未势能源通过对自主膜电极电堆的测试应用和高响应性能空压机、氢泵的标定优化,最终实现了在全功率范围内电堆级85kW/s、系统级60kW/s的平均升降载速率,以及在快速升载过程中电压最大偏差小于26mV的良好表现。
未势能源依托长城集团的长期战略规划,对第二代100kW级燃料电池系统的性能进行了全方位的升级,具备了行业领先的高效率、快响应、长寿命、低故障率以及NODS在线故障诊断能力。
本文将主要分享未势能源在燃料电池系统快速响应技术上的相关的开发过程和部分测试数据表现。
升降载功能需求分解

为了满足整车的平均60kW/s的燃料电池系统净功率响应需求,系统首先需要考虑燃料电池电堆升载能力和系统辅件的寄生功率消耗。其中,系统的高压辅件主要由空压机、氢泵、水泵组成,且往往氢泵和水泵的额定功率不超过1kW,而空压机的额定功率在15kW左右,并在升载过程中存在明显的功率尖峰问题。
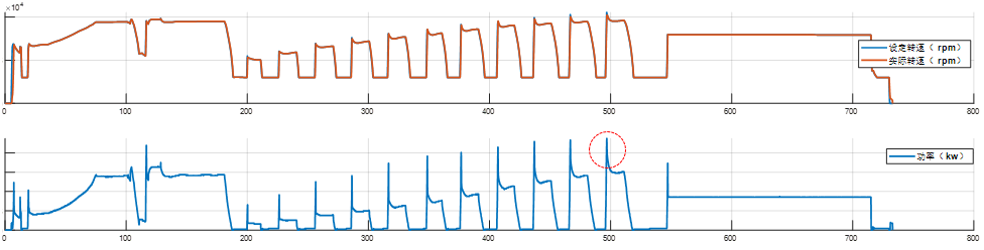
空压机功率尖峰示意图
基于对系统辅件寄生功率的初步估算,燃料电池电堆需要满足约80kW/s的平均升降载能力。并且,针对电堆的80kW/s的平均升降载需求,也就初步得到了对氢气模块、空气模块、冷却模块、DCDC模块的零部件响应能力需求,主要涉及供氢阀的最大供氢速率、氢泵的最大升降载速率、空压机的的最大升降载速率、水泵的最大升降载速率、各类阀门的最大开关速率以及DCDC的最大响应速率等。
结合第一代系统资料和部分仿真数据,细化零部件指标成为未势能源提供给零部件供应商的技术需求,并展开合作开发。
