便携储能产品的生产可分为SMT贴片、PCBA测试、电池加工、电池包组装、老化测试、成品包装等环节。
SMT贴片指的是在PCB基础上进行加工的系列工艺流程的简称,PCB(Printed Circuit Board)为印刷电路板。SMT是表面组装技术(表面贴装技术)(Surface Mounted Technology的缩写),是电子组装行业里最流行的一种技术和工艺。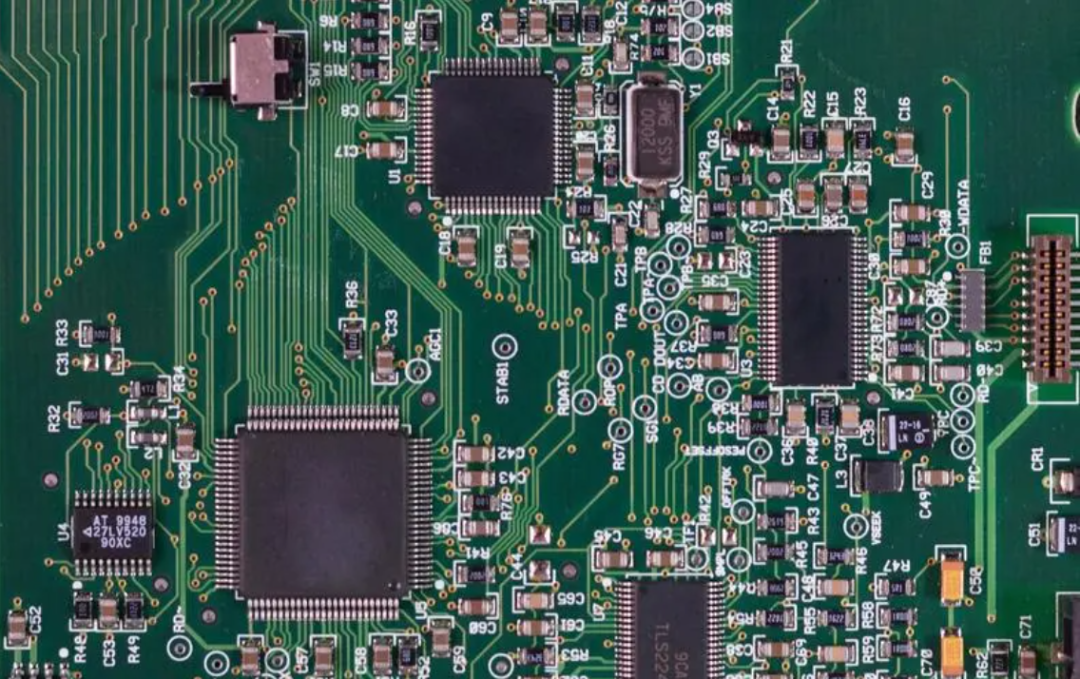
它是一种将无引脚或短引线表面组装元器件(简称SMC/SMD,中文称片状元器件)安装在印制电路板(Printed Circuit Board,PCB)的表面或其它基板的表面上,通过再流焊或浸焊等方法加以焊接组装的电路装连技术。在通常情况下我们用的电子产品都是由pcb加上各种电容,电阻等电子元器件按设计的电路图设计而成的,所以形形色色的电器需要各种不同的smt贴片加工工艺来加工。SMT基本工艺构成要素包括:丝印(或点胶),贴装(固化),回流焊接,清洗,检测,返修1、丝印:其作用是将焊膏或贴片胶漏印到PCB的焊盘上,为元器件的焊接做准备。所用设备为丝印机(丝网印刷机),位于SMT生产线的最前端。2、点胶:它是将胶水滴到PCB板的固定位置上,其主要作用是将元器件固定到PCB板上。所用设备为点胶机,位于SMT生产线的最前端或检测设备的后面。3、贴装:其作用是将表面组装元器件准确安装到PCB的固定位置上。所用设备为贴片机,位于SMT生产线中丝印机的后面。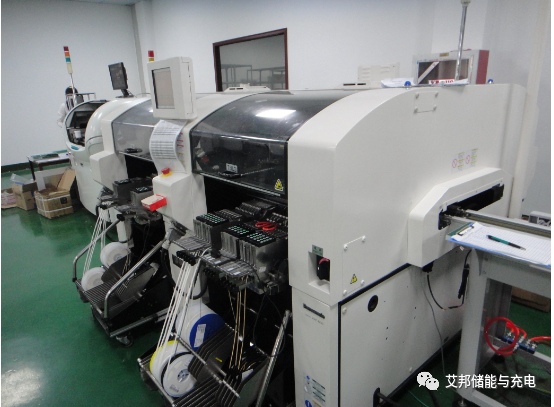
贴片机
