镀铜导电层的方阻至少需要低于一定的数值才能实现连续湿法电镀加厚,目前一般认为,特别设计的连续湿法电镀设备所需要的预镀铜层方阻至少应小于2.5欧姆(或者2欧姆),相对通用一些的连续湿法电镀设备则要求预镀铜层方阻更低些,一般要求小于700毫欧(或者低于600毫欧);通常在一定的范围内,预镀铜导电层的方阻越小,连续湿法电镀设备的生产速度就越高(单位产能连续湿法电镀设备的投资相应也较低一些),从而导致单位面积产品在湿法电镀环节的折旧及人工场地成本就越低。
综合上述两段可知,两步法中真空镀和湿法电镀两环节一定存在相对最优的工艺参数匹配组合方案,能够实现复合铜箔产品的综合成本最低目标(或者是单位投资综合产能最大等其它目标)。以下进一步举例说明,分类总结计算出第一步PVD真空镀铜环节在几种不同条件下的产能及成本参数,供行业内技术和研究人员参考。
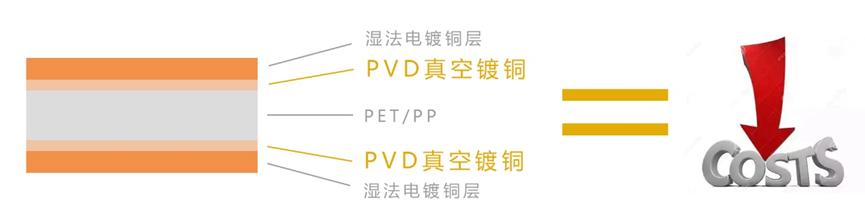
某型号卷绕式复合铜箔PVD预镀铜设备在不同参数条件下的产能和成本分析
-
基材薄膜长度大于30000米,厚度大于3μm,幅宽约1.5米
-
成品复合铜箔宽度大于1.25米,镀膜速度5-20米/分钟
-
双面镀膜,每面铜层厚度25-100nm(等效方阻约0.5-2.5欧姆)
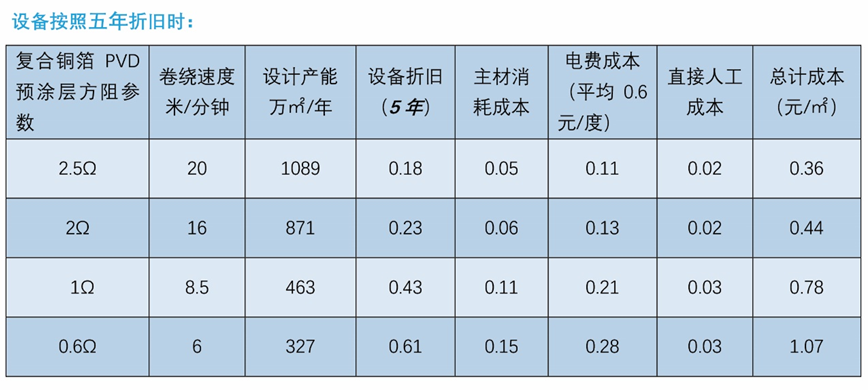
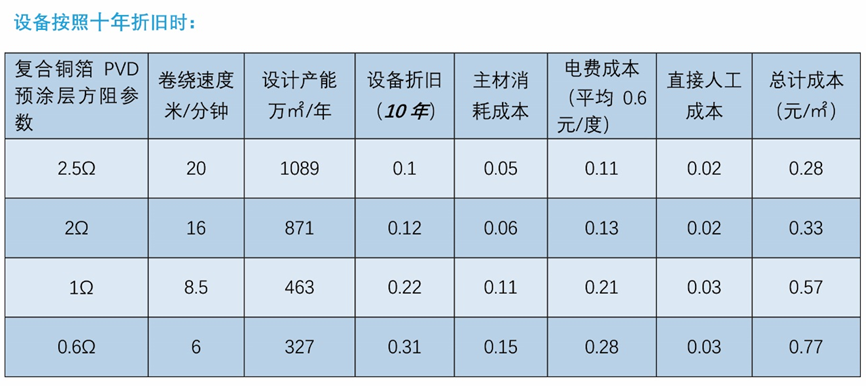
(年设计产能按照等效全年330天每天镀膜时间22小时测算)
从上述两表格可以看出,随着方阻的降低,PVD真空预镀铜导电膜成本逐步上升,但二者并非线性比例关系,同时该环节的成本与设备折旧(单位产能投资及使用年限)及电价水平关系密切。参考上述各种指标,只要进一步综合考虑第二步的湿法电镀增厚环节的对应成本,就有可能获得综合成本最优的匹配参数组合。
