翘曲变形是薄壁塑料件注塑成型中的常见缺陷之一,当翘曲变形超过允许误差后,就成为成型缺陷,进而影响产品装配。对各类大量日益增加的薄壁产品的翘曲变形做出准确分析是有效控制翘曲缺陷的前提。翘曲变形分析大都采用定性分析,从制品设计、模具设计及注塑工艺条件等方面采取措施,尽量减小翘曲变形度。
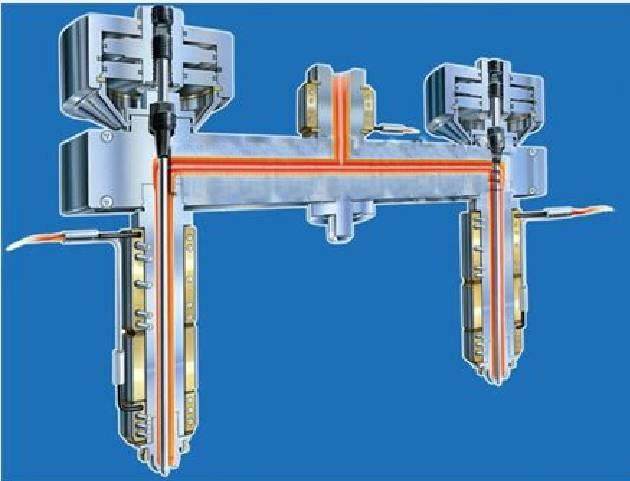
模具浇口的位置、形式和浇口的数量将影响塑料在模具型腔内的充填状态,从而导致塑件产生变形。
流动距离越长,由冻结层与中心流动层之间流动和补缩引起的内应力越大;反之,流动距离越短,从浇口到制件流动末端的流动时间越短,充填时冻结层厚度减薄,内应力降低,翘曲变形也会为此大为减少。如果只使用一个中心浇口或一个侧浇口,因直径方向上的收缩率大于圆周方向上的收缩率,成型后的塑件会产生扭曲变形;若改用多个点浇口则可有效地防止翘曲变形。
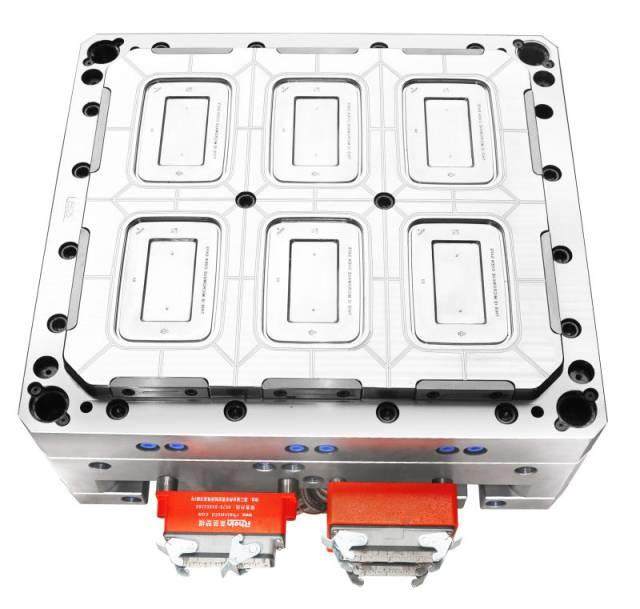
塑料冷却速度的不均匀也将形成塑料收缩的不均匀,这种收缩差别导致弯曲力矩的产生而使塑件发生翘曲。
如在注射成型平板型塑件时,所用的模具型腔、型芯的温度相差过大,由于贴近冷模腔面的熔体很快冷却下来,而贴近热模腔面的料层则会继续收缩,收缩的不均匀将使塑件翘曲。因此,注塑模的冷却应注意型腔、型芯的温度趋于平衡,两者的温差不能太大。
模具上冷却水孔的布置也至关重要。在管壁至型腔表面距离确定后,应尽可能使冷却水孔之间的距离小,才能保证型腔壁的温度均匀一致。同时,由于冷却介质的温度随冷却水道长度的增加而上升,使模具的型腔、型芯沿水道产生温差。因此,要求每个冷却回路的水道长度小于2m。在大型模具中应设置数条冷却回路,一条回路的进口位于另一条回路的出口附近。对于长条形塑件,应采用冷却回路,减少冷却回路的长度,即减少模具的温差,从而保证塑件均匀冷却。
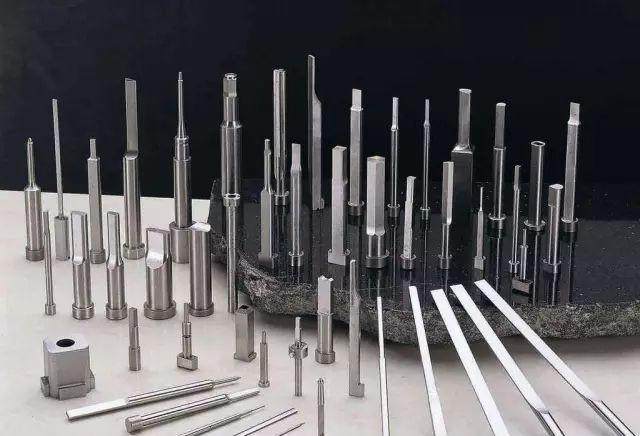
模具顶出的设计也直接影响塑件的变形。如果顶出系统布置不平衡,将造成顶出力的不平衡而使塑件变形。因此,在设计顶出系统时应力应与脱模阻力相平衡。另外,顶出杆的截面积不能太小,以防塑件单位面积受力过大(尤其在脱模温度太高时)而使塑件产生变形。顶杆的布置应尽量靠近脱模阻力大的部分。在不影响塑件质量(包括使用要求、尺寸精度与外观等)的前提下,应尽可能多设顶杆以减少塑件的总体变形。
