
燃料电池单堆功率的持续突破促使发电活性面积不断增加,会导致活性区内电流分布一致性变差,丰田、本田、宝马等车企都把分区诊断技术作为燃料电池设计开发阶段的重要手段。
车用燃料电池堆通常由数百个燃料电池发电单元组成,单个电池的活性面积在250~350 c㎡区间内。保证每个发电单元平面各局部区域物理参数的均匀性和一致性是燃料电池设计和开发的重要环节。在燃料电池发电平面内,反应气在气体流动的方向上逐渐消耗,生成水逐渐积累,冷却液流动方向上温度逐渐变化,多项物理参数包括湿度、温度、浓度、气压等在内,在平面上存在分布差异,显示出电流密度分布不均匀。
△燃料电池发电平面电流密度差异现象
如果电流密度分布差异过大,则活性面积各区域物理操作参数差异较大。短期内,局部电压差形成面内电流并导致电压损失,性能下降,反应气利用率低,从而导致低效率和高成本。从长远来看,局部区域气体不足和高温会对电堆的耐久性造成威胁。因此,在极板结构设计、机理诊断、电极梯度设计、操作工况设计等阶段,要密切关注发电平面内物理参数的分布一致性,尤其是电流密度分布。
△温度分布测量案例
△水含量分布测量案例
电流密度实质上代表每单位活性面积每单位时间内氢气和氧气的反应量(或水的生成量)。在传统的燃料电池流场(如直流场)中,大量燃料在反应活性区入口处参与电化学反应,一般呈现高电流密度区;由于气体沿流路扩散并参与反应,当到达活性区出口时,大部分的氢气和氧气已被消耗,反应物浓度较低,表现为低电流密度区。因此,在整个发电平面中,电流密度分布存在很大差异。
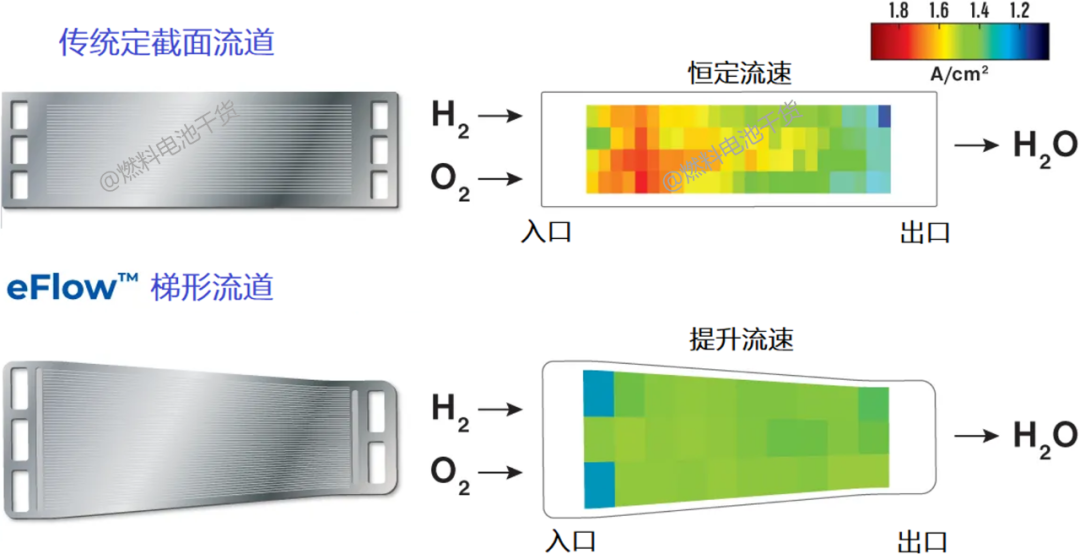
△极板电流密度分布对比(路普能源)
加拿大路普能源发现,通过分区电流,传统的极板流场(固定截面)的电流密度分布误差达到43%。其eFlowTM技术的梯形双极板设计,由于气体流道变窄而增加了气体流速,使电流密度分布误差降低到5%,保证了全板电流密度分布的一致性。电流密度分布的高一致性最终使电堆的峰值体积功率密度提高了90%,由于计量比的降低,燃料消耗降低了16%。
