车载功率模块焊接工艺方案
车载IGBT模块封装厂面临的重点问题
一、以进口为主的功率模块封装设备真空焊接炉及整套方案交付周期长、建设周期长,无法满足客户订单需求,同时增加了企业的发展风险
二、进口真空焊接炉投产技术支持、服务及时性受到影响,新产线建设,专业技术人员不足,产量提升慢,配件更换周期长,延误生产
三、定制化需求,车载IGBT模块物料网数字化生产,可追溯的系统建设,物联网系统定制、硬件配置定制、出现很多定制化需求,无法快速响应满足
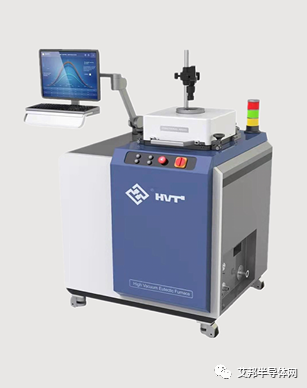
方案一
诚联恺达进口IGBT真空焊接炉替代方案
产品开发过程--标准机型、非标定制机型等
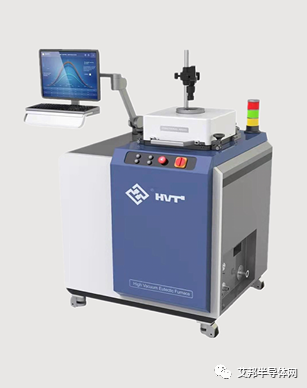
KD-V20 实验型
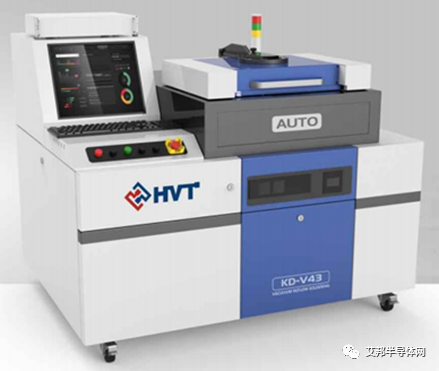