4、固化:其作用是将贴片胶融化,从而使表面组装元器件与PCB板牢固粘接在一起。所用设备为固化炉,位于SMT生产线中贴片机的后面。5、回流焊接:其作用是将焊膏融化,使表面组装元器件与PCB板牢固粘接在一起。所用设备为回流焊炉,位于SMT生产线中贴片机的后面。6、清洗:其作用是将组装好的PCB板上面的对人体有害的焊接残留物如助焊剂等除去。所用设备为清洗机,位置可以不固定,可以在线,也可不在线。7、检测:其作用是对组装好的PCB板进行焊接质量和装配质量的检测。所用设备有放大镜、显微镜、在线测试仪(ICT)、飞针测试仪、自动光学检测(AOI)、X-RAY检测系统、功能测试仪等。位置根据检测的需要,可以配置在生产线合适的地方。8、返修:其作用是对检测出现故障的PCB板进行返工。所用工具为烙铁、返修工作站等。配置在生产线中任意位置。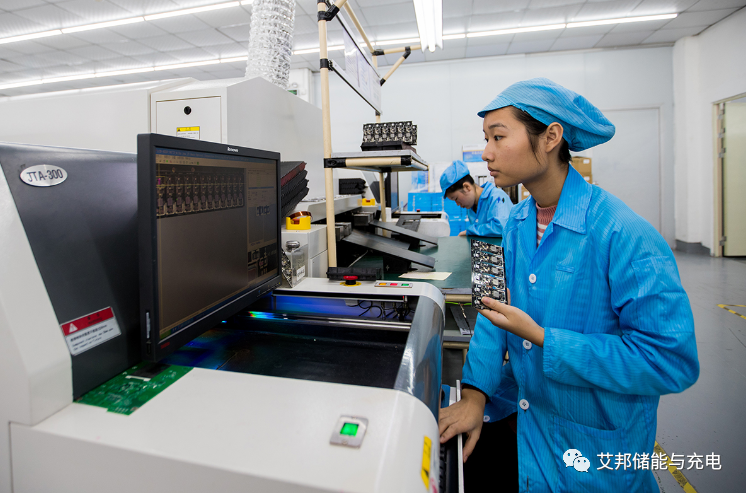
贴片
3)安全及可靠性:具有安全可靠的防护措施,充分考虑系统与设备之间的效率匹配和缓冲,采用必要的措施保证系统正常运行、数据通讯安全主控制的实时性。4)易操作可维护性:操作人员能够快速上手操作,降低系统的管理维护和操作成本。基于设备免维护性的需求,充分考虑设备配件规格的通用性。4.SMT贴片设备
一般一条完整的SMT产线常规包含以下设备:上板机、印刷机、接驳台、SPI、贴片机、插件机、回流焊、波峰焊、AOI、X-ray、下板机等设备,以上设备是一条比较完整的smt配线清单设备,不同工厂可根据实际产品需要增删相关设备,但必不可少的设备包含印刷机、贴片机、回流焊。
除了生产设备外,检测设备对SMT贴片来说也必不可少。SMT检测设备有:SPI锡膏检测仪,炉温曲线测试仪、AOI光学检测仪、ICT在线测试仪、X-RAY检测系统、ATE测试系统等。SMT周边设备:锡膏搅拌机、接驳台、分板机、上下板机、上下料机、缓存机等。
