1. 激光加工工艺:性能优势突出,契合动力电池生产需求 1.1 动力电池是新能源汽车核心部件,对于电池生产设备要求极高锂离子电池是目前公认的最佳动力电池解决方案,是新能源汽车的重要组成部件。动 力型锂电池主要用于电动汽车、电动自行车、代步车等,又称为锂离子动力电池、动力锂 电等,主要形态分为圆柱、方形和软包电池。由于新能源汽车续航距离、最高时速、电池车重比、能量密度等技术指标均与动力电池密切相关,锂电池质量直接决定新能源车辆的性能,因此,动力电池是新能源车的“心脏”,动力电池的采购成本一般占到新能源汽车整车成本的 30%-40%;动力锂电池主要为三元材料电池及磷酸铁锂电池,下游为新能源车的装机应用。动力电池能量密度及安全性能、生产自动化要求逐步提升,对生产设备的精度、安全 性以及一致性提出高要求。动力电池作为新能源汽车的核心部件,制作工艺复杂,其制造技术和设备要求极高。一方面,政府提高财政补贴门槛,将补贴标准与电池能量密度挂钩, 鼓励企业不断优化工艺,提高能量转换效率、提升能量密度、减轻重量;另一方面,随着各动力电池厂商的产能不断扩大,降低生产成本成为动力电池厂商重要的考虑因素,通过设备自动化,提高生产效率成为必然选择。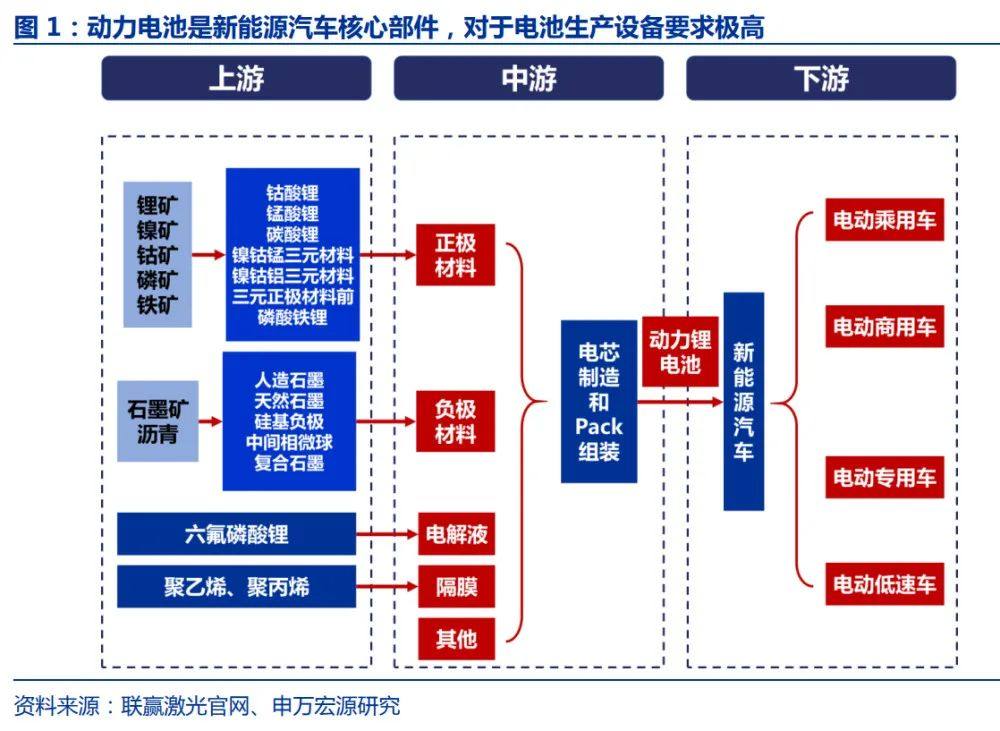
1.2 激光实现对传统加工技术的革新,在动力电池生产中作用突出激光加工技术是对传统加工技术的革新,相较于传统加工技术,具有洁净环保、精度 高、自动化程度高等特点。激光加工可实现多种材料加工目的,它可以对多种金属、非金属进行加工,特别是高硬度、高脆性及高熔点的材料;加工过程无刀具磨损、无接触应力、 不产生噪音、无环境污染。激光加工柔性大,主要用于切割、表面处理、焊接、打标和打孔等。激光工艺凭借多重性能优势,在动力电池产线在发挥重要作用。锂电池的生产制造是 由一个个工艺步骤严密联络起来的,其生产过程大致包括极片制造、电芯制作及电池组装三部分。激光工艺依托高效精密、灵活、可靠稳定、焊材损耗小、自动化和安全程度高等特点,广泛应用于动力电池生产线的前、中、后段加工过程中,具体涉及的激光工艺有激 光切割、激光焊接、激光打标、激光清洗等。动力电池的前段、中段以及后段均有较多激 光技术应用,有效提高了动力电池安全性、可靠性和使用寿命,以及生产的自动化水平。