陶瓷基板在烧结成型之后,需对其表面实施金属化,然后通过影像转移的方法完成表面图形的制作,以实现陶瓷基板的电气连接性能。表面金属化对陶瓷基板的制作而言是至关重要的一环,这是因为金属在高温下对陶瓷表面的润湿能力决定了金属与陶瓷之间的结合力,良好的结合力是封装性能稳定性的重要保证。
目前,陶瓷表面常见的金属化方法大致可以分为共烧法(HTCC和LTCC)、厚膜法(TFC)、直接敷铜法(DBC)、直接敷铝法(DBA)及薄膜法(DPC)、活性金属焊接(AMB)等几种形式。艾邦建有陶瓷基板产业群,欢迎上下游企业加入微信群,长按识别二维码即可加入。
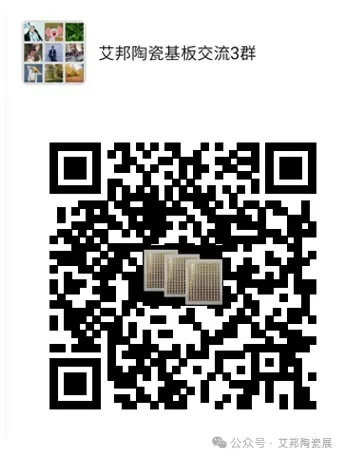
1.薄膜法( Direct plated copper,DPC)
薄膜法是主要采用物理气相沉积(真空蒸镀、磁控溅射等)等技术在陶瓷表面形成金属层,再采用掩膜、刻蚀等操作形成金属电路层的工艺过程。其中物理气相沉积是最常见的薄膜制造工艺。
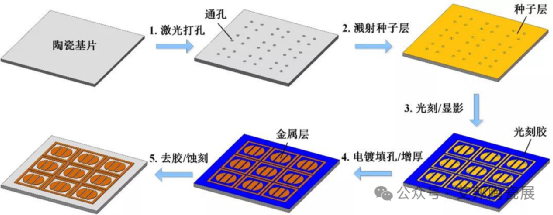
物理气相沉积是采用蒸镀或溅射等方法在陶瓷表面形成一层 3~5 μm 的金属薄膜作为陶瓷基板的导电层。因金属铜层与陶瓷层易发生热循环剥离失效,因此界面键合强度成为 DPC 基板的技术瓶颈。陶瓷与金属薄膜的结合力、金属薄膜与芯片的焊接性能以及金属薄膜自身的导电能力是衡量薄膜质量的三个重要指标。金属薄膜与氮化铝的结合力决定了薄膜工艺陶瓷基板的实用性与可靠性,而结合力则受到范德华力、化学键力、扩散附着、机械锁合、静电引力及薄膜自身内应力的综合影响,其中以扩散附着和化学键力为主要因素。因此需要选择 Al、Cr、Ti、Ni、Cu 等活性较高、扩散性能好的金属作为过渡层。导电层承担着电气连接及焊接的功能,因此需要选择 Au、Cu、Ag 等电阻率低、耐高温、化学性能稳定且扩散系数小的金属材料。
图 金属化陶瓷基板,来源:MARUWA
与其他陶瓷表面金属化方法相比,DPC 工艺操作温度低,一般在 300 ℃以下,降低了制造工艺成本,同时有效避免了高温对材料的不利影响。DPC 基板利用黄光微影技术制作图形电路,线宽可控制在 20~30μm,表面平整度可达 3μm 以下,图形精度误差可控制在 +1% 之内,非常适合对电路精度要求较高的电子器件封装。特别是在利用激光对 DPC 基板切孔与通孔填铜后,可实现陶瓷基板上下表面的互联,从而满足电子器件的三维封装要求。DPC 不仅降低了封装体积,还能有效提高封装集成度。DPC 陶瓷基板虽具有上述诸多优点,但是也存在着诸如电镀沉积铜层厚度有限,且电镀废液污染大、金属层与陶瓷间的结合强度较低,产品应用时可靠性较低等不足。