KD-V43 实验型
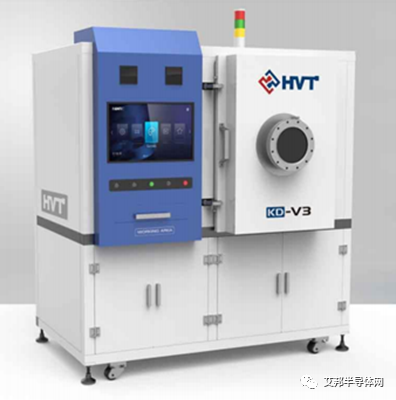
多层真空焊接炉 KD-V3V5
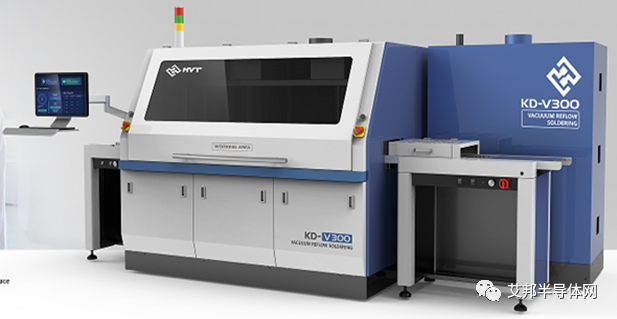
二极管、三极管、TO及光伏器件专用机型 KD-V10S
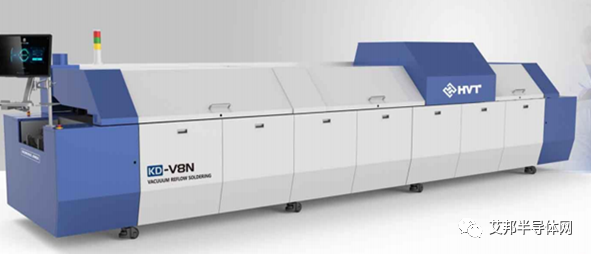
针对锡膏工艺的热风真空焊接炉 KD-V10N
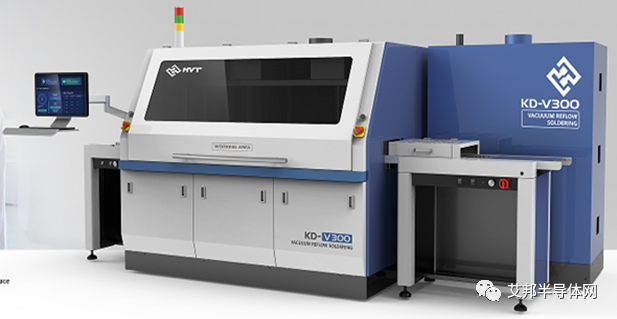
IGBT功率模块三舱真空焊接炉 KD-V300
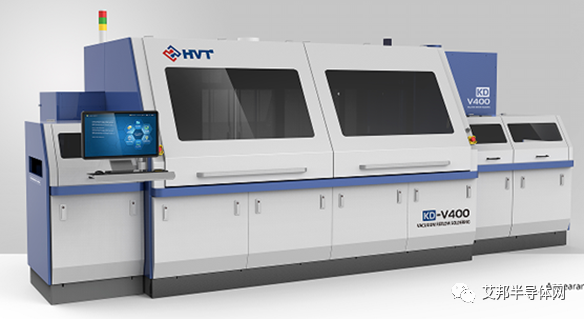
IGBT功率模块四舱真空焊接炉 KD-V400V400L
诚联恺达车载IGBT功率模块专用机型
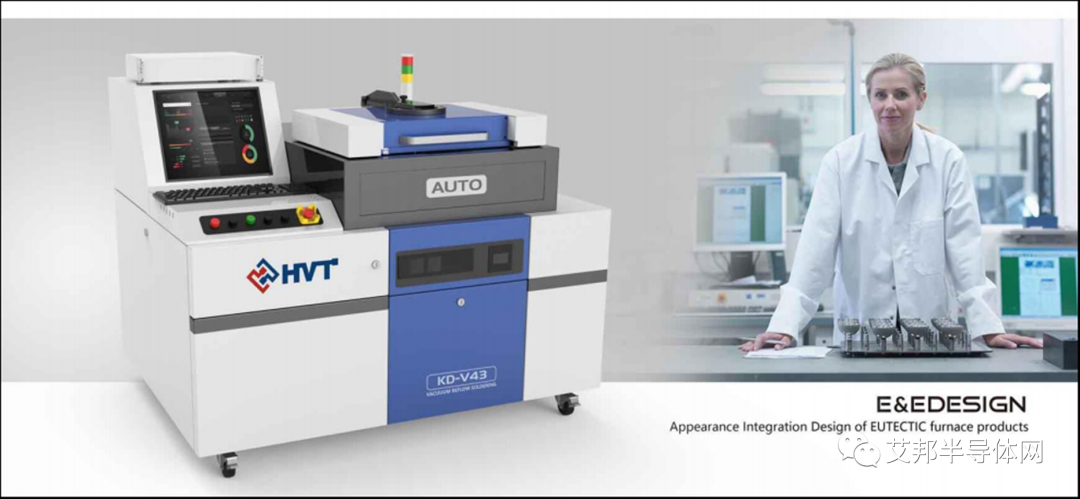
