西典新能的主营业务为电连接产品的研发、设计、生产和销售,主要产品包括电池连接系统和复合母排。自设立以来,公司一直从事电连接技术的研究、开发和应用,产品广泛应用于新能源汽车、电化学储能、轨道交通、工业变频、新能源发电等领域。
7月20日西典新能已经通过上市会议,下一步将是提交注册及注册发行,从其招股说明书(上会稿)来给大家介绍一下该公司在CCS集成母排方面的发展历程,客户群体,生产工艺以及CCCS发展趋势等。
1、电池连接系统概述
电池连接系统是电池模组内电连接的结构件,装配于电池模组内部,具体应用示意图如下:
公司的电池连接系统/CCS 将铝巴、信号采集组件、绝缘材料通过热压合或铆接等方式组合在一起,实现电芯间串并联,同时采集温度、电压等信号,产品 具有结构轻薄、集成度高等优点,有利于提升电池包成组效率和空间利用率,具有较强的市场竞争力,符合行业轻量化、集成化以及大模组的发展趋势。
2、电池连接系统产品发展历程
2017 年,公司推出热压合方案电池连接系统,创造性地将复合母排热压合工艺应用于电池连接系统的生产制造过程中,产品具有结构轻薄、集成度高等优点,较传统注塑托盘方案有效缩减了产品体积、重量及配件数量,提升了电池模组的空间利用率与生产效率。
另外,电池连接系统产品的应用电压、电流均低于复合母排,公司将原有高电压、大电流领域的产品设计与制造经验应用于电池连接系统,较好满足了新能源电池对电池连接系统耐压及载流的需求。
自进入电池连接系统领域以来,公司持续对电池连接系统进行技术创新,保证产品能及时满足下游客户不断变化的需求,保持产品的创新性。公司通过对热压合工艺进行优化,形成了高效节能热控压合技术,自主设计了热压合工序的生产设备,能够有效降低单个产品压合工序的综合能耗与时耗、实现大尺寸产品压合,较好适应下游电池行业大模组、CTP/CTC 发展趋势引致的电池连接系统大尺寸化需求。
另外,公司将热压设备与自主设计的焊接设备、检测设备等进行系统集成,开发了电池连接系统自动化流水线,大幅提升生产效率与产品质量的稳定性。
公司电池连接系统产品发展历程如下:
公司 PCB 采样电池连接系统使用 PCB 组件替代线束作为信号采集组件,主要通过绝缘膜热压工艺固定连接,其中热压工艺使用绝缘膜经加热粘合固定铝巴及信号采集组件,有效减小产品体积。
2019 年,公司完成 FPC 采样电池连接系统产品及工艺设备开发,使用 FPC 组件作为信号采集组件,同时对热压设备、焊接及检测设备进行升级改造,可实现大尺寸产品的自动化生产,与 PCB 采样电池连接系统相比,有效增加了产品尺寸,且提高了生产效率。
2020 年,公司的 FPC 采样电池连接系统投入量产, 并向宁德时代批量供货,目前已广泛应用于新能源汽车及储能领域。