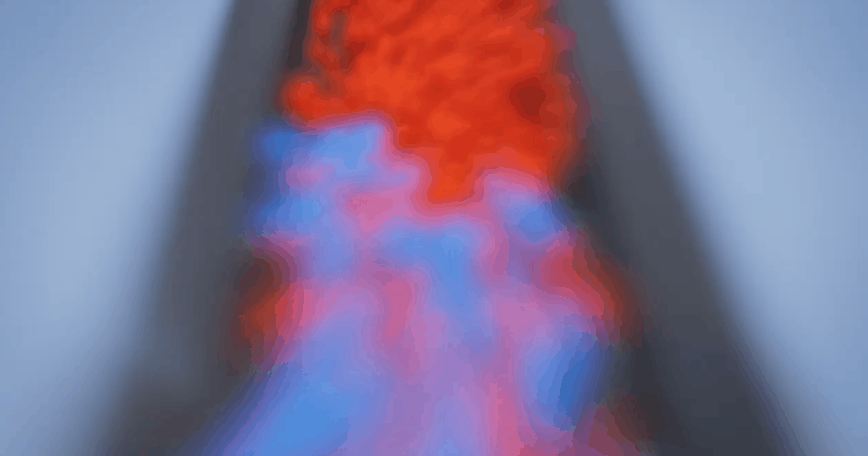
整体或局部欠气一直是难题,尤其是阳极部分缺气。在反向电流机制下,阳极部分欠气可形成阴极的高电位,然后碳载体发生腐蚀。在常见的氢-空逆流进气结构下,阳极水管理备受关注。随着电化学反应的进行,从阳极活性区入口到活性区出口的氢气分压逐渐降低,水蒸气分压升高,出口区域“水淹”风险高,随时可能出现局部欠气。
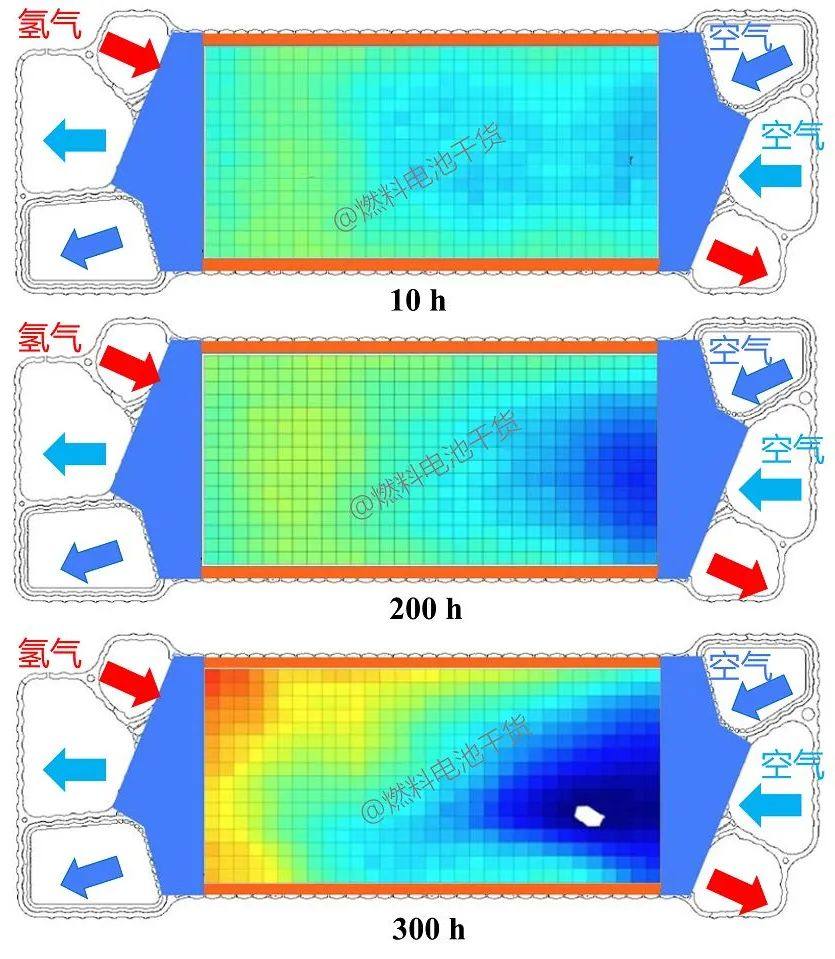
宝马在电堆(活性面积287.9 c㎡)在不同时间经历整车工况的耐久性测试时,通过S++分区电流法发现,在耐久性测试过程中,阳极入口区域的电流密度逐渐增大,而出口区域的电流密度逐渐减小。经过300h的耐久性试验后,甚至出现负电流(上图白点处)。宝马分析,这一现象主要是由于阳极出口水淹造成局部欠气所为,导致阴极碳腐蚀,这一点通过SEM表征和氢气计量比敏感性实验验证。通过SEM表征发现,与阳极进口区域的阴极多孔介质相比,阳极出口对应的阴极多孔介质发生具有腐蚀性和塌陷性。通过氢气计量比的敏感性发现,当氢气计量比从1.4增加至1.8,阳极出口处电流密度分布得到很大改善。
燃料电池的输出性能受多种操作条件的影响,如气体压力、气体流量、气体湿度、氢空压差和电堆温度等。合理的操作工况,可以有效避免“水淹”和“膜干”状态,提高燃料电池运行的稳定性,提高氢利用率,降低辅助功耗。发电区的含水量分布间接反映了气体浓度的分布,对燃料电池的可靠运行和寿命有很大的影响。局部含水量过高,可能引发欠气导致催化层衰减;局部含水量过低,可能导致欧姆阻抗增加和质子膜衰减。含水量分布深受操作条件的影响,通过操作条件优化含水量分布也是开发阶段的一项重要工作。