另外,随着技术的进步,在3.0-4.5微米厚的PET/PP等聚合物薄膜表面直接采用PVD真空镀铜方式一次形成1+1 μm的金属铜膜的PVD一步法,由于其高效清洁环保的技术特点,在有效降低设备成本及能耗指标后,也是一种值得重视的产业发展方向。
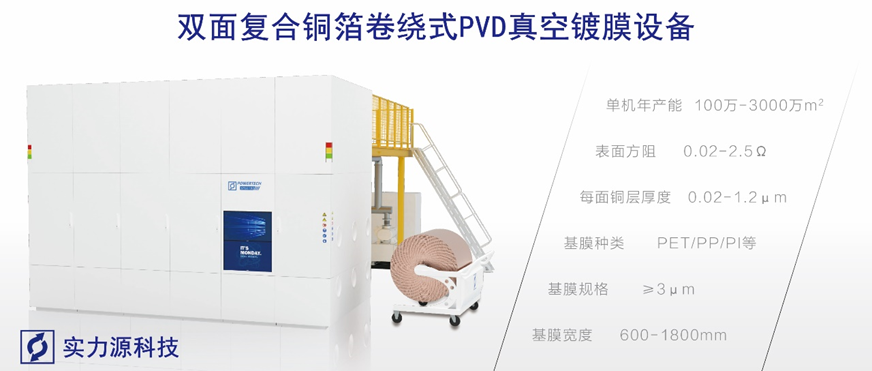
北京实力源科技创始于1993年,是国内首批专注高端真空镀膜装备研发与制造的国家级高新技术企业,总部位于北京市中关村科技园区丰台园,生产基地分别位于北京自由贸易试验区和北京国际航空港区南部,厂房面积约3万平方米。公司致力于各类真空镀膜装备及其关键组件的技术开发、产品制造及销售,拥有真空镀膜技术领域的全系列自主知识产权,近三十年来开创性的引领了PVD技术在多个新兴领域的落地应用及大规模发展,为国内及国际数百家高端客户及军工航天等特种行业提供了优质专业的产品和服务,是技、工、贸一体的国家级专精特新“小巨人”企业和“瞪羚”企业。
公司主营的真空镀膜设备包括:各类卷对卷真空镀膜设备、连续式真空镀膜设备、半导体显示行业专用真空镀膜设备、通用型磁控溅射加离子镀复合真空镀膜设备、光学真空镀膜设备等。公司及产品均通过ISO9001认证、CE认证和国家真空设备质量监督检验中心的检验认证。
程生:13439055362
安生:15901033147
10月28日,艾邦将在深圳举办“动力电池复合铜箔大会”,届时,北京实力源将会有展台展示产品,欢迎大家前来参观!
原文始发于微信公众号(锂电产业通):锂电复合铜箔集流体大规模生产中的PVD技术探讨
动力电池产业链非常长,从无机非金属材料到金属氧化物,到高分子材料,都有相关。为了让加强艾邦粉丝在新能源电池,特别是与电池相关材料的交流,特建立动力电池微信群,欢迎产业链上下游的朋友加入

欢迎关注艾邦锂电产业微信公众号;锂电池产业链交流、资讯、人脉圈。从正负极材料生产到涂布,隔膜、电解液、封装材料到检测组装等这些环节涉及的材料、辅材、添加剂、耗材,以及相关设备,相关企业介绍。