PCBA=PCB+Assembly,即印刷线路板装配,也就是说PCB+电子元器件装配过程,就叫做PCBA,也可以理解为成品线路板。如下:PCBA Test 是指对贴装好电子元器件的PCBA电路板进行电气导通性及基于输入输出数值的检测。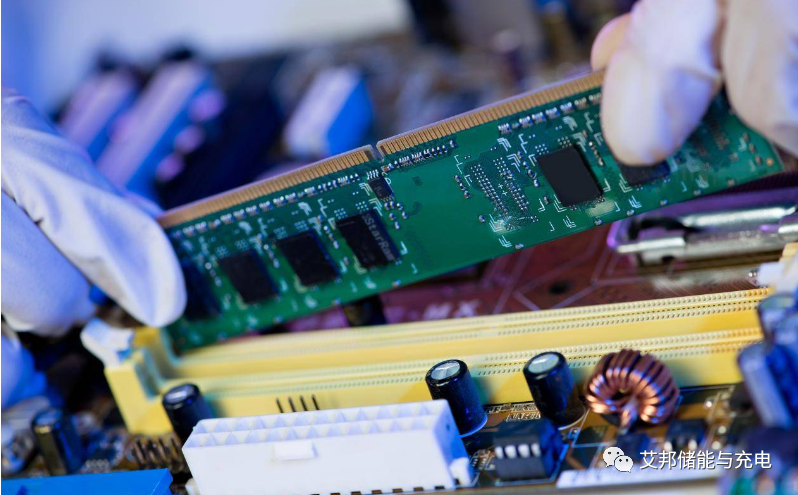
在PCB电路板的设计中,不同测试点之间存在电压和电流等数值关系。但是PCBA生产加工的工艺流程十分复杂,包括有PCB板制程、元器件采购与检验、SMT贴片组装、DIP插件、PCBA测试等多道重要工序,在生产加工过程中,可能会因为设备或操作不当出现各种问题。因此需要借助专业的测试设备或者手工操作万用表方式,对测试点进行检测,以此验证实际PCBA板是否符合设计要求,确保每个产品不会出现质量问题。PCBA测试是确保生产交货质量的关键步骤,根据客户设计的测试点、程序、测试步骤制作FCT测试治具,然后将PCBA板放置在FCT测试架上完成测试。通过FCT测试架连接PCBA板上的测试点,从而形成一个完整的通路,连接电脑和烧录器,将MCU程序上载。MCU程序会捕捉用户的输入动作(比如长按开关3秒),经过运算控制旁边电路的通断(比如LED等闪亮)或者驱动马达转动等。通过在FCT测试架上观察测试点之间的电压、电流数值,以及验证这些输入输出动作是否跟设计相符,从而完成对整块PCBA板的测试。PCBA测试主要包括:ICT测试、FCT测试、老化测试、疲劳测试、恶劣环境下测试这五种形式。ICT(In-Circuit Test)测试,主要包含电路的通断、电压和电流数值及波动曲线、振幅、噪音等,不涉及到功能按键或者输入输出方面的测试。FCT(Functional Test)测试,需要首先将编写好的单片机(MCU)程序通过烧录器(如ST-Link、JTAG)烧录到程序IC中,对整个PCBA板的功能进行模拟测试,比如按键后,LED灯亮;两按键同时按,恢复出厂设置等等。从而发现硬件和软件中存在的问题,并配备必要的贴片加工生产治具和测试架。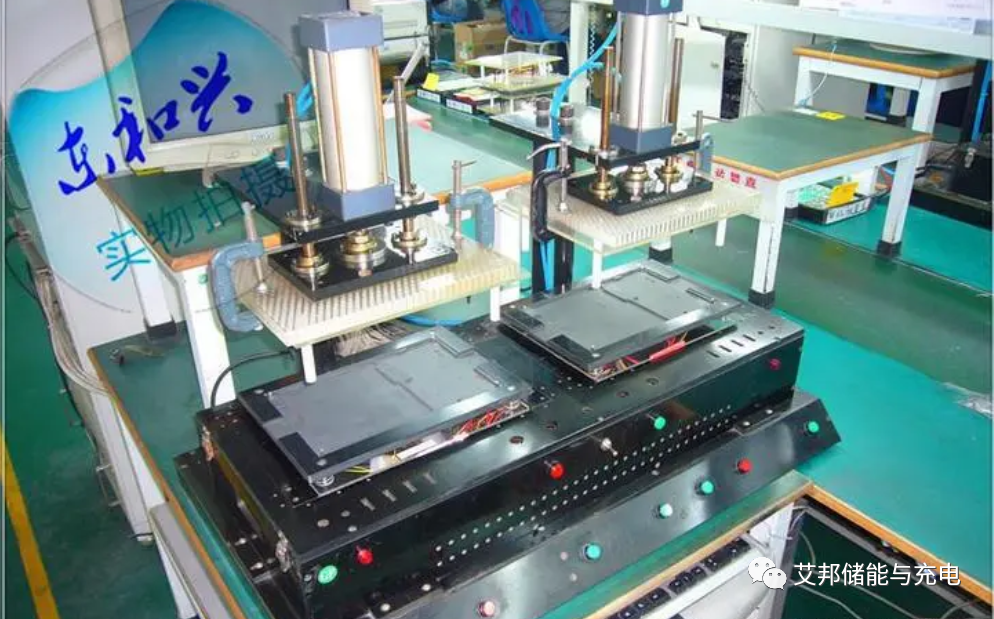