2.厚膜法( Thick film ceramic,TFC)
厚膜法是指采用丝网印刷的方式将导电浆料直接涂布在陶瓷基体上,然后经高温烧结使金属层牢固附着于陶瓷基体上的制作工艺。厚膜导体浆料的选择是决定厚膜工艺的关键因素,它由功能相(金属粉末)、粘结相(粘结剂)和有机载体所组成。常见的金属粉末有 Au、Pt、Au/Pt、Au/Pd、Ag、Ag/Pt、Ag/Pd、Cu、Ni、Al 及 W 等金属。粘结剂一般是玻璃料或金属氧化物或是二者的混合物,其作用是连结陶瓷与金属并决定着厚膜浆料对基体陶瓷的附着力,是厚膜浆料制作的关键。有机载体的作用主要是分散功能相和粘结相,同时使厚膜浆料保持一定的粘度,为后续的丝网印刷做准备,在烧结过程中会逐渐挥发。
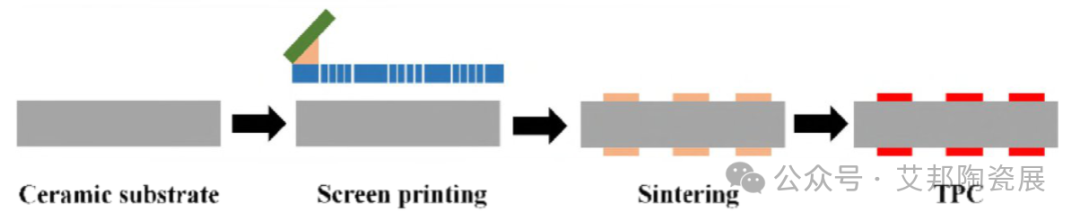
TFC 烧结后的金属层厚度一般为 10~20 μm,最小线宽为 0.1 mm。TFC 技术成熟,工艺简单,成本较低,但其存在图形精准度低(误差为+10%)、镀层稳定性易受浆料均匀性影响、线面平整度不佳( 3μm 以上)及附着力不易控制等缺点,使其应用范围受到了一定的限制。
3.共烧法( High/Low temperature co-fired ceramics,HTCC/LTCC)
共烧多层陶瓷基板利用厚膜技术将信号线、微细线等无源元件埋入基板中能够满足集成电路的诸多要求。共烧法有两种,一种是高温共烧(HTCC),另一种是低温共烧(LTCC),两者工艺流程基本相同,主要生产工艺流程均为:浆料配制、流延生带、干燥生坯、钻导通孔、网印填孔、网印线路、叠层烧结以及最后的切片等后处理过程。
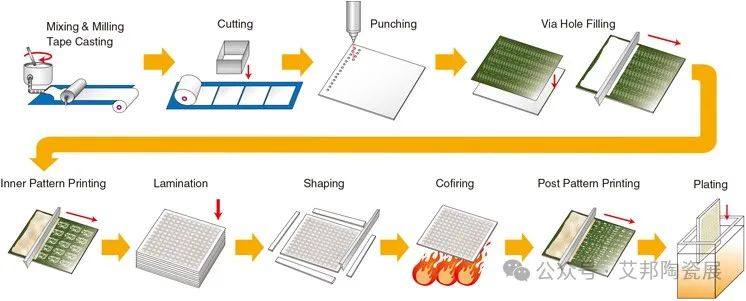
两种共烧法虽流程大致相同,所需设备也相差无几。但由于材料的差异较大,导致 LTCC 与 HTCC 在生产过程中的共烧温度区别较大,LTCC 烧结温度为 800~950℃,HTCC 烧结为 1650℃- 1850℃。
共烧陶瓷基板在增加组装密度、缩短互连长度、减少信号延迟、减小体积、提高可靠性等方面具有显著的优势。共烧基板更多的应用是将多种无源器件埋置于陶瓷基板中烧结制作成三维集成且互不干扰的高密度电路,在其表面贴装 IC 和有源器件,制作成功能集成模块,进一步减小电路结构,提高集成密度,特别适用于高频通讯用组件。然而,因 HTCC 与 LTCC 均是采用网版印刷完成图形制作,因此图形尺寸精度及表面粗糙度受印刷工艺的影响较大。同时,层压过程中也极易造成图形对位不精准而导致公差累积过大等问题。此外,生坯在烧结过程中容易出现收缩不一致的情况,这在很大程度上也限制了共烧工艺的应用。
