陶瓷材料具有高强度、高硬度、耐高温、耐氧化、耐腐蚀、化学性能稳定和轻质(低密度)等突出的优点,在航空航天、生物医疗、汽车、电子、能源、国防等诸多领域有着非常广泛的应用。然而传统的陶瓷成型技术面临加工困难(尤其是复杂几何形状结构成型更为困难)、制造周期长、生产成本高等不足和局限性,制约陶瓷零件更广泛的应用。近年来出现的陶瓷3D打印技术为该问题提供了一种全新的解决方案,陶瓷3D打印具有以下显著优势:(1) 无需原坯和模具,生产周期短,制造成本低;(2) 制造精度高;(3) 可实现几乎任意形状复杂结构成型,突破了传统工艺制造几何形状的约束;(4) 适合个性化定制和单件小批量生产;(5) 打印材料种类广泛,诸如氧化锆、氧化铝、磷酸三钙、碳化硅、碳硅化钛、陶瓷前驱体、陶瓷基复合材料等。此外,在微小零件3D打印、陶瓷/金属复合材料和功能梯度材料方面,以及材料-结构-功能一体化打印方面还具有独特的优势。目前国内外学术界和产业界已经开发的陶瓷3D打印工艺有十多种,主要包括:立体光固化成型(SLA)、数字光处理(DLP)或者面曝光成型、选择性激光烧结成型、黏结剂喷射成型、陶瓷熔化沉积成型(fused deposition of ceramics, FDC)、叠层实体制造、陶瓷墨水喷射打印成型、陶瓷浆料(挤出)直写成型等。
经过多年的发展,尽管陶瓷3D打印已经取得巨大的进展和突破,但是现有的各种陶瓷3D打印技术仍然面临以下挑战性难题:打印效率低;逐层打印致使成型零件存在各向异性,导致后续烧结过程中易于出现裂纹、变形等缺陷,严重影响打印件的质量、良率和精度。
针对传统陶瓷3D打印存在打印效率低和成型件具有各向异性的不足和局限性,青岛理工大学青岛市3D打印工程研究中心兰红波、张广明等人提出一种连续面曝光陶瓷3D打印新工艺,通过采用自主研发的复合富氧膜并结合配制的树脂基陶瓷浆料实现陶瓷素坯件的连续打印。
连续面曝光陶瓷3D打印新工艺,引入一种复合富氧膜并结合特殊配制的树脂基陶瓷浆料实现陶瓷素坯件的连续打印,整个打印系统主要包括的功能模块:数字光处理模块、储料槽、复合富氧膜、陶瓷浆料、成型零件、打印平台等。
图1 连续面曝光实验系统装置. (a) 连续面曝光实验系统装置; (b) 实验系统装置主要结构; (c) 控制模块; (d) 储料槽
其成型原理图2所示是利用陶瓷浆料中的丙烯酸光敏树脂的氧阻聚效应。由于氧阻聚效应,进入储料槽的氧气会抑制复合富氧膜顶部一定厚度内的陶瓷浆料的固化反应,从而形成几十微米的“死区”(dead zone)。同时,数字光处理模块发出的紫外光能固化“死区”上方的陶瓷浆料。由于已经固化的陶瓷部件与固定在储料槽底壁复合富氧膜的离型膜PDMS没有发生黏附,所以打印时无需缓慢剥离,从而能实现陶瓷零件的连续打印成型。
复合富氧膜是一种由多孔支撑层和富氧离型层组成的双层复合薄膜,多孔支撑层采用含有微孔的高透光PET膜,富氧离型层采用二甲基硅氧烷 (PDMS),复合富氧膜不但具有高度透氧和透紫外光的特性,而且具有优良的离型(低表面能)、抗拉伸、耐候性等物化性能。
图3 PET膜孔径大小对成型精度的影响. (a) 不同孔径下对打印精度影响的示意图; (b) 不同孔径下实际成型素坯件.对于相同厚度的离型层,多孔支撑层PET的平均孔径越大,其透氧量越高,进而导致“死区”厚度的增加,更多的陶瓷粉使得投影入射光线的散射现象更加严重,导致实际固化区域与理论固化区域的差值增大,降低了整体的打印精度.平均孔径为0.22 µm的 PET多孔膜更适合作为复合富氧膜的支撑层,可确保素坯件的整体打印精度.