在完成对燃料电池电堆和系统辅件的核心参数指标需求分解后,主要的工作集中在系统控制策略和系统通讯协议方面。我们围绕电堆升降载能力进行了测试研究和测试优化,对系统控制策略和系统通讯协议展开了技术攻关和设计优化改进。
电堆升降载能力的测试应用
电堆在考虑升降载能力时,应分别从性能和耐久两个角度进行评价(本文暂围绕性能的角度展开介绍)。电堆的升降载性能主要受两方面因素限制,一个是氢空水的快速供给,一个是电堆本身的材料和结构特性。其中氢空水的快速供给主要是系统级的工作且电堆测试台架也很难模拟,所以电堆级的测试应用主要围绕在供给充足的情况下燃料电池的升降载特性和影响因素。
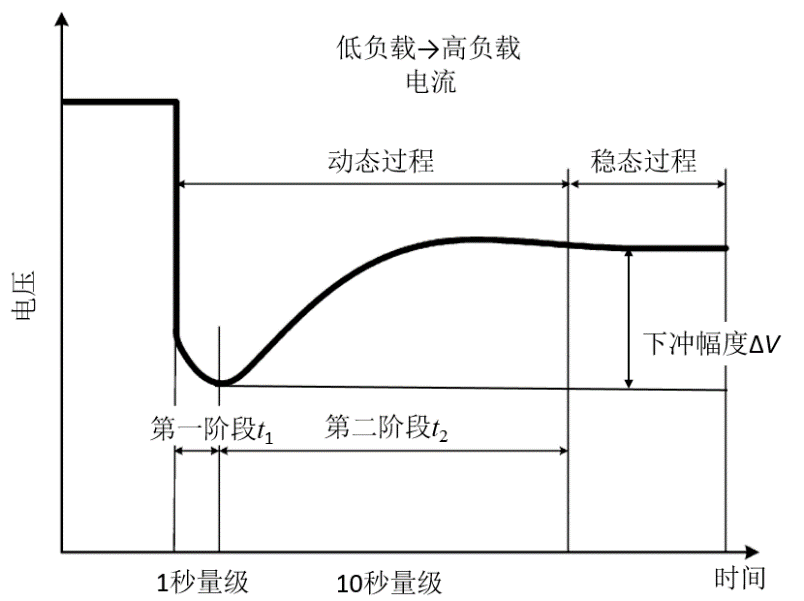
升载过程电压理论变化过程
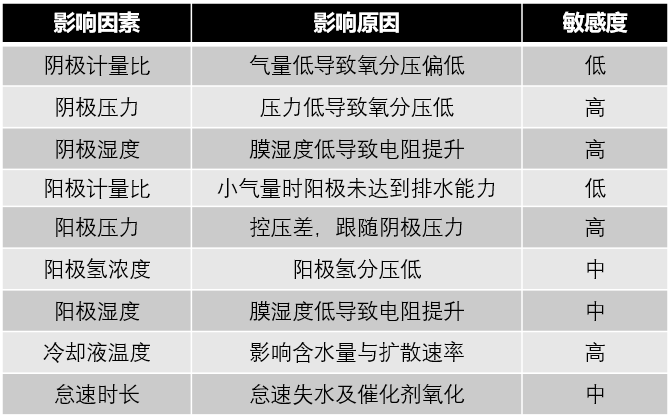
升降载影响因素测试项及敏感度
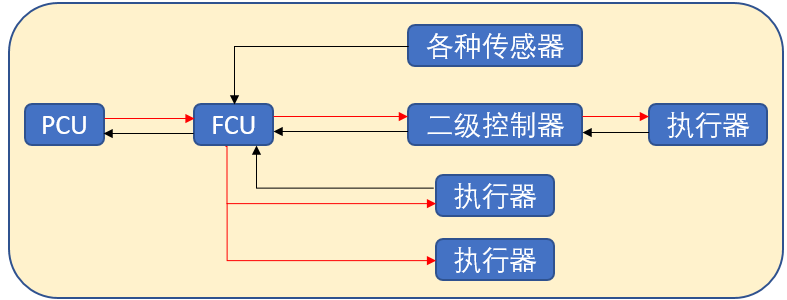
不同温度下拉载时平均电压实测数据

不同阳极入口压力下拉载时平均电压实测数据

不同阴极计量比下拉载时平均电压数据
基于优异的双极板和膜电极匹配和设计以及针对快速变载的操作条件优化设计以及操作条件边界设定,未势能源已经实现了电堆1000A/s的变载验证测试。
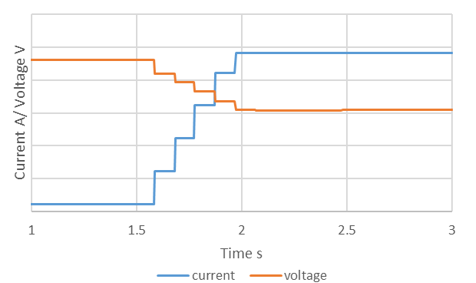
电堆级1000A/s变载能力
系统升降载能力的测试优化
在对燃料电池电堆升降载特性有了一定的认识后,系统级升降载控制策略需要平衡电堆的升降载需求和系统辅件的升降载能力。其中,升载过程和降载过程应分别考虑,这里以相对复杂的升载过程举例说明。为了满足整车动力性的需求,一个大功率幅值的升载过程往往也只持续1至2s,而通常来说,受限于CAN通讯网络的承载能力,燃料电池控制器和系统辅件的二级控制器的通讯时间介于10ms至100ms之间。