目前可以通过将薄膜工艺与多层陶瓷共烧技术相结合,利用薄膜工艺分别对 HTCC 基板正背面进行精细线条制作,制造出高精度的薄厚膜电路。
4.直接敷铜法(Direct bonded copper,DBC)
DBC 是在陶瓷表面(主要是氧化铝和氮化铝)键合铜箔的一种金属化方法。其基本原理是在 Cu 与陶瓷之间引进氧元素,然后在 1065~1083℃ 时形成 Cu/O 共晶液相,进而与陶瓷基体及铜箔发生反应生成 CuAlO2 或 Cu(AlO2)2,并在中间相的作用下实现铜箔与基体的键合。因 AlN 属于非氧化物陶瓷,其表面敷铜的关键在于在其表面形成一层 Al2O3 过渡层,并在过渡层的作用下实现铜箔与基体陶瓷的有效键合。
氧的引入是 DBC 工艺中一个非常关键的步骤,氧化时间与氧化温度是该工艺中两个最重要的参数,对键合后陶瓷与铜箔之间的结合力有着非常重要的影响。当氧化时间和氧化温度固定时,没经预氧化处理的 Al2O3 基体在与铜箔敷接的过程中,因氧难以渗入铜箔与陶瓷基板的界面,Cu/O 液相对基板的润湿性较差,最后会在界面上残留大量的空洞和缺陷。而基体经预氧化处理后,可在敷接的同时给予充足的供氧,则 Cu/O 液相对陶瓷基体和铜箔润湿性良好,界面空洞及缺陷明显减少,铜箔与基体的结合力也较为牢固。
而 AlN 是强共价键化合物,Cu/O 液相对其润湿性较差,在其表面利用 DBC 方式敷铜时则必须通过表面改性的方式来增强 Cu/O 液相对陶瓷基体的润湿性以确保铜箔与基体的结合力。目前一般的做法是利用预氧化的方式在 AlN 表面形成一定厚度、分散均匀且结构致密的 Al2O3 薄膜。因氧化铝薄膜与氮化铝基体的热膨胀系数不匹配,室温条件下两相界面可能会因内应力的存在而导致结合力变差,所以膜的质量是后续敷接成败的关键。一般而言,欲实现二者的有效结合,必须在保证氧化膜致密的前提下,尽可能减小膜的厚度来降低 AlN 与 Al2O3 两相之间的内应力。
DBC 陶瓷基板具有高热导率、高绝缘性能和高可靠性被广泛应用于 IGBT、LD 和 CPV 等的封装散热管理中。但 DBC 也存在如下不足:
(1) DBC 工艺需要在高温条件下引入氧元素使 Cu 与 Al2O3 发生共晶反应,对设备和工艺控制要求较高,基板制作成本较高;
(2) Al2O3 与 Cu 层之间容易产生微气孔,基板抗热冲击性能会受影响;
(3) DBC 表面键合铜箔厚度一般在 100 μm 以上,表面图形最小线宽一般大于 100μm,不适合精细线路的制作。
5.活性金属焊接陶瓷基板(Active Metal Brazing,AMB)