1.3 国内多家激光设备企业崛起,为动力电池厂商提供激光设备由于动力电池制造市场需求旺盛,众多激光企业纷纷抢滩入局锂电激光焊接市场。国 内重要的新能源动力电池厂商纷纷扩建生产线,迎来产能扩张期。与传统加工方法相比, 激光具有精度高、速度快、易于实现自动化等诸多优势,是动力电池生产中不可或缺的标 准工艺。1)联赢激光:2007 年,涉足锂电行业,是国内第一家锂电自动化的激光设备供应商。2017 年,被宁德时代评为“最佳合作伙伴”,并进一步锁定与动力电池行业龙头企业的业务合作关系。作为国内最早从事研发、生产动力电池激光焊接设备的厂商之一,联赢激光 及时跨越了国内激光行业早期的技术门槛,先于竞争对手引入能量控制技术,极大降低自 研激光器的能量波动,实现进口替代,目前为国内激光焊接行业的领军企业。2)海目星:2015 年,开始切入锂电系能源激光及自动化设备市场。公司研发团队打 破国内外技术封锁,研发出激光极片成型设备,能够在锂电池极片两侧的金属箔材上切割 极耳,成功解决行业痛点。海目星动力电池激光及自动化设备产品主要包括:高速激光制 片机、电池装配线、电芯干燥线等,覆盖极片制片、电芯装配、烘烤干燥等动力电池生产 关键工艺流程。2. 激光锂电设备:用于前中后段加工,成动力电池产线标配 2.1 应用环节:涵盖锂电多个工序环节,助力电池性能及生产效率提升锂电池的生产制造包括极片制作(前段)、电芯组装(中段)以及后处理(后段)三部分;动力电池的前段极片制作、中段焊接以及后段模组 Pack 均有较多激光技术应用。(一)极片制作工段-前段:激光切割工艺应用于极片及隔膜分切环节极片制作工段具体包括匀浆、极片清洗、涂布、碾压、极片及隔膜分切环节,在极片 及隔膜分切环节中,激光切割机已经成功实现对传统模切机的替代。在激光技术出现前, 锂电池产业通常使用传统机械进行加工和切割,但使用传统模切刀设备会不可避免出现磨 损,粉尘掉落并产生毛刺,进而引起电池过热、短路、甚至爆炸等各类危险问题。与传统 的机械切割相比,激光切割拥有无工具磨损、切割形状灵活、边缘质量控制、精确性更高 和运营成本较低等优势,有利于降低制造成本、提高生产效率、大幅缩短新产品模切周期。(二)电芯组装工段-中段:激光焊接工艺应用于壳体、顶盖、密封钉、极耳等焊接环节电芯组装工段具体包括电芯的卷绕、叠片、极耳焊接、电芯入壳、外壳顶盖焊、注液、 注液口封装等。