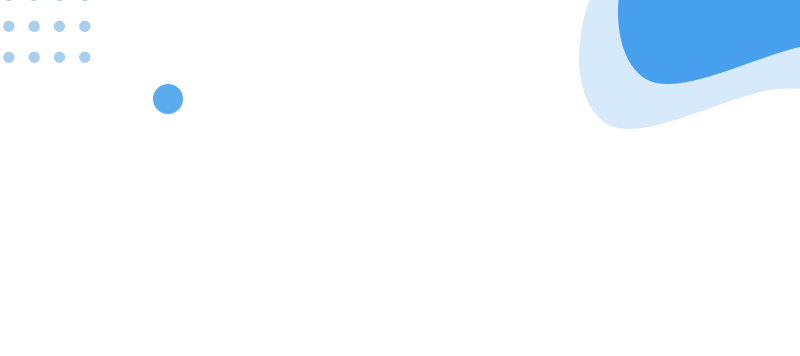
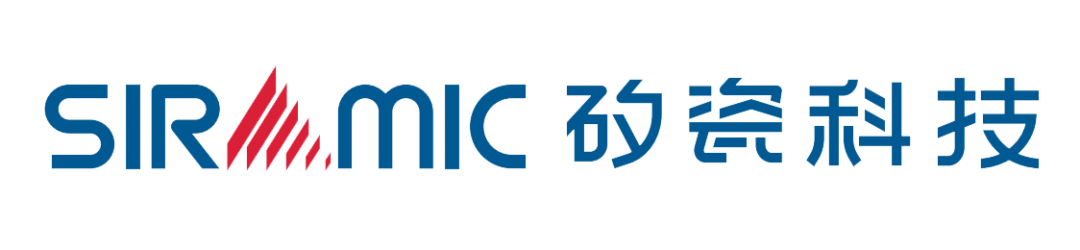
LTCC(低温共烧陶瓷)技术中,打孔工艺的重要性不言而喻,它是实现多层LTCC组件垂直互连和功能集成的关键步骤。
LTCC技术的一个显著特点是能够在多层结构中实现复杂的电路布局,打孔工艺使得不同电路层之间能够通过导通孔实现电气连接,这是构建三维电路结构的基础,而通过精确的打孔和导电填充,可以在有限的空间内实现更高的组件集成度,这对于缩小电子设备尺寸、提高性能和可靠性至关重要。打孔工艺的质量直接影响到LTCC组件的电气性能,如信号传输的完整性、阻抗匹配和射频性能。高质量的打孔可以减少信号损失和反射,提高信号传输质量。
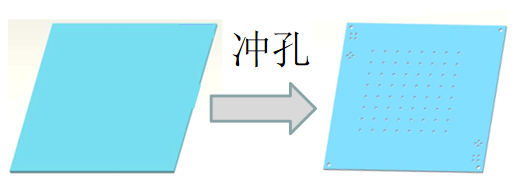
打孔原理
按照打孔方式可分为机械打孔和激光打孔。
机械打孔的原理如图,加工时,线性马达控制的机械手带动生瓷片移动,当生瓷片移动到规定位置后,通过冲针与冲模上通孔的咬合,在生瓷片上形成需要的通孔。冲掉的生瓷碎屑由真空吸附到废料盒内,以避免碎屑残存在生瓷的通孔内,对填孔质量造成影响。
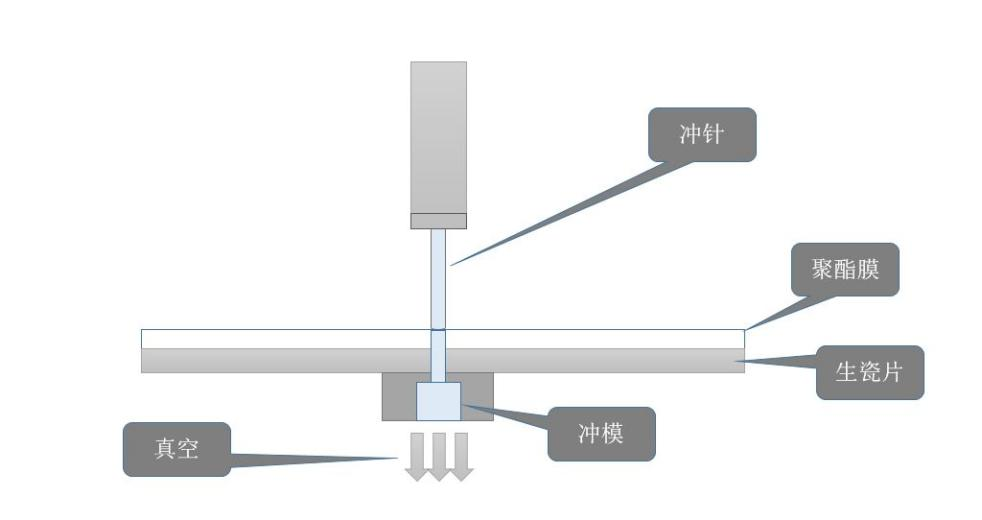
机械打孔原理
激光打孔的原理如图,加工过程中,激光器位置是固定的,载片台将生瓷移动到某一区域后,通过振镜的摆动,使激光束移动到加工位置,完成该区域的生瓷打孔。激光打孔时激光焦点位置位于生瓷表面,使其达到熔融状态,进而熔化挥发形成热刻蚀,激光束在计算机的控制下做圆周或特定路线的运动,从而使刻蚀部分重叠,进而形成通孔,划切下产生的微粒由真空吸附到废料盒内。
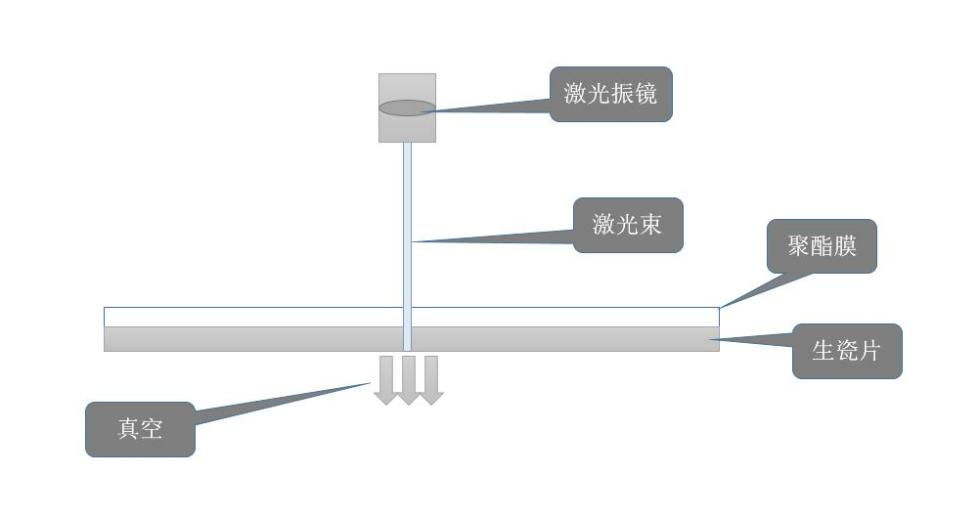
激光打孔原理
不同打孔方式的优缺点
机械打孔