△水含量分区表征设备和结果示意(本田)
本田通过分区分布实验和仿真方法,优化了6种对含水量影响较大的操作条件(阴阳极气体压力、阴阳极气体流量、冷却液入口温度和冷却液流量)结果表明,膜电极发电平面内水含量最小值可通过冷却液入口温度和阴极气体入口压力来控制,最大值可通过冷却液入口温度、阴极气体入口压力和阴极气体流量控制。
△水含量分布优化
为了充分发挥膜电极的性能,梯度化设计理念被引入到膜电极结构中,并已应用于商用化的燃料电池产品中。与传统膜电极中物质的无序分布状态相比,梯度化设计可以根据设计目标在空间上将离聚物与孔隙等有序分布。目前,膜电极的梯度化主要包括催化层中离聚物与催化剂的梯度化、气体扩散层中疏水性和孔隙率的梯度化。
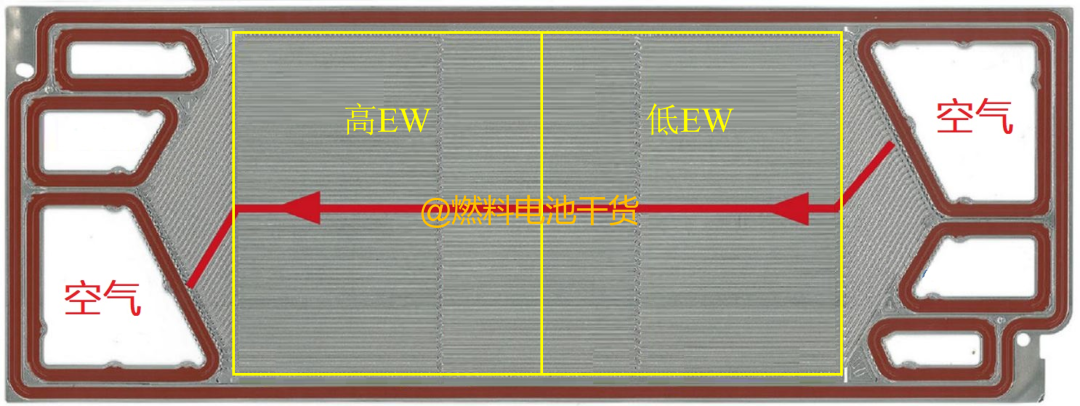
由于低EW树脂储水含量更高,通常在低湿度下具备较好的性能,但在高湿度下由于溶胀传质损失更高。此外,宝马通过S++燃料电池密度与温度测试系统进行分区电流、温度测试发现,尽管车规级燃料电池阴极入口温度较低,但“膜干”现象依然出现。因此,宝马制备了在发电平面方向上离聚物EW呈现梯度化分布的膜电极,即空气入口区域为低EW聚合物,空气出口区域为高EW聚合物。结果表明,该离聚物EW呈梯度化分布的膜电极在2.9 A/cm2下性能提升约13%。
S++ Simulation Services(以下简称S++)是一家德国公司,多年来一直专注于燃料电池的电流密度分布测量装置的研发和制造,为客户提供相关的产品以及解决方案。
S++ Simulation Services可以按照客户的要求完成设备的定制,未来将持续研发用于电流密度分布测量,空间分辨阻抗谱和单电池电压测量的设备,以满足用户更高的需求。S++ Simulation Services的使命是通过数学建模、仿真以及测量技术来支持燃料电池的开发。