AMB陶瓷基板利用含少量活性元素的活性金属焊料实现铜箔与陶瓷基片间的焊接,其工艺流程如下图所示。活性焊料通过在普通金属焊料中添加Ti、Zr、Hf、V、Nb或Ta等稀土元素制备,由于稀土元素具有高活性,可提高焊料熔化后对陶瓷的润湿性,使陶瓷表面无需金属化就可与金属实现焊接。AMB基板具有优异的力学性能及耐高低温冲击可靠性,成为功率模块的封装材料。
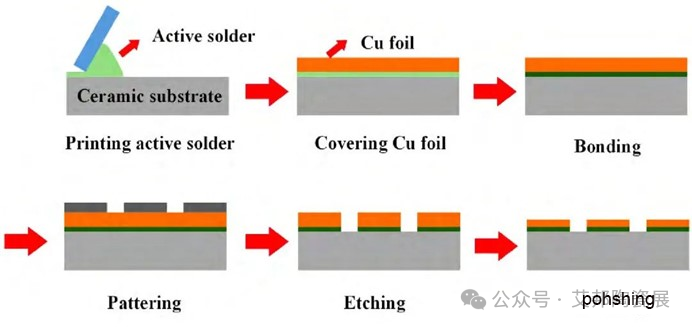
AMB基板制备技术是DBC基板工艺的改进(DBC基板制备中铜箔与陶瓷在高温下直接键合,而AMB基板采用活性焊料实现铜箔与陶瓷基片间键合),通过选用活性焊料可降低键合温度(低于800°C),进而降低陶瓷基板内部热应力。AMB基板依靠活性焊料与陶瓷发生化学反应实现键合,因此结合强度高,可靠性好。
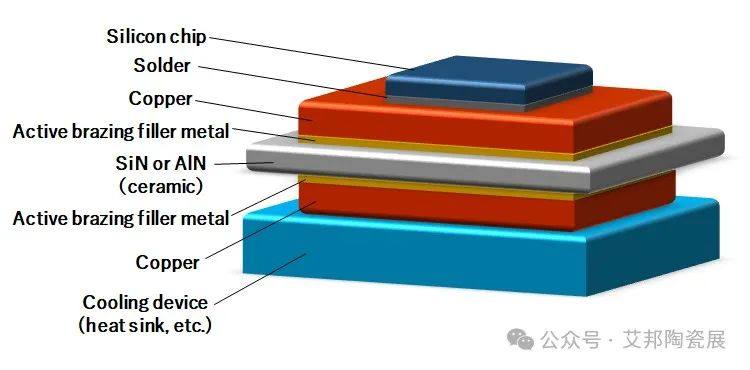
AMB陶瓷覆铜板的核心是活性金属钎焊浆料及其互联工艺,对可靠性影响较大,很大程度取决于活性钎焊浆料的成分、钎焊工艺、钎焊层组织结构、反应层厚度等诸多关键因素。AMB基板的成本较高限制了其推广应用。
6.直接敷铝法( Direct Bonded Aluminum,DBA)
直接敷铝法是利用铝在液态下对陶瓷有着较好的润湿性以实现二者的敷接。当温度升至 660℃ 以上时,固态铝发生液化,当液态铝润湿陶瓷表面后,随着温度的降低,铝直接在陶瓷表面提供的晶核结晶生长,冷却到室温实现两者的结合。由于铝较为活泼,在高温条件下容易氧化生成 Al2O3 薄膜而存在于铝液表面,大大降低铝液对陶瓷表面的润湿性使敷接难以实现, 因此在敷接前必须将其去除或是在无氧条件下进行敷接。
在敷接铝之前,对陶瓷进行表面处理以增大敷接强度是非常关键的工艺环节。陶瓷基板表面粗糙度在很大程度上影响敷接性能,保持一定的粗糙度是提高敷接强度的必要条件。因此如何处理陶瓷基板以改变其粗糙度是提高铝/陶瓷之间结合强度的关键。
DBA陶瓷基板热稳定性良好,与同结构的 DBC 相比质量可减轻 44%,铝线键合能力佳,铝/陶瓷之间的热应力也相对较小,近年来发展迅速。Al2O3-DBA 基板及 AlN-DBA 基板具有优异的导热特性、良好的抗热震疲劳性能、出色的热稳定性及结构质量轻和良好的铝线键合能力,基于 DBA 基板的电力器件模块已成功在日本汽车工业中得到应用。因对氧含量有严格的限制,DBA 对设备和工艺控制要求较高,基板制作成本较高。且表面键合铝厚度一般在 100 μm 以上,不适合精细线路的制作。
资料来源:
1.《陶瓷基板表面金属化研究现状与发展趋势》,秦典成,等.