KD-V43 离线小型真空焊接炉 实验研发型
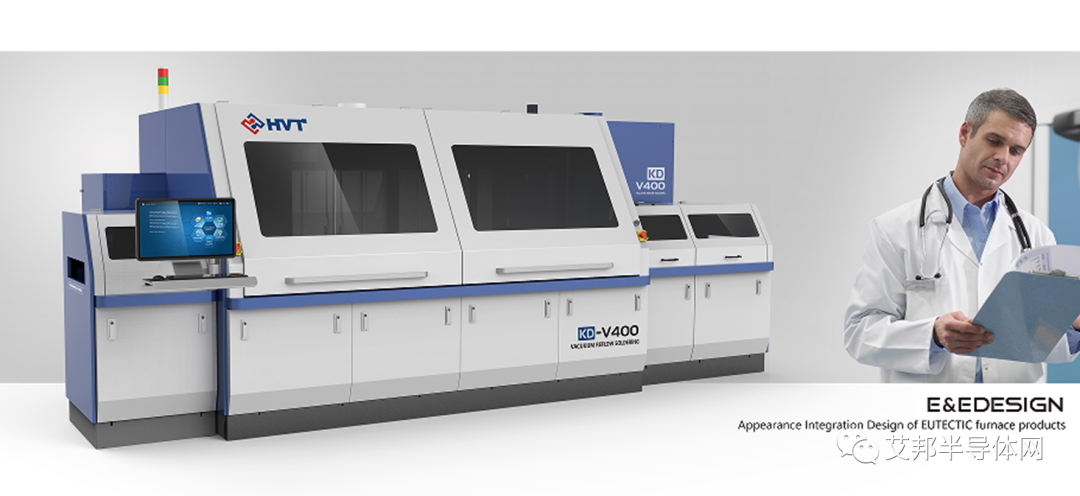
KD-V3V5 离线多层真空焊接炉 批量生产型
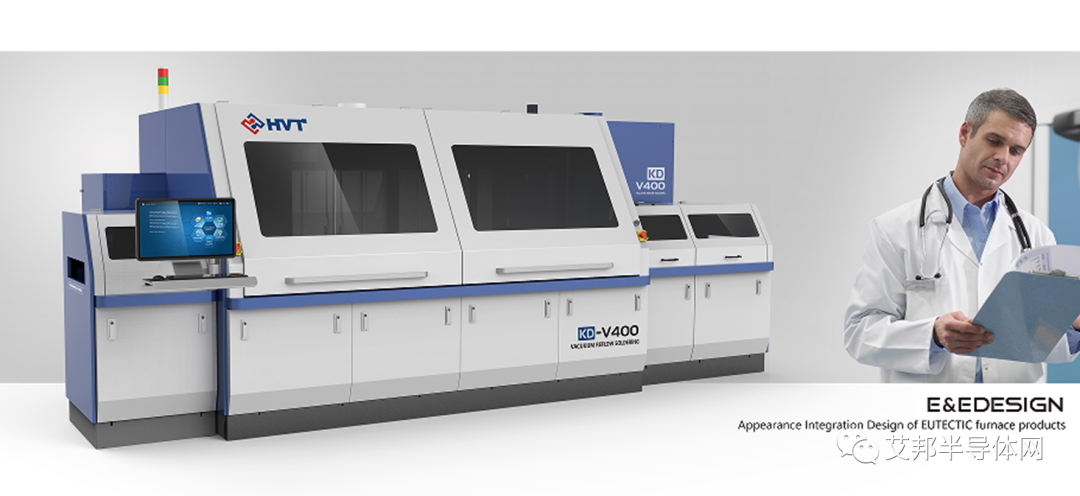
KD-V300 三舱在线自动化真空焊接炉 批量生产型
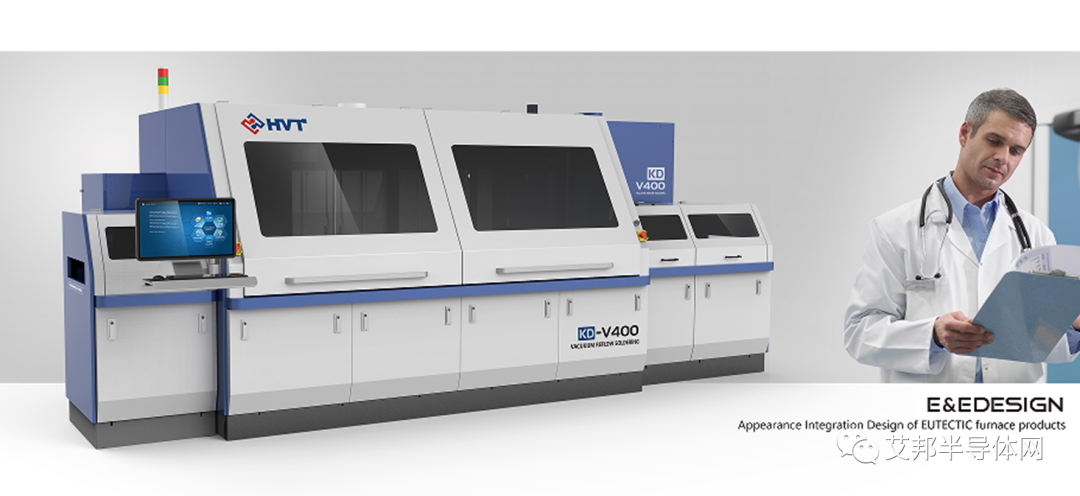
KD-V400V400L 四舱在线自动化真空焊接炉 批量生产型
进口真空焊接炉替代方案、交付能力
以上几款机型是诚联恺达重点推荐的进口设备替代方案,生产机型,出货量最多的是在线式三舱真空焊接炉KD-V300、四舱真空焊接炉KD-V400,已经交付100台以上,交付周期3-4个月,新工厂投产后,月产能可达30台以上。
满足甲酸焊片工艺及锡膏工艺,目前产品进入量产阶段,国内多家企业已经批量订购使用,性能稳定,各方面指标结果均满足生产需求,可以替代进口功率模块真空焊接炉。