机械打孔具有加工质量好、孔径准确、孔位精度高的优点,机械加工的方式使其对生瓷片影响最小,冲制的通孔上下一致,为标准圆柱形,孔型圆度好。机械打孔的缺点主要是孔径受制于使用的冲针尺寸,无法加工极小尺寸(100μm以下),在进行非标准尺寸或异形孔的加工时会受到限制,另外,机械打孔需消耗冲针,耗材昂贵。目前先进机械打孔设备生产效率可达单针1800孔/分钟以上,打孔位置精度可达±5μm。若定制模组进行冲孔,效率可更高,但对模组加工质量要求也较高。
激光打孔
激光打孔具有不使用耗材、加工速度快的特点,并且激光打孔不受孔径限制,在非标尺寸和异形孔加工时具有极大优势。激光加工的缺点主要是激光加工时会对加工区域产生热影响,导致生瓷片通孔边缘状态发生变化。另外,由于激光束的特性和加工方式,激光的入口直径更大、出口直径更小,产生锥度。激光加工的效率受生瓷片厚度和孔径尺寸影响,生瓷片厚度越大,孔径尺寸越大,加工效率越低。目前先进的激光打孔设备在特定条件下单激光头生产效率可达4000孔/秒,而不少厂家为提升加工效率还设计双头双工位甚至四头四工位设备,其加工效率更是倍增。
如何提高打孔质量
提高打孔的质量通常涉及对设备、材料、工艺参数和操作流程的精细控制。
就机械打孔来说
①选择合适的设备:使用高精度、高稳定性的打孔机是前提,确保设备的X、Y运动平台能够实现生瓷片的高速、高精度移动;高质量的冲针和凹模是保证打孔质量的最重要因素,冲针和凹模的硬度、圆度、尺寸精度、装配公差直接影响着机械打孔的质量。
②适宜的材料:机械打孔过程仅发生物理变化,因此对材料成分几乎没有要求,一般的LTCC材料都可采用机械打孔的方式,但材料的机械特性会对打孔质量造成较大影响。若生瓷片的脆性较大,在打孔时易发生崩缺、开裂;若生瓷片的材质不均匀,会影响打孔的一致性;若生瓷片的平整度不够,会影响加工通孔的位置准确度甚至造成生成瓷片损坏。在生瓷片脆性合适的情况下确保其平整度和一致性是保证机械打孔质量的重要条件。
③优化工艺参数:机械打孔的主要参数是间距、压力和速度。间距是指生瓷片在冲针和凹模之间的间距,一般情况下三者相距越近,冲针加工的孔径越精准,孔型越圆,加工速度越快,但过近的间距对生瓷片的平整度和相关机构的加工要求就越高,间距越近,越易发生冲针损坏或生瓷片破损。压力主要影响通孔的完整性,合适的压力范围应保证通孔能完整打穿而不对其他机构产生影响。速度主要指冲针加工的时间,一般将整个过程分为冲针等待时间(从生瓷片移动完成到冲孔开始)、冲孔时间(从冲针下行到冲针开始上行)、冲针复位时间(从冲针开始上行到冲针上行完成回到原位),合理调整这三个过程的时间才能保证机械打孔过程的稳定高速运行。