电芯是动力电池的最小单位,电芯的质量决定了电池模组的性能进而影响整个动力电池系统的可靠性。其中,激光焊接工艺应用于壳体、顶盖、密封钉、极耳等焊接环节,以及电芯前的配件防爆阀的焊接环节。相比传统氩弧焊、电阻焊的方式,激光焊接具有显著优势:一是热影响区窄,焊接变形小,特别适合于微型件的焊接;二是通过光 导纤维引导或棱镜偏转,可远距离施焊;三是具有极高的能量密度;四是不需要真空防护 和 X 射线防护,也不受磁场影响。(3)后处理工段-后段:激光自动化系统替代传统手工装配方式应用于模组 PACK后处理工段具体环节包括化成分容、测试分档、PACK 模组,主要设备包括化成机、 分容检测装置、过程仓储物流自动化,PACK 自动化设备。其中,激光自动化系统普通应 用于模组 PACK 组装产线,进行电池 PACK 模组时的连接片焊接。2.2 激光切割:高效精准,锂电池制造领域的“利器”激光切割是利用高功率密度激光束来实现切割的工艺,在动力电池生产中主要应用于 前段工序的电池极片制造环节。激光切割是利用经聚焦的高功率密度激光束照射工件,使 被照射的材料迅速熔化、汽化、烧蚀或达到燃点,随着光束对材料的移动,孔洞连续形成 宽度很窄的切缝,从而实现切割的技术。激光切割在锂电池制造中的应用主要包括正负极的激光极耳切割成型、激光极片切割、激光极片分条,以及隔膜的激光切割;其中,激光极耳成型是目前激光切割在锂电池制造领域最主要的应用。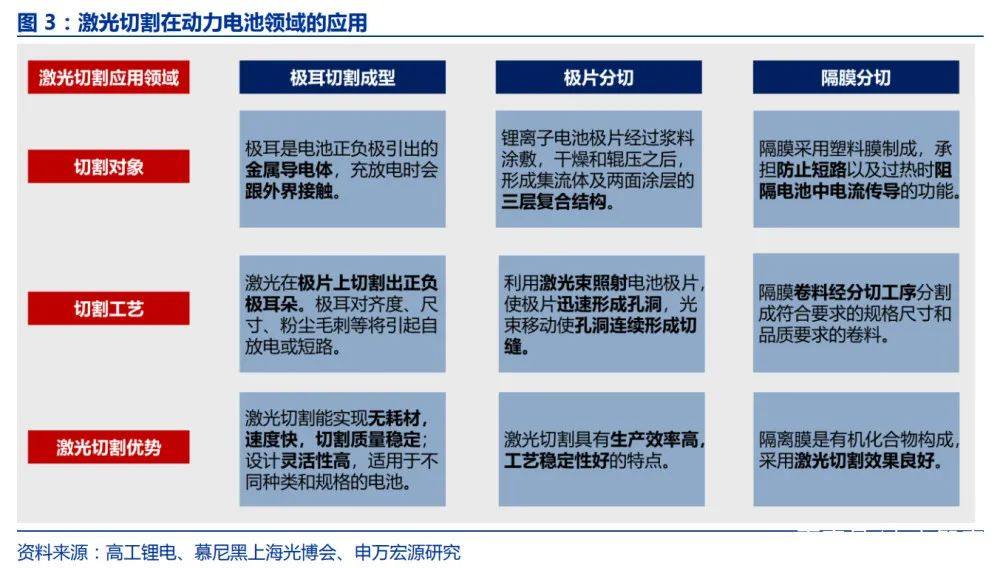
激光切割作为先进加工工艺,具有精度高、速度快、自动化水平高等优势,主要替代 传统模切机。在激光技术出现前,锂电池产业通常使用传统机械进行加工和切割,而模切刀在使用过程中,会不可避免地出现磨损,进而掉落粉尘、产生毛刺,可能引起电池过热、 短路、爆炸等危险问题;且五金模切工艺存在模具损耗快、换模时间长、灵活性差和生产效率低等局限性,已越来越不能满足锂电池制造的发展要求。与传统的机械切割相比,激光切割拥有无工具磨损、切割形状灵活、边缘质量控制、精确性更高和运营成本较低等优势,有利于降低制造成本、提高生产效率、大幅缩短新产品模切周期。在动力锂电池的极耳加工环节中,激光极耳切割已成为行业标配。