方案二
车载IGBT功率模块的焊接工艺
方案
离线式真空焊接炉工艺方案
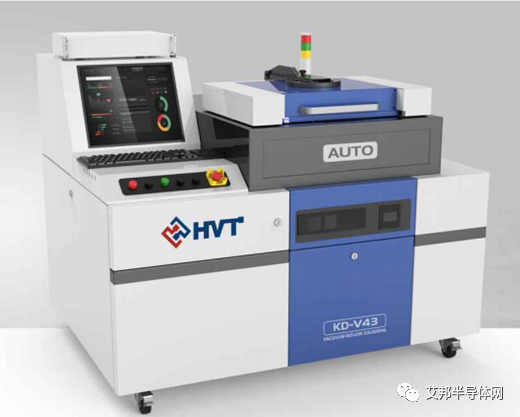
KD-V43 实验研发型焊接炉工艺方案--整体工艺时间20min/炉
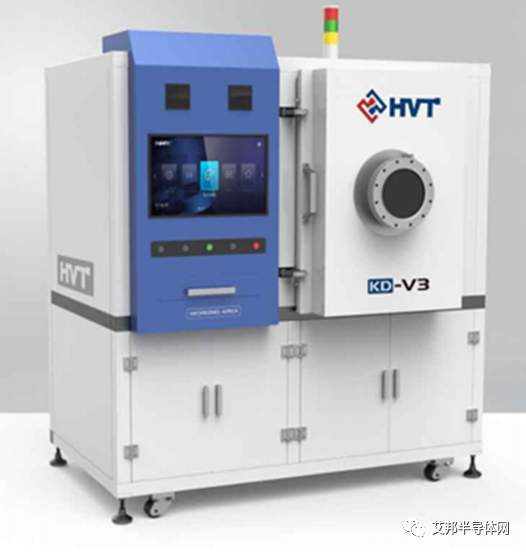
KD-V3V5 多层真空焊接炉工艺方案--整体工艺时间30min/炉
SAC305 工艺流程:
预热段 预热、甲酸还原
1、抽真空到设定真空度1mbar以下
2、充氮气,流量设置60-100L/min,至950mbar
3、升温加热至200℃
4、温度保持30s,同时抽真空至1mbar
5、充甲酸,流量设置30L/min,充至850mbar
6、在200 ℃甲酸环境下保持150s
焊接段 焊接抽真空排气泡
7、升温至焊接温度260 ℃