④操作流程的精细控制:如保证生产环境的清洁和稳定,避免微尘和湿度对打孔质量的影响,控制生瓷片的转运过程,减少转运过程中对生瓷片平整度的扰动等都是提升机械打孔质量的重要保证。
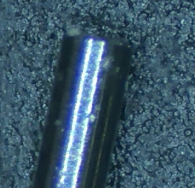
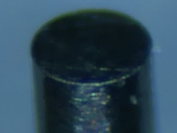

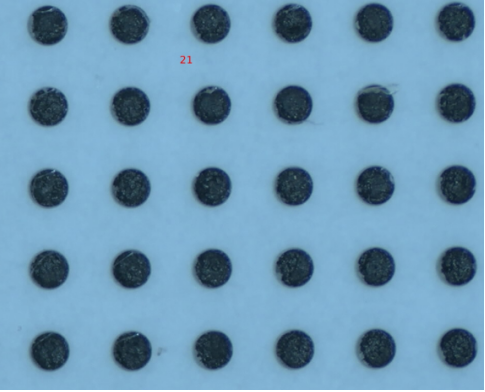
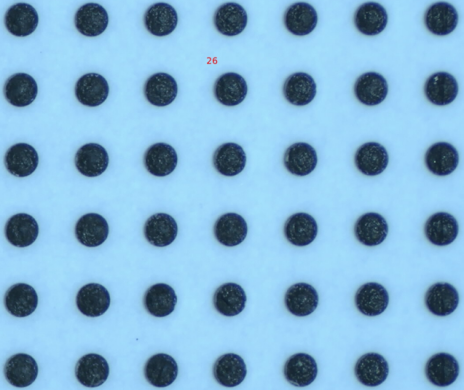
完好的冲针及凹模及其打孔效果
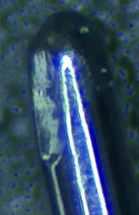
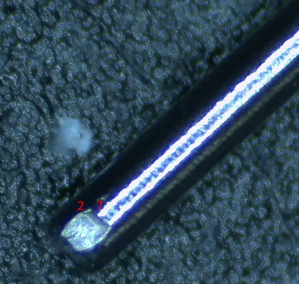
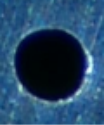

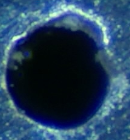
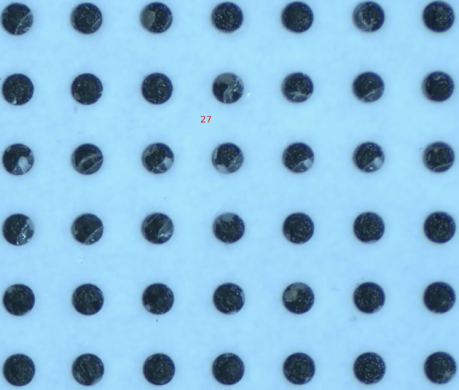
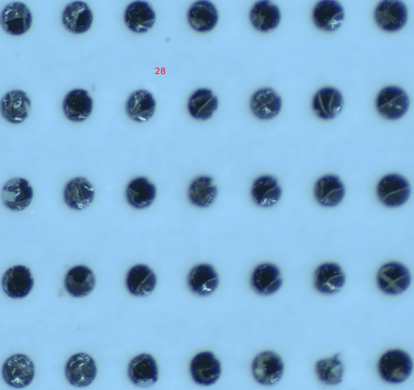
磨损的冲针及凹模及其打孔效果
就激光打孔来说
①选择合适的设备:使用具有稳定的激光器、精确的导向系统和可靠的控制系统的高性能的激光设备,这是提高激光打孔质量的基础。当前激光打孔的方式有两种,其一是将CO2激光的光斑精确聚焦于固定尺寸,采取冲制的方式直接加工通孔,这种加工方式速度快,加工效率高,但其热效应高,对材料要求高。其二是使用皮秒、飞秒等脉冲激光聚焦于较小尺寸(一般为30μm以下),采取划切的方式加工通孔,这种加工方式加工效率低,但热效应更集中,对材料的损伤更小。