2.3 激光焊接:高度契合,锂电池制造领域的“粘合剂”激光焊接是利用激光束对物体进行融化并实现焊接的工艺,在动力电池生产中主要用 于中段电芯、后段模组 PACK 环节。激光焊接是利用激光束优异的方向性和高功率密度等特性进行工作,通过光学系统将激光束聚焦在很小的区域内,在极短的时间内使被焊处形成一个能量高度集中的热源区,从而使被焊物熔化并形成牢固的焊点和焊缝。作为一种高精密的焊接方式,其极为灵活、精确和高效,能够满足动力电池生产过程中的性能要求, 是动力电池制造过程中的首选。在动力电池的生产中,使用激光焊接的环节主要包括:电 芯配件中的防爆阀焊接;中道工艺:极耳的焊接(包括预焊接)、极带的点焊接、电芯入壳的预焊、外壳顶盖密封焊接、注液口密封焊接等;后道工艺:包括电池 PACK 模组时的 连接片焊接等。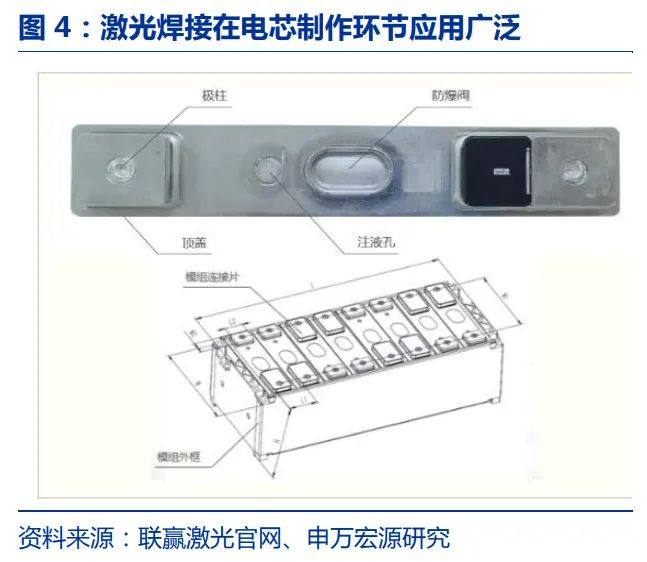
1)电池防爆阀焊接:电池的防爆阀是电池封口板上的薄壁阀体,当电池内部压力超过规 定值时,防爆阀阀体破裂,避免电池爆裂。安全阀结构巧妙,这道工序对激光焊接工艺要求极为严格。没有采用连续激光焊接之前,电池防爆阀的焊接都是采用脉冲激光器焊接,通过焊点与焊点的重叠和覆盖来实现连续密封焊接,但焊接效率较低,且密封性相对较差。采用连续激光焊接可以实现高速高质量的焊接,焊接稳定性、焊接效率以及良品率都能够 得到保障。2)电池极柱焊接:电池盖板上的极柱,分为电池内部和电池外部连接。电池内部连接, 是电芯极耳与盖板极柱的焊接;电池外部连接,是电池极柱通过连接片焊接,形成串联、 并联电路,组成电池模组。电池的极柱即电池的正负极,一般正极采用铝,负极采用铜。常用的结构为铆压结构,铆压完成后进行满焊,其大小一般为直径 8 的圆。焊接时,在满足设计要求的拉力和导电性能的情况下,优先选择光束质量好、能量分布均匀的光纤激光 器或是复合焊激光器,采用光纤激光器、复合焊激光器焊接可以实现的电极柱的铝-铝结构 焊接、铜-铜结构焊接稳定性,减少飞溅、进而提升焊接良率。3)转接片焊接:转接片与软连接是连接电池盖板与电芯的关键部件。它必须同时考虑 到电池的过流、强度及低飞溅的要求,所以在与盖板的焊接过程中,需要有足够的焊缝宽度,且需要保证没有 particle 落在电芯上,避免出现电池短路。而作为负极材料的铜,属 于低吸收率的高反材料,在焊接时需要更高的能量密度去焊接。