2.《电子封装陶瓷基板》,程浩,等.
艾邦建有陶瓷基板产业群,欢迎上下游企业加入微信群,长按识别二维码即可加入。
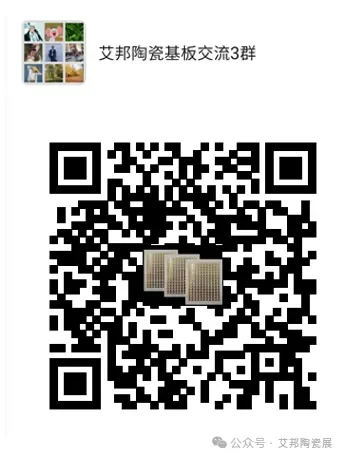
The 2nd Ceramic Packages Industry Forum
河北·石家庄
一、会议议题
序号
|
暂定议题
|
演讲单位
|
1
|
薄膜技术在封装中的应用
|
中电科四十三所 车江波 高级工程师
|
2
|
陶瓷封装技术在半导体器件领域的应用
|
北京大学东莞研究院 郑小平 研究员/项目总监
|
3
|
传感器技术的发展及陶瓷封装的应用趋势
|
郑州中科集成电路与系统应用研究院 先进封测中心主管 周继瑞
|
4
|
集成电路高可靠陶瓷封装的发展概况
|
睿芯峰
|
5
|
微电子封装用封接玻璃的开发
|
天力创
|
6
|
高品质氮化硅粉体规模化制备关键技术新进展
|
中国科学院理化技术研究所/中科新瓷(重庆)科技有限公司 高级工程师/总经理 杨增朝
|
7
|
功率模块封装用高强度高热导率Si3N4陶瓷的研究进展
|
中材高新氮化物陶瓷有限公司 高级专家 张伟儒
|
8
|
电子封装陶瓷基板关键的制备技术
|
河北东方泰阳
|
9
|