用软质塑料来生产大型深腔薄壁的塑件时,由于脱模阻力较大,而材料又较软,如果完全采用单一的机械式顶出方式,将使塑件产生变形,甚至顶穿或产生折叠而造成塑件报废,如改用多元件联合或气(液)压与机械式顶出相结合的方式效果会更好。
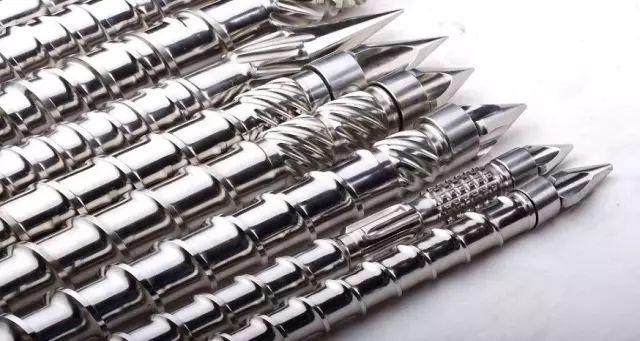
塑化阶段即玻璃态的料粒转化为粘流态,提供充模所需的熔体。在这个过程中,聚合物的温度在轴向、径向的温差会使产品产生应力;另外,注塑机的注射压力、速率等参数会极大的影响充填时分子的取向程度,进而引起翘曲变形。
多级注射控制可以根据流道的结构、浇口的形式及注塑件结构的不同,来合理设定多段注射压力、注射速度、保压压力和溶胶方式,有利于防止翘曲变形的产生。
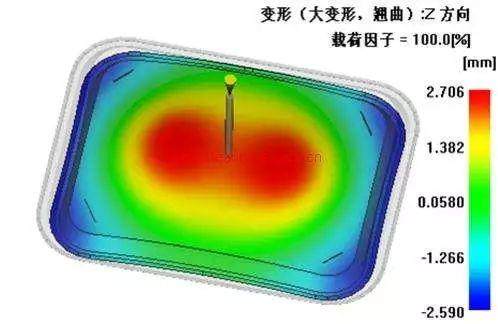
制品收缩本身对翘曲而言并不重要,重要的是收缩上的差异。在注塑成型过程中,熔融塑料在注射充填阶段由于聚合物分子沿流动方向的排列使塑料在流动方向上的收缩率比垂直方向的收缩率大,而使注塑件产生翘曲变形。一般均匀收缩只会引起塑料体积上的变化,只有不均匀收缩才会引起翘曲变形。结晶性塑料在流动方向与垂直方向的收缩率之差较非结晶型的大。
对制品几何形状分析的基础上选择的多级注射工艺,由于制品的壁薄且流长比长,熔体流经必须很快通过,否则易冷却凝固,对此应设定高速注射。但高速注射会给熔体带来很大的动能,熔体流到底时会产生很大的惯性冲击,导致能量损失和溢边现象,这时须使熔体减缓流速,降低充模压力而要维持通常所说的保压压力使熔体在浇口凝固之前向模腔内补充熔体的收缩,这就对注塑过程提出多级注射速度和压力的要求。
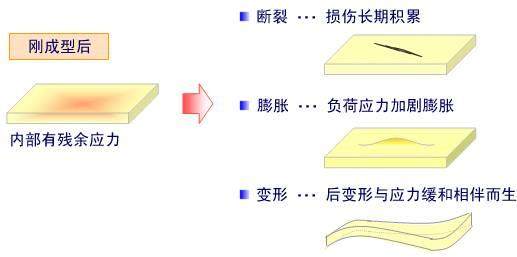
塑料熔体在成型过程中,由于取向、收缩的不均匀,导致内应力的不均匀,所以制品出模后,在不均匀内应力的作用下,发生翘曲变形。
冷却阶段塑料由液态变为固态的相转化和应力松弛行为,对未固化的区域,塑料呈现粘性行为,用粘性流体模型描述,对已固化的区域,塑料呈粘弹行为,用标准线性固体模型来描述。因此,模具开发者或产品开发者可采用粘—弹相转换模型和二维有限元法来预测热残余应力和相应的翘曲变形。
流体表面的速度应该是常数。应采用快速射胶防止射胶过程中熔体冻结。射胶速度设置应考虑到在临界区域(如流道)快速充填的同时在入水口位减慢速度。射胶速度应该保证模腔填满后立即停止以防止出现过填充、飞边以及残余应力。
本文来源: 无锡海天机械有限公司
在线加入艾邦PC群
阅读原文加入艾邦PC群#标签#工艺,注塑#
始发于微信公众号:艾邦高分子