4)壳体封口焊接:动力电池的壳体材料有铝合金和不锈钢,其中采用铝合金的最多, 也有少数采用纯铝。不锈钢是激光焊接性最好的材质,无论是脉冲还是连续激光都能够获得外观和性能良好的焊缝。使用连续激光器焊接薄壳锂电池,效率可以提升 5~10 倍,且外观效果和密封性更好。现在为了追求更快的焊接速度和更均匀的外观, 大部分公司已经开始采用复合焊和环形光斑取代以往低速的单光纤焊接。5)密封钉(电解液注入口)焊接:密封钉(注液孔盖帽)的形式也较多,其形状通常 为一个直径 8mm、厚度约 0.9mm 的圆形盖帽,其焊接的基本要求就是耐压值达到 1.1MPa,密封且不能有针孔、裂纹和爆点的存在。作为电芯焊接的最后一道工序,密封钉 焊接的良率尤为重要。密封钉焊接时由于有残留电解液的存在,导致有爆点、针孔等缺陷, 而抑制这些缺陷的关键方式则是减小热输入量。6)动力电池模组及 PACK 焊接:电池模组可以理解为锂离子电芯经串并联方式组合, 并加装单体电池监控与管理装置。电池模组的结构设计往往能决定一个电池包的性能和安全。其结构必须对电芯起到支撑、固定和保护作用。由于铜和铝之间采用激光焊接后易形成脆性化合物,无法满足使用要求,通常采用超声波焊接;铜和铜、铝和铝一般均采 用激光焊接。同时,由于铜和铝传热均很快,且对激光反射率非常高,连接片厚度相对较大,因此需要采用较高功率的激光器才能够实现焊接。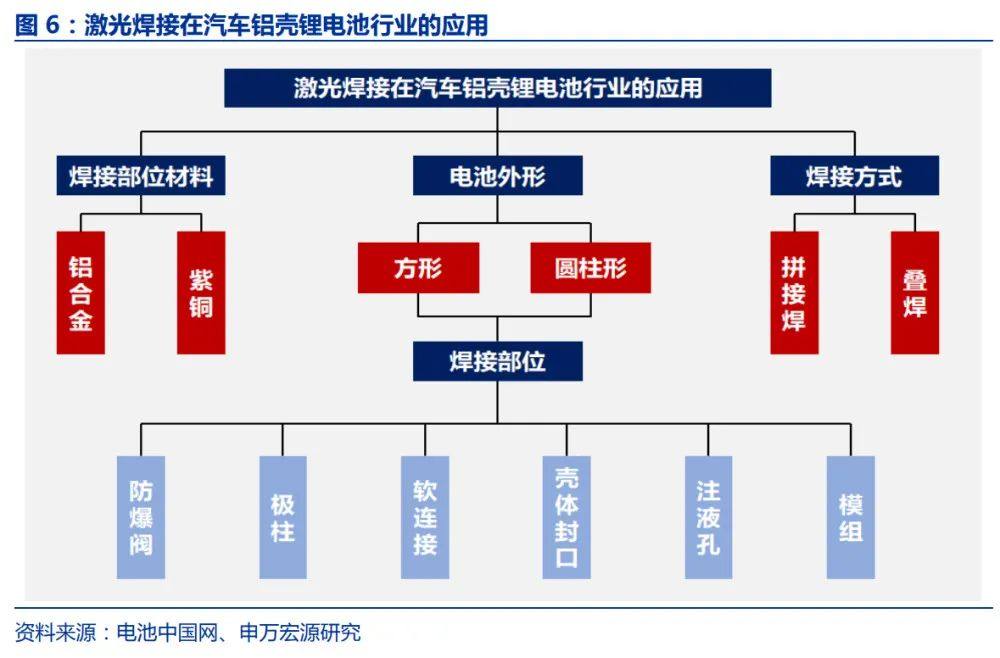
在动力电池应用方面,相比于传统电弧焊、电阻焊等,激光焊接具有材料契合度高、 高效精密、自动化集成的优势。激光焊接优势明显。1) 材料契合度高:动力电池壳体多为铝材材质,更适合使用激光进行焊接,激光焊接防止飞 溅和气孔,有利于提升电池良品率及安全性能;2)高效精准:传统的氩弧焊、电弧焊都是 通过接触式焊接,降低了焊接速度,激光能量密度高,热影响区变化范围较小,属于非接触焊接,焊接速度快,加工精度高,变形小;3)自动化集成:激光焊接系统具有高柔性, 与机器人联合组成的焊接系统可以形成多功能的激光加工系统,易实现自动化生产。特别值得注意的是,在动力电池行业,激光焊接相较于切割及打标具有定制化、客户 粘性强等特点,进入壁垒更高。1)激光焊接设备呈现非标定制化的特点。