8、达到目标温度后,保持30s
9、抽真空至1mbar,到达真空度后,保持60s
10、充氮气到1000mbar,常压
冷却
11、设置目标温度45℃,冷却水温度23 ℃
12、达到目标温度后结束
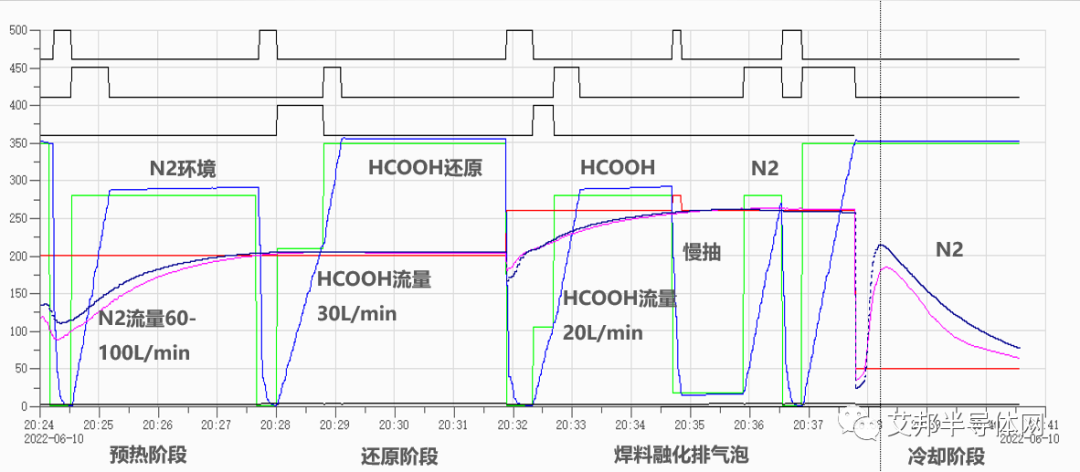
离线真空焊接炉工艺曲线
KD-V300 三舱真空焊接炉工艺方案
--连续工艺时间10min/托盘
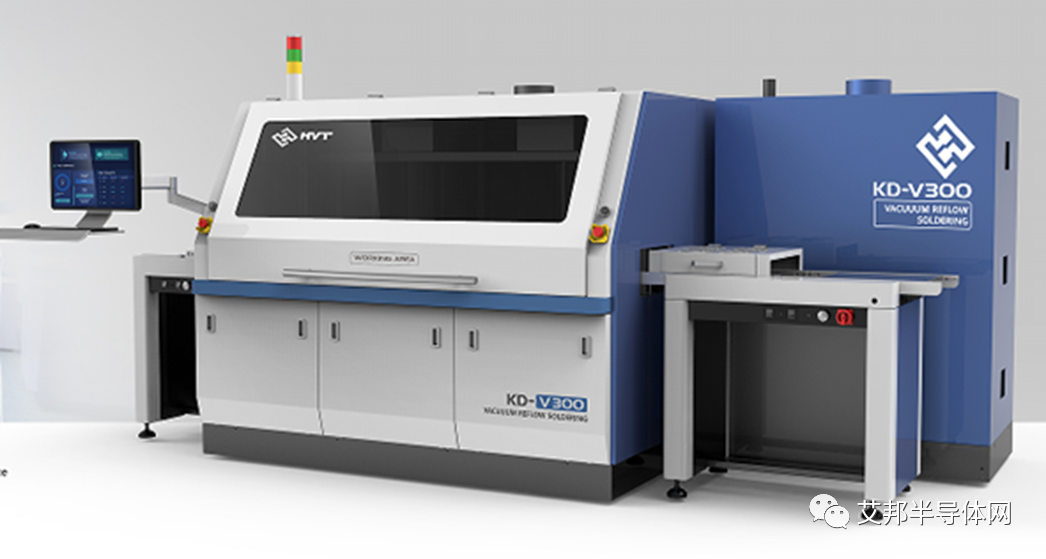
SAC305 工艺流程:
预热舱一 预热、甲酸还原
1、抽真空到设定真空度1mbar以下
2、充氮气950mbar
3、升温加热至200℃
4、温度保持30s,同时抽真空至1mbar
5、充甲酸,流量设置30L/min,充至850mbar
6、在200 ℃甲酸环境下保持120s
焊接舱二 抽真空排气泡
1、抽真空到设定真空度1mbar以下
2、充甲酸800mbar
