在环保和能源可持续发展的背景下,二氧化碳排放问题受到越来越多的关注。新能源汽车凭借其环保性和可持续性的明显优势,正逐步取代传统汽车,呈现出一种不可逆转的发展趋势。为了进一步推动这一进程,国家政府、各省市相继出台各项政策措施,加大对车规级功率器件行业的扶持力度,以加速其发展进程。
近年来半导体技术的发展促使车规级功率器件封装技术的发展和进步,在政策和技术的推动下,多种封装形式相继衍生。然而,相比工业应用,车规级功率器件的应用工况更为复杂,对其设计、制造和验证提出了更为严格的高功能安全标准。
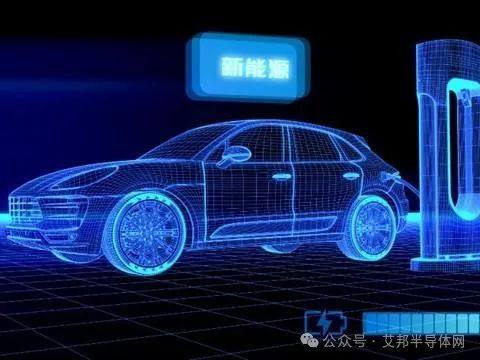
图源 摄图网
半导体技术的发展使得芯片的尺寸进一步缩小,给车规级功率器件的封装带来了巨大挑战,国内外厂商从结构、制程、技术、工艺、集成化、材 料等方面对车规级功率器件进行了全面提升,促使封装技术向着更高的功率密度、更紧凑的体积、更优化的驱动电路、更低的系统成本的方向发展。
器件的封装电感、芯片散热和电气绝缘等问题,以及器件内部的耦合效应,与器件的热学、电学、机械性能和可靠性密切相关,特别是车规级功率器件,其可靠性问题是封装关键技术研究的重点。因此,需要深入研究车规级功率器件的可靠性问题,才能探索适应市场发展需求的车规级功率器件封装结构。
在上述研究背景下,本文将紧密围绕车规级功率器件的封装关键技术和可靠性研究现状,从实际应用需求角度出发,深入剖析封装设计和可靠性问 题及其难点。首先,详细阐述车规级功率器件的应用场景及发展需求;其次,结合现有设计水平和主要厂商对车规级功率器件的封装关键技术进行归纳,并对可靠性研究难点进行总结;最后,归纳需要重点研究的问题,并在此基础上提出了相应现有可行的解决方案。今天我们先详细阐述一下车规级功率器件的应用场景及发展需求,后面的内容将陆续放出
一、车规级功率器件封装现状及需求
封装现状
车规级功率器件的封装方案可分为以下两类:多分立器件并联式方案和功率模块式方案,图 1 为两种封装方案的基本结构。图1(a)为多分立器件并联式方案的基本结构,功率芯片焊接在以铜基底为支撑面的底座上,通过内部的连接线引出芯片的电极,管脚直插式焊接。分立器件大多基于标准封装,工艺成熟,成本低,采购周期短,提高了开发设计的适应性和适配性。