产品由客户根据自己的产品确定技术指标, 行业内以宁德时代的技术指标最为先进。动力电池行业的激光焊接设备主要有:密封钉焊接系统、顶盖焊接系统、软连接焊接系统、极柱焊接系统、防爆阀焊接系统、PACK 及模组焊接系统等;依据下游客户的场地限制、自动化水平、技术要求等,需要重新进行定制化设计。2)激光输出的稳定性控制。为了对焊件输出统一、稳定的焊接激光束,就需要激光输 出功率具有良好的一致性以及能够精确控制激光输出功率,功率过低会导致焊接熔融不足而影响焊接质量,功率过高或上下波动会导致飞溅、气孔等不良效果。同时部分重要的工业材料如铝、铜等材料, 采用激光焊接方式呈现高反射性、难焊特点,容易形成飞溅、裂纹和气孔,影响焊接质量 和效果,因此研发设计具有针对性的激光器就显得尤为重要。3)针对不同的焊接材料设定 激光焊接工艺参数。包括激光光束属性、光束聚焦及焦点特性、辅助气体特性、加工材料 性质、合适的夹具及机械件等多项工艺参数,以达到最优焊接效果。4)焊接工艺技术参数及要求会影响激光器的选择、自动化传动装置、夹治具、控制软 件等的设计开发。在研发设计过程中,需要对激光光源有着比较深刻的了解和研究,如激 光的波长范围、激光的能量密度、激光的焊接的速度、激光焦点和材料的位置关系等,并且要理解材料特点。3.1 驱动力一:新一轮动力电池扩产到来,激光锂电设备需求高涨动力电池行业与新能源汽车行业息息相关,政策驱动下,新一轮动力电池投资扩产高 拉动设备需求提升。在全球范围内,新能源汽车取代传统燃油汽车趋势明显,2019 年,全 球新能源汽车市场渗透率仅为 2.5%,尚处于发展初期,2020 年新能源汽车销量接近 10% 的增长。到 2025 年, 我国新能源汽车新车销量占比达到 25%左右;中国动力电池市场占据全球动力电池市场份额 50%以上,成为全球第一大动力电池市场。在政策驱动下,激光锂电设备市场需求或迎 来高速发展。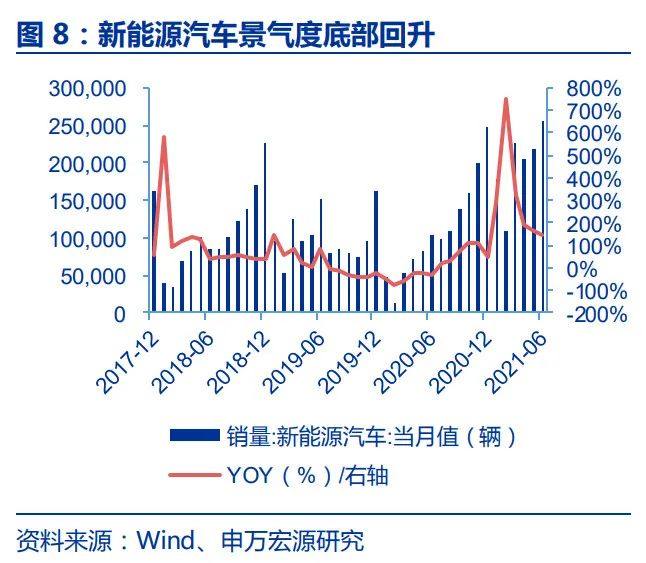