3、升温至焊接温度260 ℃
4、达到目标温度后,保持30s
5、抽真空至1mbar,到达真空度后,保持60s
6、充氮气到1000mbar,常压
冷却舱三 冷却
1、设置目标温度45℃,冷却水温度23℃
2、达到目标温度后结束
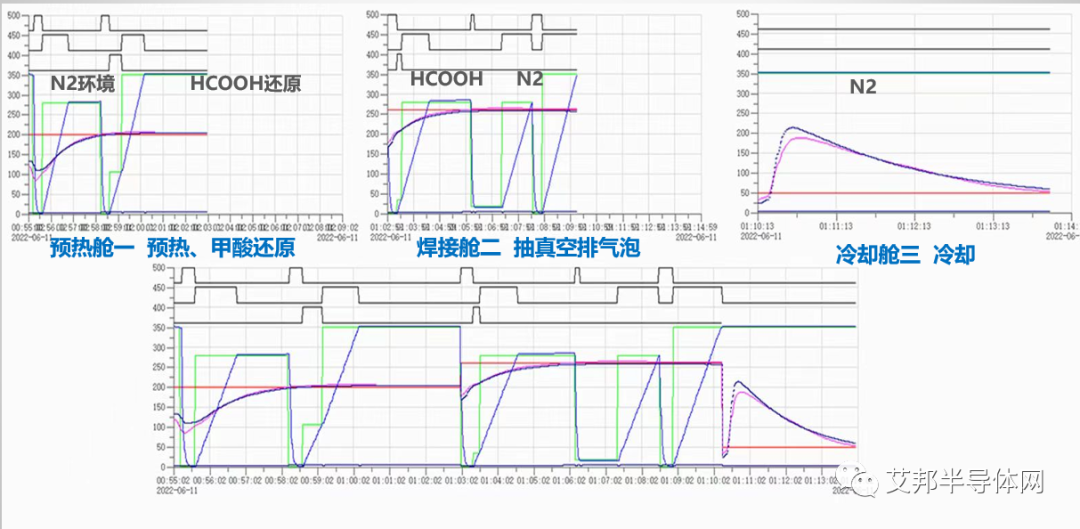
KD-V400 四舱真空焊接炉工艺方案
--连续工艺时间6min/托盘 产能提升50%
SAC305 工艺流程:产量相比V300产量
提升50%
预热舱一 预热
1、抽真空到设定真空度1mbar以下
2、充氮气950mbar
3、升温加热至160℃
4、进入预热舱二
预热舱二 甲酸还原
1、抽真空到设定真空度1mbar以下
2、充甲酸,流量设置30L/min,至950mbar
3、升温加热至200℃
4、温度保持30s,同时抽真空至1mbar
焊接舱三 抽真空排气泡