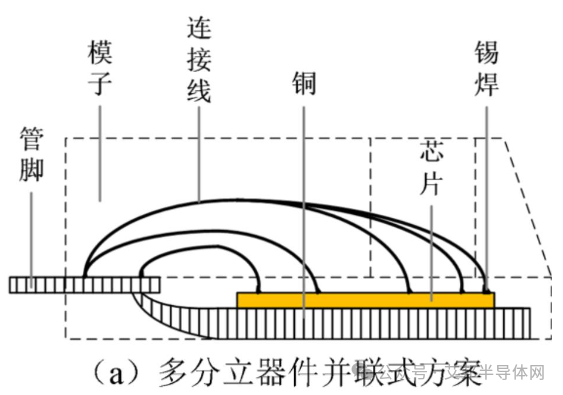
图 1 车规级功率器件的封装方案
图1(b)为功率模块式方案的基本结构,隔离构造,芯片之间通过焊锡与键 合线相连,铜箔附着在陶瓷基板的上下两面,上层铜箔与芯片及端子连接,下层铜箔与散热基板连接。可以容纳多个功率芯片串并联,可应用于更高功率的场合,通过提高内部设计达到更高的可靠性和鲁棒性。
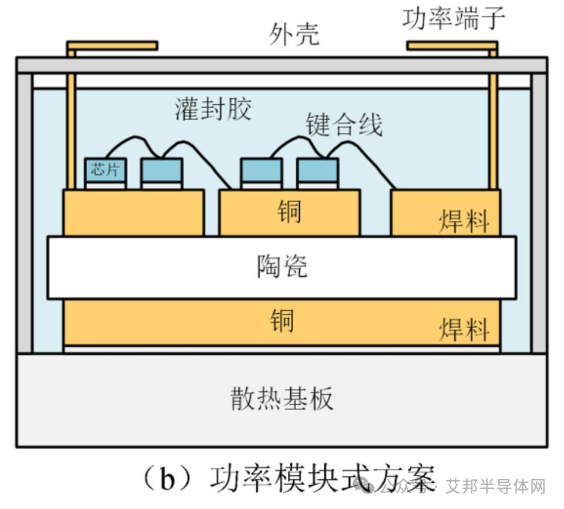
图 1 车规级功率器件的封装方案
功率模块式方案凭借其高功率密度的封装优势又衍生出各具特色的封装方式,典型代表有 HybridPACK 封装、EasyPACK 封装、功率集成模块(PIM)封装和双面散热(DSC)封装,如图2 所示。HybridPACK 封装具有高集成度、体积小、质量轻的特点;EasyPACK 封装的特点是简化集成,降低电感,即插即用;PIM 封装将多电路集成到单个模块中,高效、可靠、紧凑;DSC 封装则实现了双面散热且空间利用率高,热性能和可靠性好。
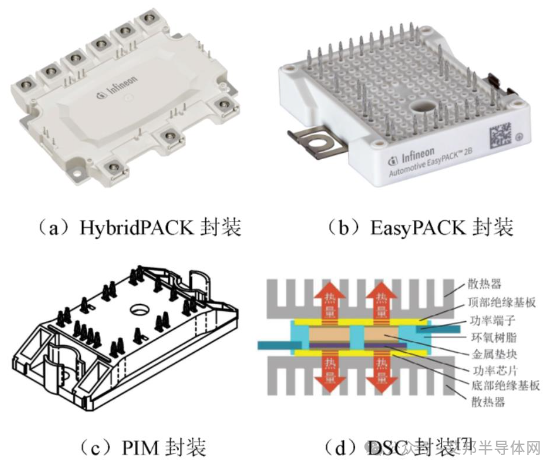
图2 功率模块式方案封装典型代表
2)主要应用场景
与燃油汽车相比,新能源汽车功率半导体器件的用量明显增长,广泛应用于车载充电机(OBC)、功率控制单元(PCU)等部件中。OBC 是实现电网经 AC/DC 转换器为电池组充电的关键部件。与 PCU 相比 OBC 的功率等级较低,功率器件产品往往具有体积小、质量轻、功率密度高的优势,一般采用分立式封装和 EasyPACK 封装。以功率器件制造厂商德国 Infineon 公司为例,针对 OBC 用功率器件的封装设计,Infineon 公司开始采用 TO247-3 和 TO247-4 封装的 SiC 功率器件,而后是 TO263-7 贴片封装的 SiC 功率器件,近几年则推出了 QDPAK TSC 顶部散热封装技术,如图 3 所示。