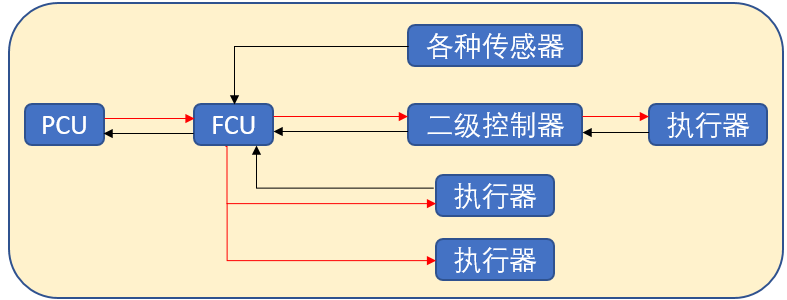
燃料电池通讯网络示意图
燃料电池系统通讯延迟组成
在进行系统台架测试时,即使测试所用的上位机的采集精度很高,比如10ms记录一个数据点,但如果部分执行器和燃料电池控制器之间的通讯周期是100ms,那么每10个采集到的数据,只有1个是真实的。针对一个仅持续1000ms甚至更短的升载过程,100ms的数据采集精度意味着在计算升载速度时的误差将超过10%。为了减小误差范围,针对系统辅件的控制优先级和CAN通讯网络承载能力,差异化的设定不同辅件和系统控制器间的通讯周期,是非常简单有效的方法。
在确认了上文所述的电堆、系统辅件、通讯网络相关的工作内容后,主要的工作就是燃料电池系统控制策略的优化和控制参数的标定。针对升载过程,优化目标主要考虑三个方向:①尽可能缩短整车指令下达到系统辅件的响应周期,②在燃料电池电堆长时间稳态运行参数的基础上,下探升载过程短时间运行参数的边界,③更多的限制快速升载出现的频率。
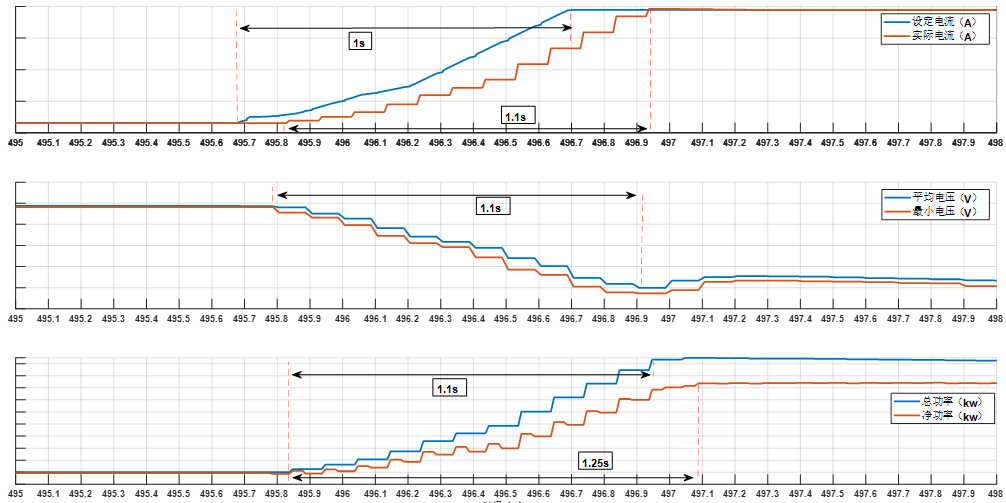
燃料电池系统升载过程展示
目前,通过大量的测试标定工作,未势能源已达成了系统级60kW/s的平均升降载能力,并且在升载过程中实现电压偏差<26mV。未来,未势能源将会基于变载进行更多的性能及耐久相关验证,持续优化设计和操作条件,为客户提供性能更高且操作更加友好的燃料电池产品,助推氢燃料电池汽车规模化普及和商业化发展。
来源:未势能源
原文始发于微信公众号(艾邦氢科技网):燃料电池系统瞬态响应开发过程和测试数据分享
