本篇文章主要介绍了两种复合材料成型工艺,分别是:HP-RTM和湿法模压成型工艺。
HP-RTM成型工艺
HP-RTM是英文High Pressure Resin Transfer Molding的简写,全称是高压树脂传递模塑成型工艺,简称HP-RTM成型工艺。它是指利用高压压力将树脂对冲混合并注入到预先铺设有纤维增强材料和预置嵌件的真空密闭模具内,经树脂流动充模、浸渍、固化和脱模,获得复合材料制品的成型工艺。
上述介绍中关键词介绍:
高压压力:这里的高压是相对于传统RTM(Resin Transfer Molding)工艺而言,HP-RTM把注胶压力提升到80bar。高压注胶的好处是树脂可以更快的达到每个拐角,因此可以提高产品的纤维含量,提高产品性能,对于造型复杂的零件更加适用;
预先铺设:这里预先铺设的纤维增强材料是指已经经过剪裁预成型的纤维材料;
预置嵌件:嵌件是指在成型前放置于模具里的零件,材质有金属和非金属,这样使得成型后的制品,嵌件被包入本身的结构中,不可拆卸。是否需要预置嵌件由制品的结构设计决定。
以上流程可以通过一个简单的工艺流程图来体现:
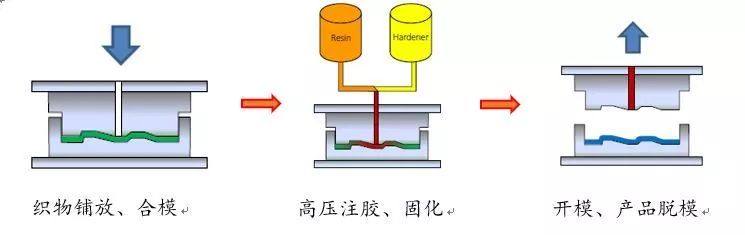
前面提到HP-RTM成型工艺是相对于传统RTM工艺而言进行优化后的成型工艺,在不同的优化方向上,也相应开发出了其它的以RTM工艺为基础,进一步提高生产效率和制品性能的工艺,比如现在HRC拥有的HP-CRTM(High Pressure Compression Resin Transfer Molding)成型工艺.