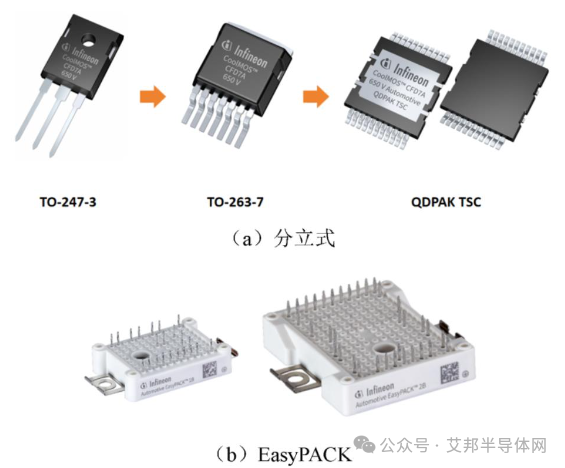
图 3 OBC 用功率器件封装技术发展主要历程
PCU 是实现电池组经 DC/AC 转换器驱动电机的关键部件,功率等级相对较高,因此对其功率器件的功率密度和可靠性提出了更高要求。以 Infineon 公司为例,其车规级功率器件产品早期采用 Si 基 IGBT 的平面型、波浪型 HybridPack Drive(HPD)封装,而后采用针翅(Pin-Fin)型 HPD 封装,再进一步将 Al2O3 基板更换为 AlN 基板并将电流提高到 950 A,之后提出用双面散热塑封 DSC 模块降低热阻提高功率密度。但考虑到双面塑封 DSC 模块封装应力会导致芯片栅极失效,为了消除此影响,现有封装形式多采用单面直冷塑封模块,封装内部采用铜带键合和纳米银烧结技术,如图 4 所示。
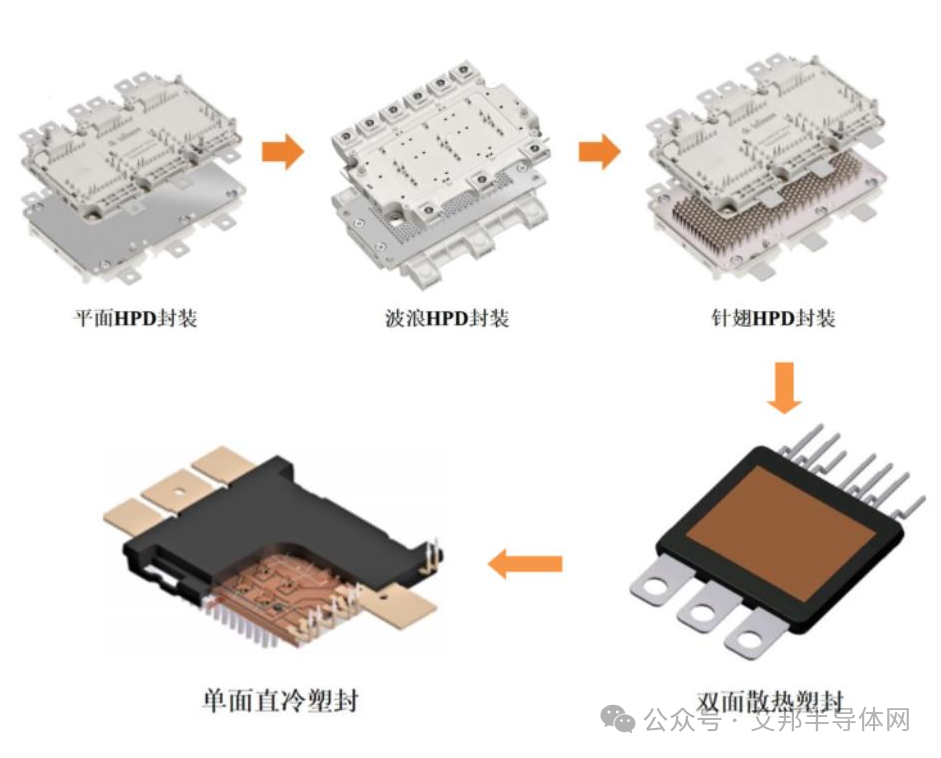
图 4 PCU 用功率器件封装技术发展主要历程
2. 发展方向及需求
针对车规级功率器件的封装设计,很多学者和器件厂商进行了研究,本文将围绕以下几个重难点,对已有封装设计发展方向进行总结,并参考已有模块设计给出相应的发展需求。
1)高功率密度和高工作效率
车规级功率器件影响着整车的充电效率和行驶工况,要具备尽可能高的功率密度和工作效率。若应用第三代宽禁带半导体材料的 SiC MOSFET 和 GaN HEMT等半导体器件,能使电动汽车的能耗在降低的同时,获得更好的性能和里程表现,并且可以大大缩短能源补给时间。
目前特斯拉、比亚迪、蔚来均已有车型采用了全 SiC 模块主逆变器,且已有几十家车企在 OBC 上采用了 SiC 技术;晶体管外形(TO)封装的多分立器件并联式方案,通过先进的均流技术可以在性能不变的情况下降低单个器件的电流负担,降低温度并提高效率。
Infineon 公司的无引线封装有助于减少导通电阻(Rds,on)和提高载流能力;ABB 基于堆叠陶瓷基板结构的大电流 SiC 功率模块的 3D 结构,可以更加灵活地控制各电位信号并将多个半导体并联工作,实现模块的快速开、关切换。