连续面曝光陶瓷3D打印的工艺流程较为复杂,涉及的工艺步骤和工序较多,完整工艺流程如图4所示。
首先进行模型缺陷检查,然后加支撑和模型分层,最后将模型切片数据编辑成连续投影图像传输到数字光处理模块;
将表面改性后的陶瓷粉和预混液配制成陶瓷浆料(各组分确保均匀混合,避免陶瓷材料团聚、光敏树脂与陶瓷材料密度不同导致分层);
基本流程是Z向工作台带动成型平台浸入到陶瓷浆料中,使成型平台与成型窗口的复合膜保持设定距离(“死区”的厚度);Z向工作台以设定的打印速度(优化出的工艺参数)连续提升,同时数字光处理模块连续播放分层的数据信息,光源系统产生的紫外光投射到陶瓷浆料上,成型平台在Z向工作台的提拉下将已固化部分从浆料中拉起,陶瓷浆料持续填充已固化区域,整个过程连续无间断,直至整个模型打印完成;
从打印平台取下成型件,将素坯件进行清洗和烘干处理;
根据陶瓷浆料组分、固相含量的不同,采用优化出的脱脂烧结工艺路线和参数(烧结温度、时间曲线),首先脱脂,然后在烧结炉中进行烧结处理,完全去除陶瓷件中的有机成分,获得最终的陶瓷打印件。
其中模型数据处理和陶瓷浆料配置属于打印前处理模块,清洗、脱脂、烧结等属于打印后处理模块。
研究团队利用连续面曝光陶瓷3D打印技术,并结合优化工艺参数,打印了镂空陶瓷件、薄壁陶瓷件。
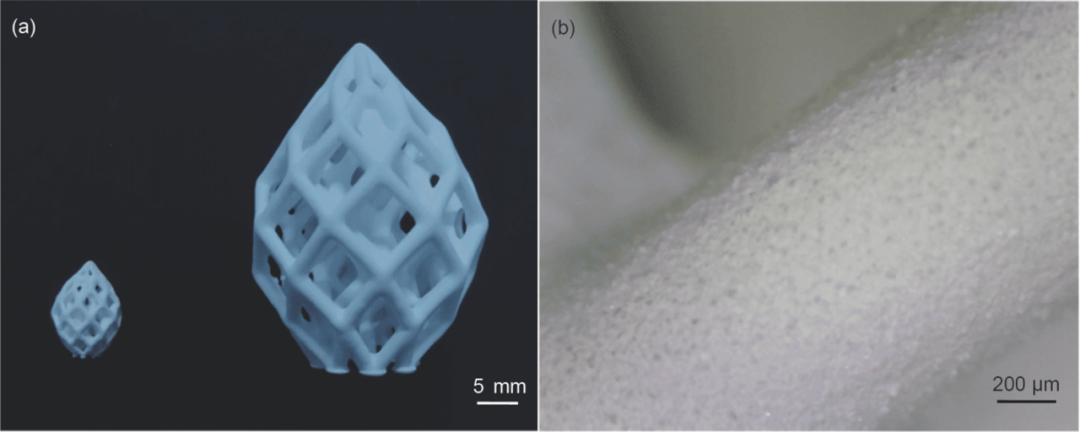
图5 基于连续面曝光陶瓷3D打印制造的镂空陶瓷零件(脱脂烧结后). (a) 两种不同镂空零件; (b) 镂空零件局部放大图
以树脂基氧化锆陶瓷浆料作为打印材料,氧化锆陶瓷浆料固相含量为50 vol%,其中陶瓷粉的平均粒径为5 µm。成型窗口复合富氧膜的支撑层采用平均孔径为0.22 µm 且厚度为10 µm的PET微孔膜,离型层为厚度为50 µm 的PDMS。打印速度设为80 mm/h。连续面曝光陶瓷3D打印制造的素坯件经过脱脂烧结后得到的陶瓷零件如图5(a)所示。实验打印结果显示:制件没有开裂和裂纹等缺陷,表面质量和尺寸精度高,体积收缩率约为 24%。通过显微放大图可以看出表面连续性较好,即未出现台阶现象,也未出现表面裂纹和较大孔隙。
图6 基于连续面曝光陶瓷3D打印制造的薄壁零件. (a) 简单薄壁结构的陶瓷件; (b) 小型叶轮的素坯件和陶瓷件
薄壁陶瓷件的制造是陶瓷3D打印的难点,成型窗口复合富氧膜参数与镂空陶瓷件案例相同,采用的氧化锆陶瓷浆料固相含量为40 vol%,打印速度设为100 mm/h。降低陶瓷浆料的固相含量有助于增加其流动性,提高填充速度。首先打印了一些结构较为简单的中空薄壁件,并进行了脱脂和烧结,如图6(a)所示,成型效果较好,未出现瑕疵。在此基础上又进行了结构较为复杂的小型叶轮的打印,打印的素坯件和脱脂烧结后得到对应陶瓷件,如图6(b)所示.实验结果显示:所制造的陶瓷零件表面质量好,没有出现开裂和裂纹等缺陷。
来源:王赫, 兰红波, 钱垒, 等. 连续面曝光陶瓷3D打印. 中国科学: 技术科学, 2019, 49: 681–689.doi: 10.1360/N092018-00338
原文始发于微信公众号(陶瓷科技视野):连续面曝光陶瓷 3D 打印新工艺