1、真空到设定真空度1mbar以下
2、升温至焊接温度260 ℃
2、达到目标温度后,保持30s
3、抽真空至1mbar,到达真空度后,保持60s
4、充氮气到1000mbar,常压
冷却舱四 冷却
1、设置目标温度45℃,冷却水温度23 ℃
2、达到目标温度后结束
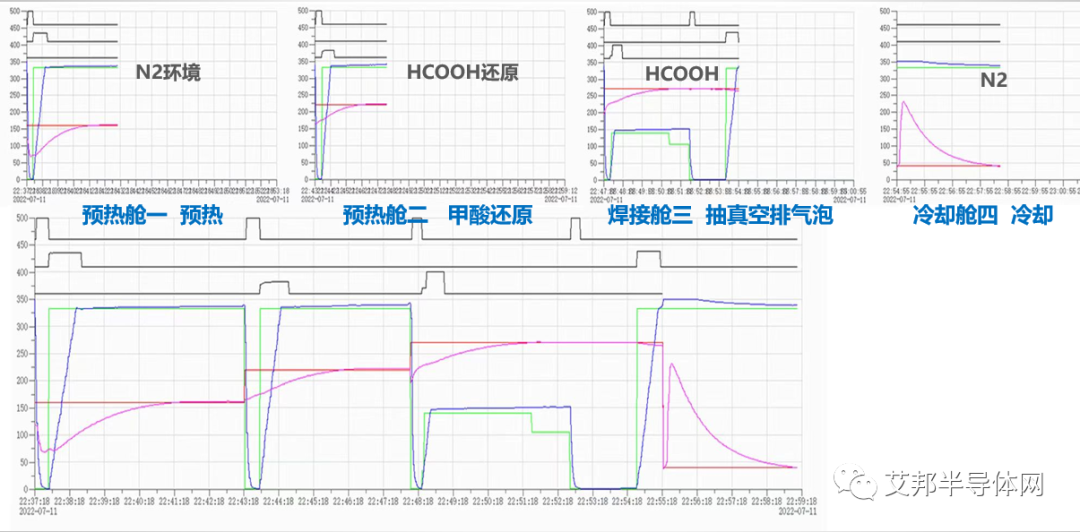
KD-V400L 四舱真空焊接炉工艺方案
--连续工艺时间6min/托盘 产能再次提升100%
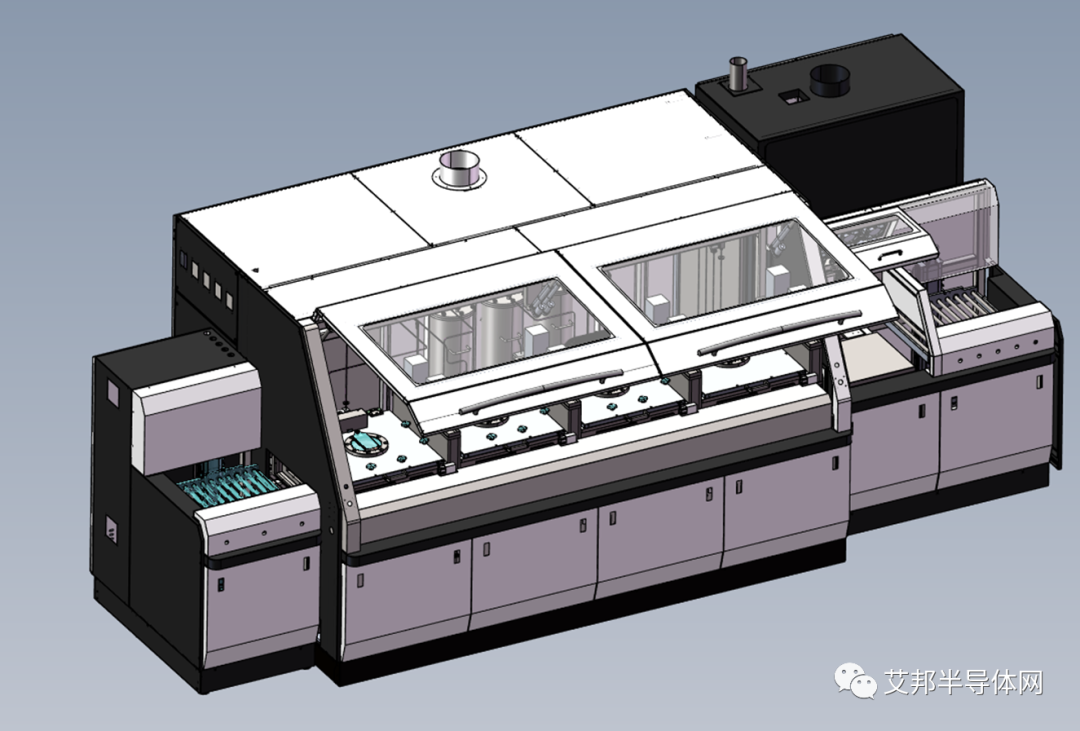
产品放置托盘有效区域面积加大,单套托盘放置产品数量增加100%
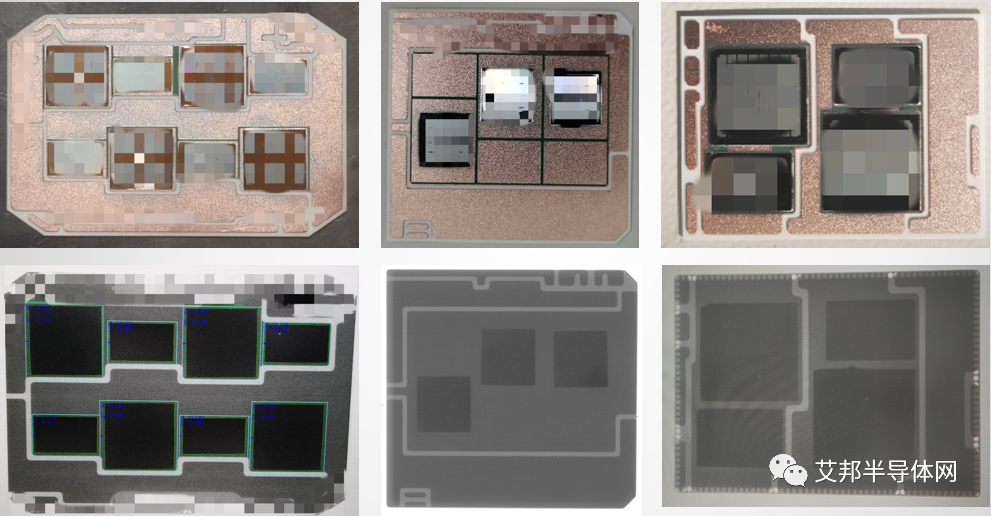
焊接目标效果:单个空洞率<1%,整体空洞率<2%
焊接空洞率<1%
原文始发于微信公众号(艾邦半导体网):车载IGBT功率模块焊接工艺方案