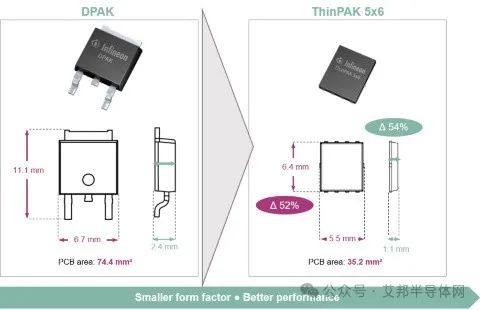
Infineon无引线 SMD 封装
2)强散热能力和低热阻
大功率混合动力汽车(HEV)/电动汽车(EV)的使用对电驱动系统的热管理提出了更高要求,要兼具承受较高局部电流和损耗密度的能力,需要提升散热能力、降低热阻。
对称设计的双面散热结构可以将模块的散热效率提高一倍,等效芯片的结-壳热阻(Rth,j-c)降低了约 50%,从而大大降低了结温(Tj),提高了热性能和可靠性;集成针翅基板的直接液体冷却(DLC)模块消除了导热硅脂的负面影响,具有优越的热性能;无基板结构、无衬板结构,如直接芯片键合到母排、衬板直接液体冷却、衬板基板一体化设计、集成液体循环冷却通道等,其设计目标是通过简化模块结构,减少结合层,去除热界面材料(TIM),实现降低热阻抗,降低 Tj,增加热稳定性和可靠性。
Infineon 采用了 Pin-Fin 和 DSC 相结合的散热结构以增强模块散热能力;Infineon 采用的扩散焊互连技术可以降低 Rth,j-c;Y.Y.Chen 等人提出了基板集成相变散热结构的 IGBT 器件,提高了温度均匀性,有助于器件散热;ABB 的印制电路板(PCB)嵌入式封装可以增强器件的散热能力并降低热阻;Semikron 的 SKiM 技术将芯片通过银烧结与绝缘衬板相结合,克服了无基板结构衬板底部和散热器间导热硅脂材料对模块热性能和可靠性的影响;Semikron 的芯片直接压接技术可以降低封装热阻;ST 的 SLLIMM HP 系列智能功率模块采用直接覆铜(DBC)HPS(Al2O3,质量分数为 9%的 ZrO2)基板以提高其散热能力,其推出的 ACEPACKTM SMIT 功率器件封装顶部绝缘散热采用 DBC 贴片技术,实现了高效的封装顶部冷却。
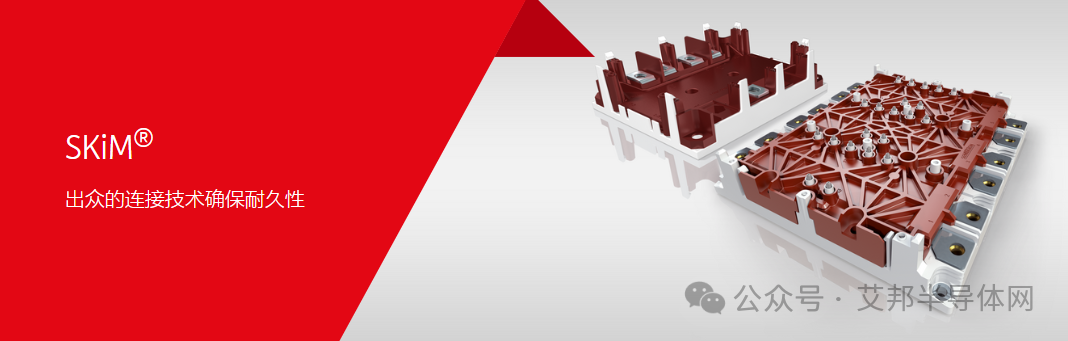
赛米控丹佛斯 SKiM 技术
3)低寄生参数