受益于新能源市场景气度回升,动力电池厂商扩产加速,拉动锂电设备 3-5 年高需求。动力电池厂商扩产的进度受下游整车销售情况影响,2020 年下半年以来新能源汽车销售火 爆,新能源产业链景气度持续提升。现阶段,动力电池厂商同步在现有产能基础上大幅扩 产,激光锂电市场有望收益实现突破。2020 年动力电池投扩项目 26 起, 总金额超 1370 亿元,扩产规模超 400GWh。新增投资项目中,单个项目的产能规模基本 在10GWh,百亿级投资项目大幅增加,其中宁德时代 7 个生产基地新增产能规划达535GW, 中航锂电“十四五”期间,规划产能超过 300GWh;预计未来 3-5 年新能源汽车行业增速 呈喷井态势,下游动力电池厂商扩产投资热潮持续不减,将推动锂电设备需求快速增长。3.2 驱动力二:动力电池性能要求提升,激光设备更迭进程加速动力电池能量密度及安全性能逐步上升,对激光加工设备提出更高要求。自 2008 年锂 离子动力电池应用于电动汽车已经 10 年,实际装车产品的能量密度从 100 瓦时/公斤提升到 250 瓦时/公斤,提高了 2.5 倍。2020 年的能量密度将达到 300 瓦时/公斤。向高能量密度发展是动力电池的 必然趋势,但在现有的材料体系下,能量密度的提升将导致电池的热稳定性变差,造成安 全性风险,从而对激光加工设备的技术与工艺提出了更高的要求。激光器的更新迭代较快,企业为保障领先于竞争对手而主动进行设备替换。随着近年 来激光行业的快速发展,激光器的更新迭代速度较快,市场上每隔一段时间会推出更高功 率和更好光束质量的激光器,促进激光行业整体向更高精度和更快效率不断发展,下游客 户对加工要求也会逐渐提高,原有较低功率和较差光束质量的激光设备将逐渐无法满足市 场新的要求,设备使用商为保障先进加工能力,将不断淘汰老旧设备、更替新设备。同时, 磨损及老化等因素导致激光设备加工效率下滑,倒逼企业进行设备更替。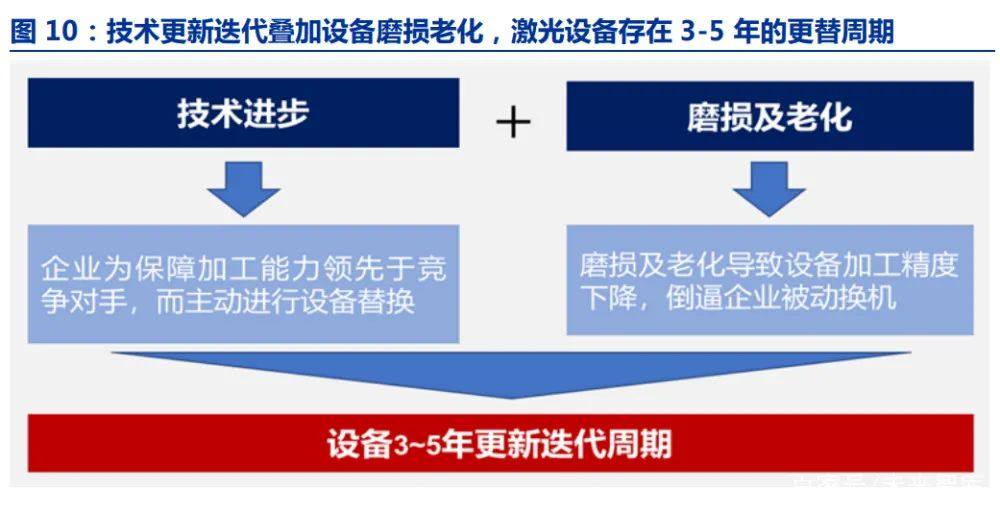
3.3 驱动力三:储能领域或迎来黄金期,锂电市场有望充分受益储能领域是锂电池的崭新领域,电源、电站、电池三者并驾齐驱。动力型锂电池主要 用于电动汽车、电动自行车、代步车等;储能和工业型锂电池主要用于调峰电源、储能电 池等储能产品和电动工具等产品的锂电池电芯及模组。而锂电池在循环寿命、快速充放能 效、比能量方面均大幅优于铅酸电池,在安全性方面与铅酸电池相当,作为一种绿色环保 的新型电池,在储能领域有很好的应用前景。随着通信运营商集中采购,以通信储能为代表的储能锂电池市场有望迅速增长。