钙钛矿型铁电介质陶瓷开发及应用
|
电子科技大学 唐斌 教授
|
10
|
低温共烧陶瓷基板及其封装应用
|
中电科43所 董兆文 研究员
|
11
|
集成电路陶瓷封装外壳仿真设计
|
拟邀请陶瓷封装厂商/高校研究所
|
12
|
系统级封装用陶瓷材料研究进展和发展趋势
|
拟邀请陶瓷封装厂商/高校研究所
|
13
|
陶瓷封装结构优化及可靠性分析
|
拟邀请陶瓷封装厂商/高校研究所
|
14
|
陶瓷薄膜金属化工艺技术
|
拟邀请金属化设备企业
|
以最终议题为准。更多议题征集中,欢迎自拟或者推荐议题。演讲&赞助&会议报名请联系李小姐:18124643204(同微信)
方式一:加微信
李小姐:18124643204(同微信)
邮箱:lirongrong@aibang.com
扫码添加微信,咨询展会详情
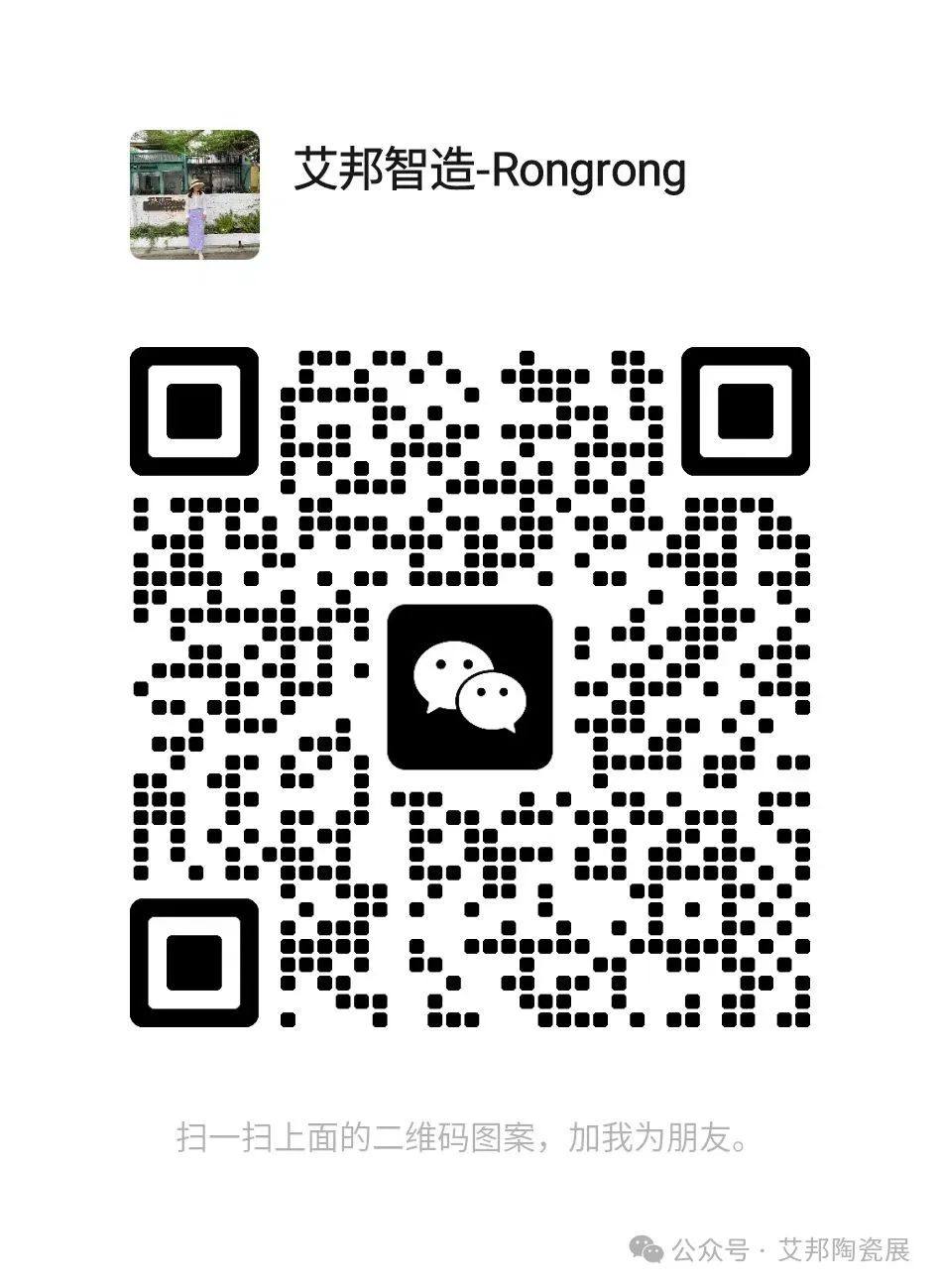
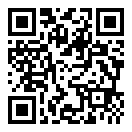
https://www.aibang360.com/m/100216?ref=196271
点击阅读原文,即可在线报名!
原文始发于微信公众号(艾邦陶瓷展):电子封装陶瓷基板表面金属化技术介绍