寄生参数包括回路总电感、分布电感和电阻,寄生参数会影响功率器件的开关损耗,功率器件的开关瞬变还会带来一系列器件和封装内部电磁寄生效应问题。
Infineon 在 HybridPACK 模块中采用了高水平电流对称性设计,可以降低杂散电感;Infineon 的 EasyPACK 功率模块通过采用并行化带状线设计,也达到了降低模块杂散电感的目的;一些改进型引线键合结构通过减小换流回路长度、优化功率端子、改进芯片布局方式等思路降低回路寄生电感。
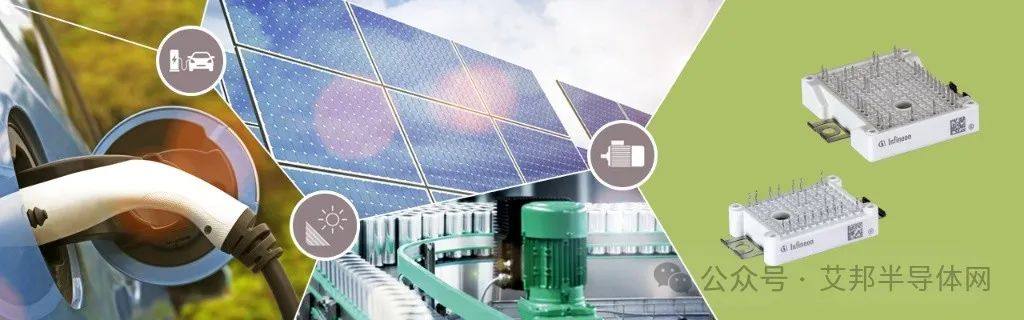
英飞凌 EasyPACK 系列产品
4)高绝缘能力
功率芯片在使用过程中要避免与外界接触,否则芯片电路将受到空气中的污染或杂质颗粒的腐蚀或影响,导致功率器件电气性能降低甚至使电路失效。在 SiC 功率器件内部高电场强度下,电化学腐蚀过程将尤为严重,需要通过采用高强度的顶部封装材料等措施,应对由 SiC 功率器件强内外磁场所带来的高绝缘需求。
采用灌封胶进行封装可以提升器件在高温和高压下的电气绝缘能力;绝缘材料在过高的温度下也可能发生老化和性能的下降,合理设计散热结构对提升功率器件的绝缘能力也十分重要;采用塑封功率集成模块可以提高器件的可靠性、抗震性和防尘防水性能;TOSHIBA 的塑封模块式栅极注入增强型晶体管(IEGT)器件为了获得更好的绝缘性而采用了高相对漏电起痕指数(CTI)的材料。
东芝塑料模块式 IEGT 器件 PMI
5)高集成度
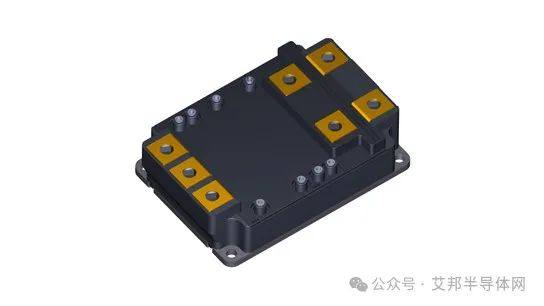
TOSHIBA 碳化硅功率模块的新封装 iXPLV
除上述外,还有低成本、采购周期短、耐久性好、便于使用和优化升级等发展需求。对于车规级功率器件的封装设计来说,满足不同应用场景、适应高标准的发展需求、从不同角度综合考虑、达到多维度优化的最佳效果,依然是一个值得研究的复杂问题,后续内容请持续关注。
参考资料:车规级功率器件的封装关键技术及封装可靠性研究进展,武晓彤等.
原文始发于微信公众号(艾邦半导体网):车规级功率器件的封装关键技术(上)