储能锂电池 2025 年有望达 58Gwh 装机量,有利于带动激光锂电应用增长。2020 年中国储能市场规模达到 175 亿元,同比增长 35%。储能锂电池出货量达 到 16.2GWh,同比增长 70.53%。随着政策对新型储能支持力度加大、电力市场商业化机 制建立、储能商业模式清晰、锂电池成本的持续下降。预测至 2025 年,中国储能 锂电池出货量将达到 58GWh,市场规模超过 550 亿元。3.4 预计 2025 年激光锂电自动化设备需求约 430 亿激光技术在动力电池中承担核心功能,假设激光锂电自动化设备在整线中的价值量占 比为 30%。锂电设备生产中涉及的激光工艺主要为激光焊接、切割和自动化模组,激光焊接的价值量在锂电设备中占据 10-15%;而激光切割及自动化设备, 在前段、中段产线中均有重要应用,因此,假设激光自动化设备占产线价值量投资比例为 30%。新能源车销量增长带动锂电设备市场,预计 2025 年激光锂电自动化设备需求约 430 亿。2020 年我国汽车整体销量达 2526.76 万辆,新能源汽车销量为 132.29 万辆,渗透率 仅为 5.24%。假设一:2025 年新能源汽车 渗透率逐步提升至 26%,即可测算每年新能源汽车销量(每年汽车销量*新能源汽车渗透率);假设二:单车带电量历年平均值为 50KWH,假设未来 5 年稳步提升,即可测算每年装机 量(每年新能源汽车销售*单车带电量);假设三:据高工锂电测算, 近年动力电池单 GW H 设备投资额约为 1.7-1.9 亿元,考虑技术逐步成熟、设备性能提升, 假设未来 5 年每 GWH 设备投资额小幅降低,即可测算每年设备需求规模(每年产能新增 扩产*每 GWH 设备投资额);假设四:假设激光设备占整线价值量投资比例为 30%;即可 测算出每年激光锂电设备需求规模(每年设备需求规模*激光锂电自动化设备价值量占比), 2025 年激光锂电设备需求规模约 430 亿元。
原文始发于微信公众号(锂电产业通):一文讲清楚锂离子电池用激光设备!
欢迎关注艾邦锂电产业微信公众号;锂电池产业链交流、资讯、人脉圈。从正负极材料生产到涂布,隔膜、电解液、封装材料到检测组装等这些环节涉及的材料、辅材、添加剂、耗材,以及相关设备,相关企业介绍。
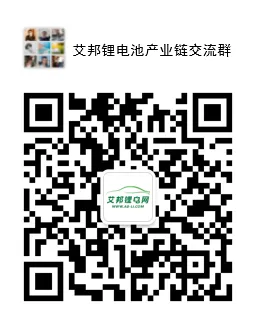