2022 年公司推出 FPC 吸塑盘电池连接系统,进一步丰富产品线布局。此外,公司积极开展 FFC 采样电池连接系统的研发工作,使用 FFC 作为信号采集组件,目前已在部分项目中实现量产。相较于 FPC 组件,FFC 具有成本低、强度高的优势,能够进一步降低产品成本并提高产品可靠性。
3、工艺流程及主要原料
电池连接系统工艺流程图
公司不同类别电池连接系统工艺及主要原材料对比如下:
4、近三年产能及产品营业额
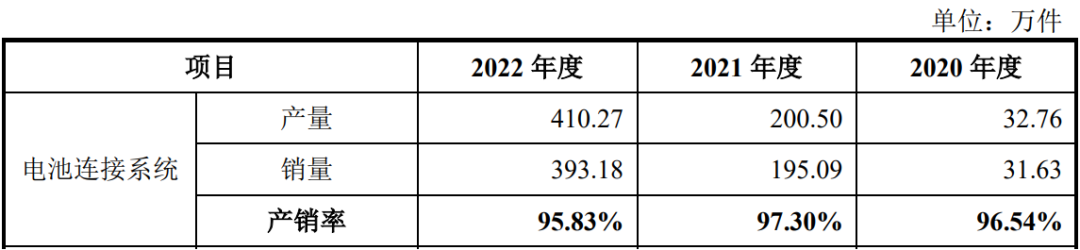

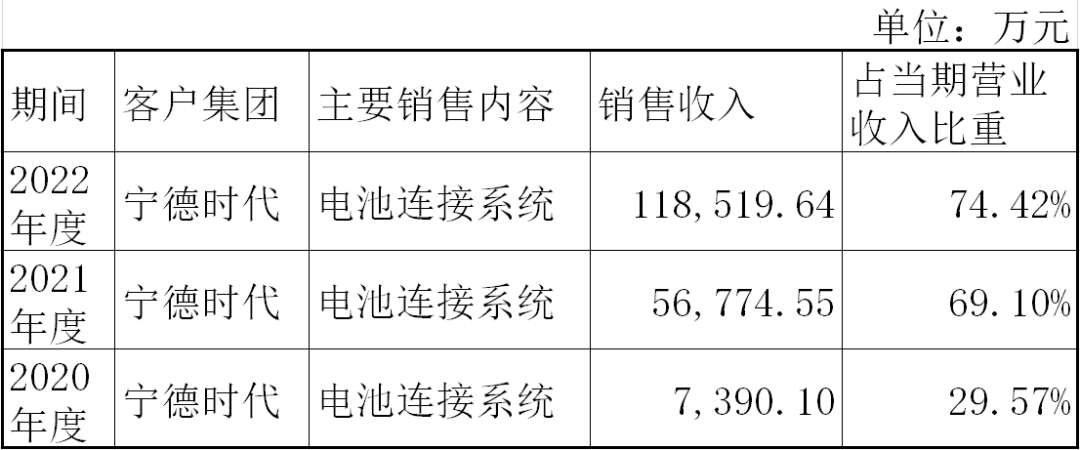
5. 主要客户
公司在电池连接系统业务发展初期,采取了优先保障宁德时代需求的大客户策略,导致现阶段电池连接系统主要面向宁德时代销售。随着公司电池连接系统产能扩充,未来在保持与宁德时代稳定合作的同时公司将积极开发其他电池连接系统客户,优化客户结构。
目前公司已与上汽集团旗下上汽时代动力电池系统有限公司、上汽大通汽车有限公司,蜂巢能源、比亚迪、中创新航等客户开展前期业务拓展。
6、电池连接系统发展态势
在动力电池及电化学储能领域,锂电池主要的技术进步来源于结构创新和材料创新,前者是在物理层面对“电芯—模组—电池包”进行结构优化,达到兼顾提高电池包体积比能量密度与降低成本的目的,后者是在化学层面对电池材料进行探索,达到兼顾提高单体电池性能与降低成本的目的。
锂离子电池传统的应用形式包括“电芯—模组—电池包”三层结构,电池模组在电池包箱体内排列,辅以管理系统和高压元器件,组成完整的电池包。
目前电池结构创新主要朝无模组化方向发展,减少零件数量降低成本,同时节约空间提高体积比能量密度。作为电芯之间串并联以及采集温度和电压等信号的连接传输组件,电池连接系统伴随电池结构创新不断迭代升级,主要体现在信号线路发展、集成工艺多样化以及 CTP/CTC 趋势下产品尺寸增加等方面。具体如下:
①.信号线路发展
早期锂离子电池主要采用铜线线束作为信号线路,常规线束由铜线外部包围塑料而成,连接电池包时每一根线束到达一个电极,当动力电池包电流信号较多时,则需要多根线束配合使用,对空间挤占较大。
在电池包装配环节由于线束较多、组装较为复杂,且需要依赖人工将端口固定到电池包上,导致装配自动化程度较低。
相较铜线线束,FPC 由于其高度集成、厚度较薄、柔软度较高等优点,在安全性、轻量化、布局规整等方面具备突出优势,装配时可通过机械手臂抓取直接放置电池包上、自动化程度高,适合规模化大批量生产。