HP-CRTM成型工艺是在HP-RTM工艺技术中的树脂注胶前,将模具上移0.5~1mm,增大密封模腔间隙,模具可以有更宽的浇道,降低树脂流动阻力,注胶结束后再将模具在高压下完全闭合,树脂体系随闭合压力流动充模,成型压力相对较低,这样既保证纤维不乱纹,又保证了较高的注射速度。
工艺流程图体现为:
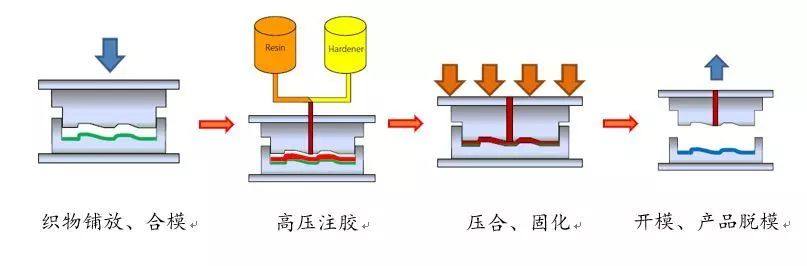
HP-RTM成型工艺是现在广泛应用在多行业的复合材料成型工艺之一,它的优点在于可能实现相对于传统RTM工艺的低成本、短周期、大批量、高质量生产(良好的制件表面),在汽车制造、造船、飞机制造、农业机械、铁路运输、风力发电、体育用品等多行业均有应用。
下面,我们来看一些采用了HP-RTM成型工艺及衍生的其它相关工艺得到的具体制品:
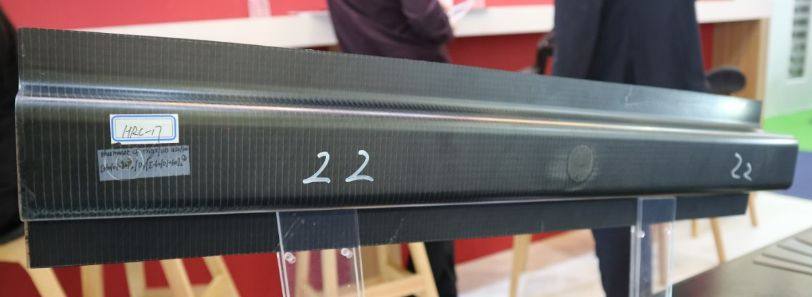
碳纤维电动滑板
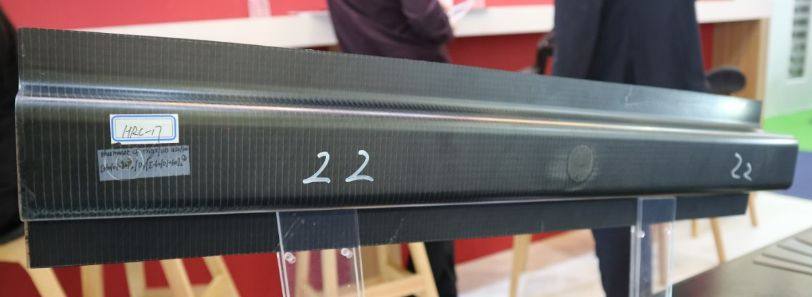
碳纤维帽型梁
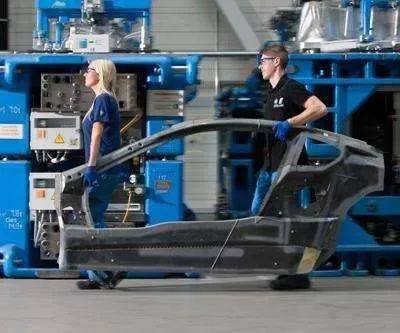
BMW i8 车身侧框架
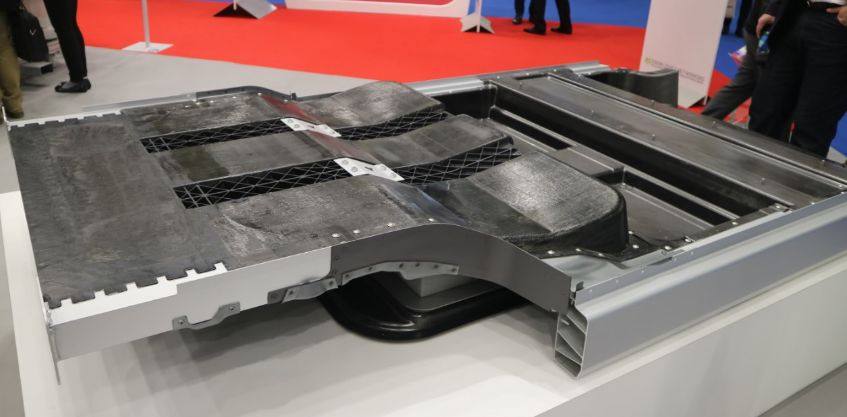
AUDI AG的碳纤维底板模块,
成型工艺中应用了Ultra-RTM工艺
参考资料:
1. 微信公众号:复材人生 《一键进入带你了解HPRTM工艺》
2. https://www.compositesworld.com/articles/hp-rtm-on-the-rise
湿法模压成型工艺
本期推送介绍的第二个成型工艺是湿法模压工艺,也称WCM(是Wet Compression Molding的简称)工艺,先来看相关的工艺流程图:
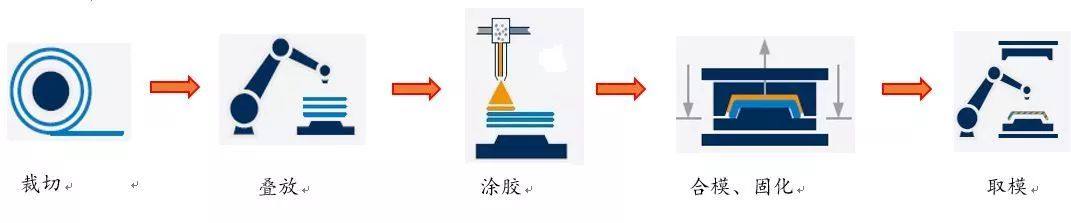
将湿法模压工艺的成型步骤可分解如下:
1、使用裁切好的碳纤维或玻纤干布铺放成平面;
2、将材料转移在模具上;
3、进行涂胶,使树脂覆盖纤维;
4、进行合模,抽真空、加压,加热固化;
5、开模,取出产品。
湿法模压工艺最主要的特点是前期裁切使用干的纤维布,先进行喷涂树脂之后再放入模具进行成型固化,这也致使该工艺更适合加工形状复杂程度低(2D或2.5D造型)的制品,应用行业广泛,其优点是批量生产节拍快,模具设计简单,单件成本低。
下面分享几组应用湿法模压工艺得到的制品及案例:
我们将上述关键词串起来就得到了基本工艺流程,如下图:

碳纤维mini机盖
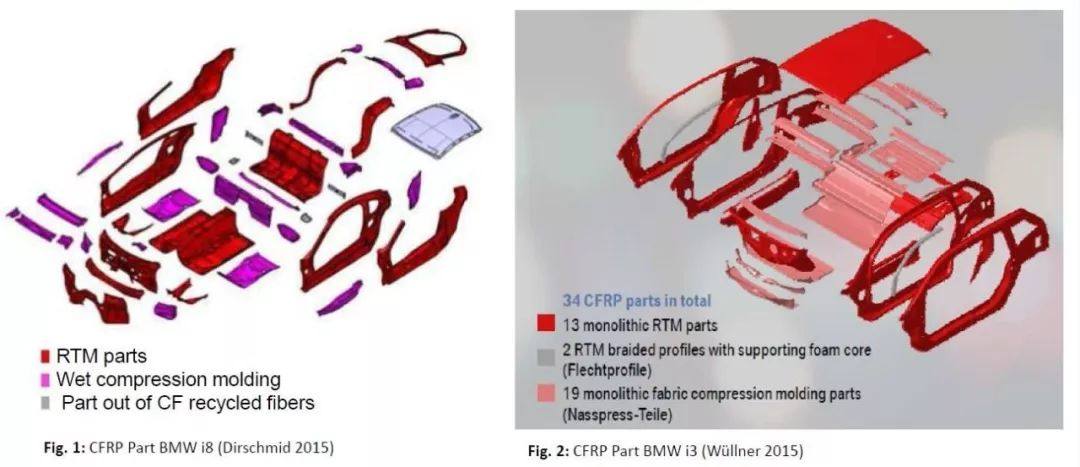
上图是湿法模压工艺在BMW i3和i8车型中应用图示,其中在BMW i3(右)中使用了17个“湿压部件”,在i8(左)中使用了21个。
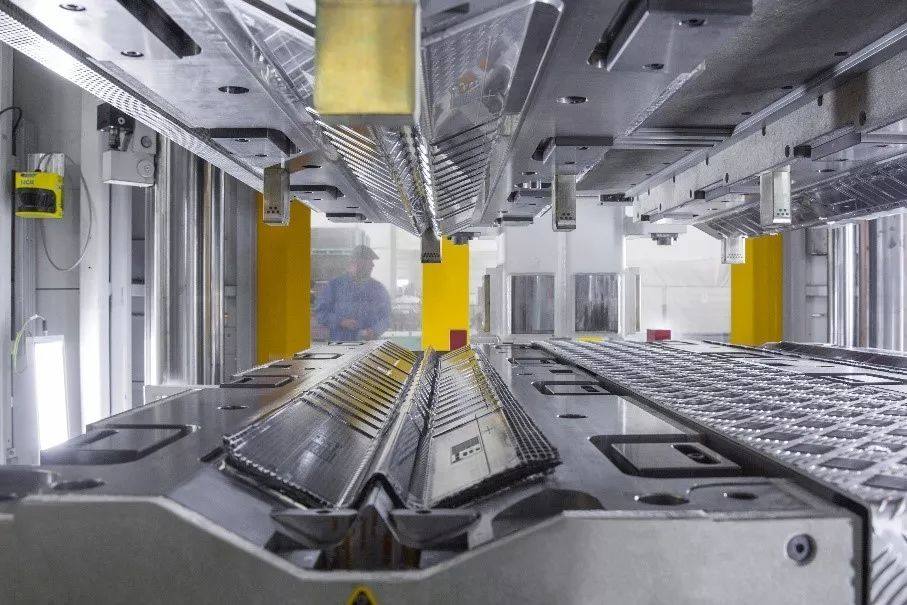
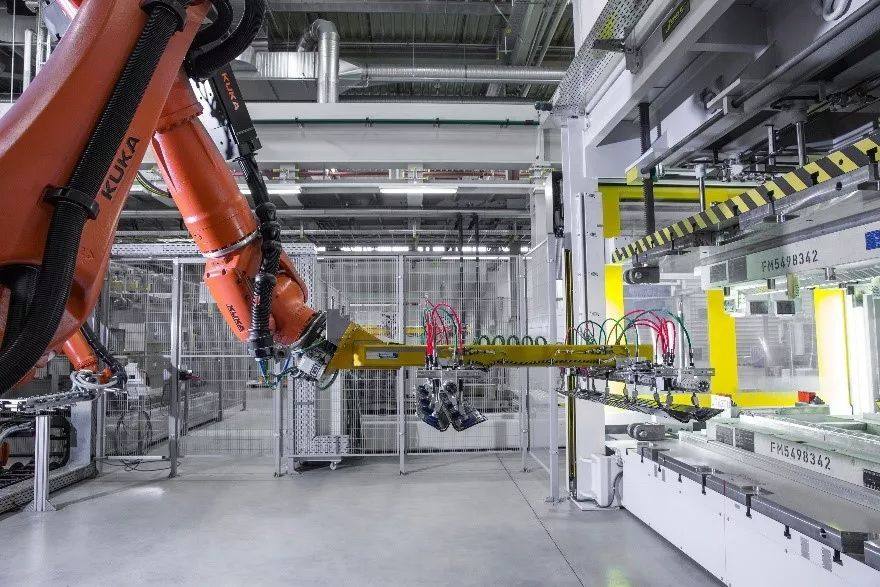
上图,湿法模压工艺被用来生产BMW7系的“Carbon Core(碳芯)”乘客舱组件,为造型复杂度较低的零件提供更短的生产周期和更低的成本。
参考资料:
https://www.compositesworld.com/blog/post/wet-compression-molding
文章来源于:黑话碳纤维
原文始发于微信公众号(艾邦复合材料网):复合材料HP-RTM和湿法模压成型工艺介绍