②优化工艺参数:激光打孔的主要参数是激光聚焦位置、激光功率、脉冲宽度、激光频率和振镜标刻速度。激光在聚焦位置才能形成最小的光斑,进而提升打孔的精度和锥度,因此在激光划切加工时,往往需要聚焦位置随着加工遍数变化。激光功率是影响打孔速度和质量的关键因素,功率越高,去除材料的速度越快,但过高的功率可能导致材料过度熔化或热影响区域扩大。脉冲宽度影响激光能量的分布,较短的脉冲可以提供高峰值功率,更适合高精度打孔,较长的脉冲则提供更平缓的能量分布,适用于较深的打孔;激光频率决定了单位时间内激光脉冲的数量,增加频率可以提高打孔速度,但过高的频率可能导致热量积累和材料损伤;振镜标刻速度影响着激光聚焦光斑移动的速度,其与激光频率配合才能保证孔型的完整性与圆度。
③操作流程的精细控制:如保证生产环境的清洁和稳定,避免微尘和湿度对打孔质量的影响,针对生瓷片和PET采取不同的打孔参数组合打孔,提高打孔质量等。
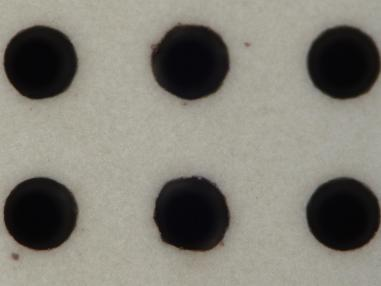
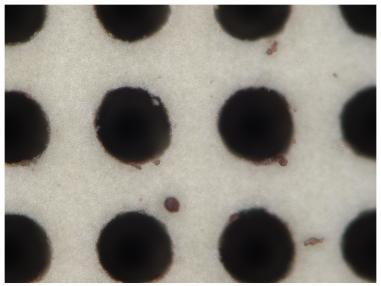
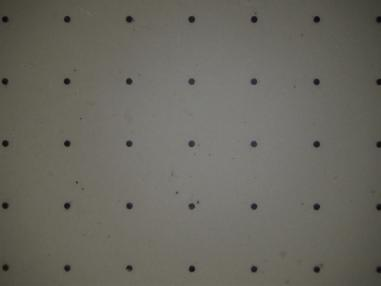
不良的激光打孔质量
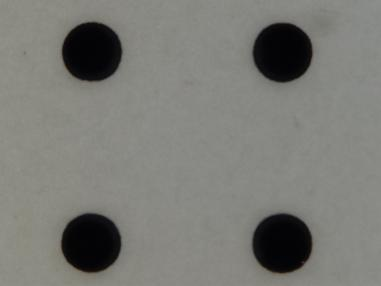
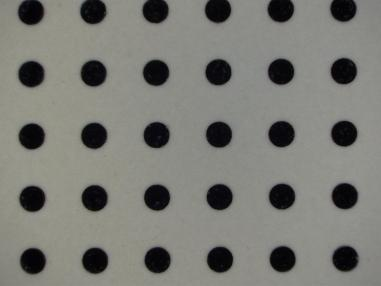
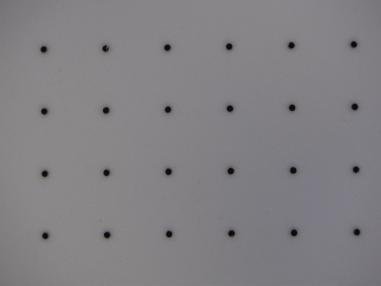
良好的激光打孔质量
结语
打孔工序是LTCC工艺中的关键工序,打孔质量直接影响到LTCC组件的电气性能,而打孔效率又直接影响着LTCC组件的生产效率,在提升打孔质量的同时往往需要牺牲打孔效率,两者需要根据具体的应用场景和要求进行平衡。而如何通过工艺优化、设备升级和智能化控制,可以在保证质量的前提下提高效率,或在提高效率的同时确保可接受的质量水平,将是LTCC打孔工艺一直致力追寻的方向。
往期回顾
原文始发于微信公众号(矽瓷科技):低温共烧陶瓷工艺之打孔
长按识别二维码关注公众号,点击下方菜单栏左侧“微信群”,申请加入交流群。