气动FCT(Functional Test)测试
老化(Burn In Test)测试,主要是对已烧录程序并且FCT通过的PCBA板,进行长时间、周期性的模拟用户输入输出,以此检测其耐用性和焊接可靠性。经过老化测试后的电子产品才能批量出厂销售。疲劳测试主要是对PCBA板抽样,并进行功能的高频、长时间操作,观察是否出现失效,判断测试出现故障的概率,以此反馈电子产品内PCBA板的工作性能。恶劣环境下测试主要是将PCBA板暴露在极限值的温度、湿度、跌落、溅水、振动下,获得随机样本的测试结果,从而推断整个PCBA板批次产品的可靠性。
锂电池电芯为什么要分选?
锂电池组的不一致性是一个不断累积的过程,时间越长单体电池之间产生的差异越大;并且锂电池组还会受到使用环境的影响,在以后的使用过程中单体电池的不一致性会被逐渐放大,从而导致某些单体电池性能加速衰减,最终导致电池没有使用功能。锂电池组的不一致性主要受时间的影响较大,原因主要包括两个方面:
1、首先是制造过程中存在工艺上的问题和材质的不均匀等问题,使得锂电池的材料和等存在很微小的差别;在锂电池组投入使用后,电池组中各个电池的电解液密度、温度和通风条件、自放电程度及充放电过程等差别的影响,同一批次出厂的同一型号电池容量和内阻可能存在差异性。2、装车使用时,锂电池组中各个电池的电解液密度、温度和通风条件、自放电程度及充放电过程等差别的影响。锂电池电芯分选所用设备
锂电池电芯自动分选机可以直接分选出设置的开路电压、交流内阻等参数。并且分选效率高,10个通道一起分选,9个OK通道,1个NG通道。保障了锂电池包的一致性。参考资料:华宝新能招股书、CSDN:Sandyxxh、乾元坤和、深圳中美创力、网络等原文始发于微信公众号(艾邦储能与充电):便携储能生产工艺流程