2017 年前后,FPC 开始小批量应用于新能源汽车动力电池连接系统,随着 FPC 展现出的优异性能以及规模化生产后快速降本,FPC 替代传统线束的进程明显提速,目前 FPC 已经成为动力电池连接系统的主要选择。
FFC 为采用绝缘材料包裹多股铜丝绞合导体压合而成的扁平型电缆,相较 FPC 具有成本低廉、强度高的优点,但由于 FFC 作为信号采集线路使用时存在加工难度较高的问题,目前在电池连接系统中尚未规模应用。
未来,随着 FFC 在电池连接系统中应用技术的不断成熟,其有望凭借低成本、高强度的优势成为动力电池连接系统的主要选择之一。
②.集成工艺多样化发展
在公司推出绝缘膜热压 CCS 前,行业内主要采用注塑托盘的集成方案,通过热铆或卡扣固定托盘、信号线路及铜铝排。由于塑胶结构件较厚且重量相对较重,注塑托盘方案一定程度上影响电池成组效率与空间利用率。
绝缘膜热压 CCS 通过热压工艺将绝缘膜与信号线路、铝巴压合为一块薄片,与注塑托盘相比具有重量轻、空间利用率高、结构简单等优点,契合下游提升电池包成组效率和空间利用率的发展趋势,适合大尺寸产品应用。
近年来还出现了吸塑盘方案,采用较为轻薄的吸塑盘替代注塑托盘,也能有效降低重量、提高空间利用率。
③.动力电池 CTP/CTC 发展使得电池连接系统尺寸不断增加
动力电池厂商和车企在电池结构方面的研发创新始终围绕着成组效率和空间利用率提升开展,致力于达到提升能量密度、降低成本的目的。
过去几年,电池包结构创新主要体现在通过增加标准化电池模组尺寸、减少模组数量等,提升 电池包的空间利用率和系统能量密度,如从 355 模组向 590 模组、大尺寸模组演化。
由于模组的存在降低了动力电池包的空间利用率,影响成组效率,目前主流电池厂商已逐步采用 CTP 高效成组技术,跳过标准化模组环节,将电芯直接集成至电池包,突破传统“电芯—模组—电池包”三层结构。
根据宁德时代官方网站,以宁德时代 CTP 技术为例,通过简化模组结构,能够使电池包空间利用率提高 20%~30%,零部件数量减少 40%,生产效率提升 50%。
在 CTP 基础上,行业内部分电池厂家、车企已开始布局 CTC 技术,将电芯直接集成至汽车底盘,可省去模组、打包过程,实现更高程度集成化,进一步提升新能源汽车续航里程。
上述大模组或 CTP/CTC 发展趋势对电池连接系统设计、生产制造工艺水平均提出了更高的需求,电池连接系统尺寸需相应增加,同时进一步提升集成化水平,简化结构的同时提高空间利用率,以适应电池成组技术发展需求。
资料来源:招股书
//////////
原文始发于微信公众号(锂电产业通):从西典新能招股书(上会稿)看CCS生产工艺及发展趋势
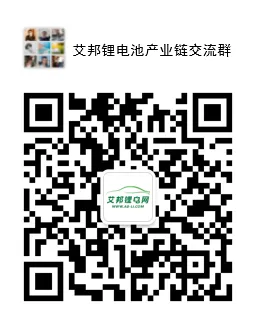