△S++燃料电池密度与温度测试系统
在燃料电池局部条件不同的情况下,会导致不均匀的质量转换,导致不均匀的电流生产。深入了解PEM燃料电池、DMFC 等电化学电池的关键之一是测量电流密度分布。在大型燃料电池中,这对于节省和可靠的操作以及高寿命是很重要的。
S++燃料电池密度与温度测试系统的测量单元是由小型变压器组成的。磁性材料的磁导率取决于磁化强度和温度。被测量的电流Im流过线圈L1,并引起磁性材料的磁化(虚线)。交流电i(t),提供给 L2,诱导电压 u(t)进入线圈L3。这个电压取决于磁性材料的磁导率(虚线)。所以Im的大小具有决定权。
单个测量单元按行和列串联进行,交流电i1(t)到in(t)将被连续输入矩阵以激活行1到n。u1(t)到un(t)的电压将被采集为测量信号。测量单元不被交流电激活,不会向测量信号传递任何信息。一般来说,用2n对导线可以达到n²个测量点。因此, 连接电线、控制和评估电子的复杂性是线性的!这样,可以很容易地为任意大型燃料电池建立测量装置。
△以3×3测量单元为例
下图显示了一个定制的传感器板,其活动面积为 800cm²,46x36个测量单元。几乎任何设计都是可能的,测量单元的最小尺寸为7x7mm,最大尺寸受到他们必须测量的电流的限制。
△定制的传感器板
S++燃料电池密度与温度测试系统在燃料电池中可提供详细的流场分析、材料详细分析、燃料电池优化、燃料电池故障诊断、分辨率约7×7毫米、最高可测电流3A/cm²、最高可测温度180°C、有标准型号也可客制化。
△S++燃料电池密度与温度测试系统软件界面
S++燃料电池密度与温度测试系统也适用于大型燃料电池。它通过USB连接到任何电脑,使用便捷!
- End -
原文始发于微信公众号(艾邦氢科技网):车用燃料电池的分区设计和诊断—S++燃料电池密度与温度测试系统
