
据外媒报道,西班牙技术中心AIMPLAS获得巴伦西亚地方政府资助,将开展VETERIA21项目,为热塑性复合材料开发新的、更有效的转化工艺,以便可替代电动汽车电池的金属成分。
这些材料可确保大幅减轻车辆重量,从而延长电池寿命。不仅如此,这些材料还可回收,因此符合循环经济。而目前的锂离子电池模块由不锈钢和铝制成,外形大且重,占车辆重量的20%到30%。
相关人员表示:“一般来说,金属部件占汽车重量的73%。因此热固性复合材料是电池外壳的轻质替代品。但其可回收性和生产率不高,而热塑性复合材料具有较高可回收性和生产率,可以作为热固性复合材料的替代物。”
热塑性复合材料逐渐成为汽车减重主要材料。此外,该材料还在机械阻力方面具有优势,且可适应不同制造工艺、具有较短制造周期、能与其他材料结合,并具有可焊接性、易回收性和对循环经济的适应性。
热塑性复合材料的兴起
热塑性树脂和热塑性复合材料已经存在了一段时间,特别是对于短纤维应用。但是,由于越来越需要在不损失结构稳定性的情况下增加轻量化,特别是在汽车工业中,热塑性复合材料引起了新的关注。
一个具体的例子是使用热塑性复合材料来减轻车门内部组件重量的潜力。实际上,一家日本大型汽车制造商最近开始重新设计其内门部件,采用热塑性复合材料。可以相信,这种材料可以使门的重量减少近一半。
热塑性复合材料在复合材料工业中的成功将取决于开发产品和有效工艺的企业。
采用更多的热塑性树脂将不仅使汽车受益,尤其是由于新的商用飞机通常包含超过50%的复合零件。
热塑性复合材料很容易成为运输市场据点的原因很多。与其他材料相比,该材料制成的组件可以焊接,从而减少了对粘合剂的需求,并且可以包覆成型以生产具有卓越机械性能的先进几何形状。
热塑性树脂的普遍优势在于,它们可以无休止地软化和重整,而不会显着降低物理性能。热塑性产品一旦达到其生命周期的尽头,就可以将其熔融并重整以用于新的用途,从而减少了材料浪费。从材料本身的物理特性以及不适合使用热固性材料的潜在新应用中可以发现其他优势。
在热塑性拉挤成型成为主流之前,仍有许多研究需要完成,特别是因为大多数生产方法都适合热固性树脂,因此必须加以调整。
热塑性树脂显示出巨大的潜力,可以生产易于回收的坚固,轻巧的复合材料。尽管现在不是放弃久经考验的热固性复合材料的明智之举,但还是要注意热塑性复合材料的发展,特别是在将可持续性放在首位的情况下。
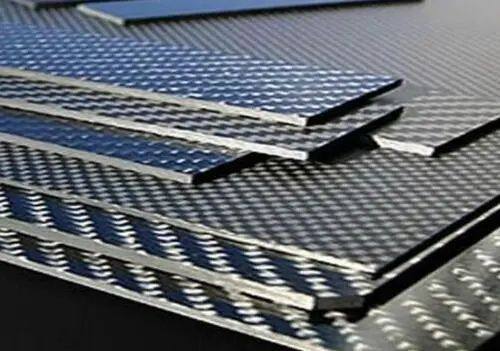
热塑复合材料应用于汽车轻量化配件
复合材料在汽车上的应用复合材料在汽车上主要可应用于发动机罩、翼子板、车顶、行李箱、门板、底盘等结构件中。碳纤维最初主要应于赛车当中,随着车用复合材料技术地不断成熟发展,现在也被广泛地应用于超级跑车和高价值民用轿车上。在商用车应用上,也逐渐从重型卡车中,广泛地延伸到大巴车和轻型小卡。
1、主承载车身结构件为了确保足够的安全性能,在主承载车身结构件上汽车厂商通常要选择强度,刚性及耐冲击性能均很高的材料用于制作主承力结构件,这时环氧树脂碳纤维增强复合材料就成为理想的材料选择。环氧树脂碳纤维增强复合材料具有可设计性,质轻高强,与同体积的铝合金构件相比减重可达50%,耐冲击,耐腐蚀,抗疲劳, 材料寿命长,此类材料制作的主承载车身结构件,不仅大大提高了汽车的安全性,而且降低了车重,减少了燃油消耗,提高了经济性,另外还改善了美观性。
2、次承力结构件次承力结构件主要包括:车门,发罩,行李舱门,前后杠,翼子板,扰流板等部件,其结构大都为层合实体结构和复合材料三明治夹心结构。三明治结构特点:蒙皮选用高强度高模量材料制作,承受较大的弯曲负荷;芯材选用一定刚度和强度的低密度材料,其抗剪切性能突出,可承受较大的冲击载荷;胶结层将蒙皮和芯材连接在一起,承受剪切应力;由于选用低密度芯材,重量会进一步降低。

原文始发于微信公众号(艾邦高分子):【复材资讯】热塑复合材料代替金属可延长电池寿命,还能减重回收,迎发展春天!