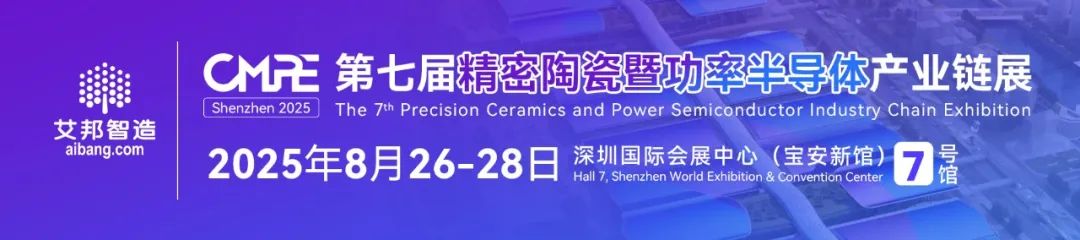
氮化铝(AIN)陶瓷由于高热导(理论可达320 W·m−1·K−1)、低的介电常数(在1 MHz测试条件下为8.0)和介电损耗(介电损耗角为tanδ=10−4)、低热膨胀系数以及高强度、高耐蚀性、良好的绝缘性(>1014 Ω·cm)等优良的综合性能,不仅是功率器件理想的封装和基板材料,也被应用于半导体制程装备用静电卡盘、氮化铝加热器、陶瓷喷嘴等关键零部件。氮化铝陶瓷由氮化铝粉末烧结而成,高质量粉末原料是获得高性能氮化铝陶瓷的先决条件,氮化铝粉末的制备对最终氮化陶瓷的烧结、成型以及导热效率等性能有重要影响。工业上制备氮化铝粉末的方法有三种,分别是直接氮化法、自蔓延高温合成法与碳热还原法。1.碳热还原法的原理
碳热还原法通常以铝的化合物为原料(如氧化铝、氢氧化铝等),与过量的单质碳或有机碳为原料在氮气(N2)/氨气(NH3)气氛中高温下合成氮化铝,产物经 500~700℃温度氧化气氛下除碳获得氮化铝粉体,具有氧含量低、纯度高、粒度分布窄、颗粒形貌规则等优点。其反应原理如式所示。一般认为此反应分两步进行:①氧化铝的还原:由碳还原生成中间产物Al(g)和Al2O3(g);②氮化:Al与 N2发生反应制得 AIN。碳热还原法制备 AlN 的反应机理可分为气一固反应、固一固反应2大类。经实验观察到的铝蒸汽发射峰佐证了特定条件下的含铝气相的产生,同时气–固反应也解释了反应过程的质量损失和晶须生长的传质过程;而固–固反应控制机理则解释了合成产物与前驱物形貌延续的现象以及多项研究中Al—O—C 与 Al—C—N 等 Al2O3的转化中间态化合物的形成机制,该机理也得到更广泛的认可。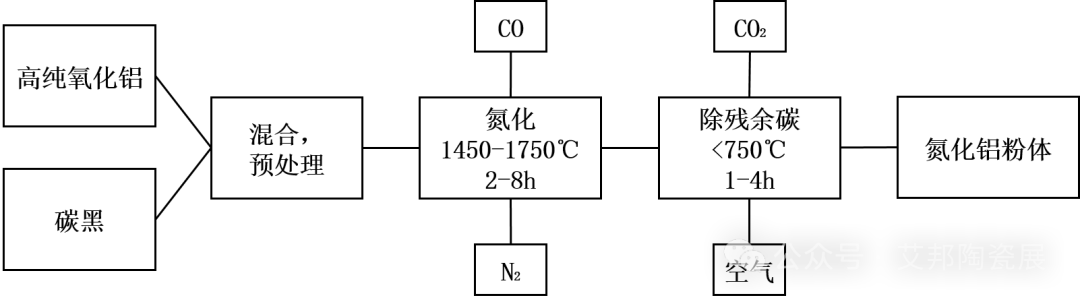
AIN粉末制造工艺流程主要包括球磨混料、氮化合成、低温除炭、氮化铝粉碎回收等。2.碳热还原法工艺特点
碳热还原法具有原料丰富、工艺简单、适合大规模生产的特点,且合成粉体球形度高、纯度高、粒径小、粒度分布窄、分散性好等特点,是目前工业化生产氮化铝粉体的主要方法。较直接氮化法与自蔓延高温合成法而言,碳热还原法制得的粉末具有更高的纯度和较好的球形度。但是碳热还原法存在对原料的性能要求高,合成温度高且效率低、生产周期长,而且后期还需二次除碳,工艺繁琐,成本高等问题。通常采用以下方法改善工艺:许多研究表明,碳热还原法合成氮化铝粉末的质量和氮化温度与原料的种类和性能密切相关,采用不同种类的原料,氮化温度相差可达200℃。使用键能更低的铝源和碳源为原料, 有助于在低温短时内获得高质量的氮化铝粉体。Al2O3原料的粉体粒径越小,表面积越大、表面自由能越高,与C粉接触的面积越大,能有效促进碳热还原反应的进程。减小原料的粒度和增加原料的混合均匀程度可降低碳热还原法制备氮化铝粉末的反应温度,提高反应速率。Al2O3粉体与C粉的混合越均匀,越利于碳热还原反应的进行。传统获得混合均匀且粒径细小的Al2O3与C粉的方法是通过球磨共混的方式实现。经高能球磨细化后的Al2O3,相对于原始粉末,反应生成的AIN量有较大提高。相较于通过机械球磨混和分散超细氧化铝粉体,使用铝化合物(即,铝盐或铝醇盐)与有机配体在沸腾溶液中反应制成前驱体,在碳热还原反应发生前,通过热解可获得成分更加均匀且结合紧密的Al2O3+C混合物。2)改变制粉过程条件,通过引入微波、高活性气氛与烧结助剂的方式降低反应温度。艾邦建有半导体陶瓷产业交流群,欢迎产业链上下游的企业扫码下方二维码进入:第七届精密陶瓷暨功率半导体产业链展览会
2025年8月26日-28日
展出2万平米、1,000个摊位、500多家展商、50,000名专业观众;汇聚IGBT/SiC功率半导体产业链;热管理材料产业链,精密陶瓷、电子陶瓷、陶瓷基板、薄膜/厚膜陶瓷电路板、陶瓷封装管壳、LTCC/HTCC/MLCC加工产业链、SOFC/SOEC隔膜等产业链上下游企业!
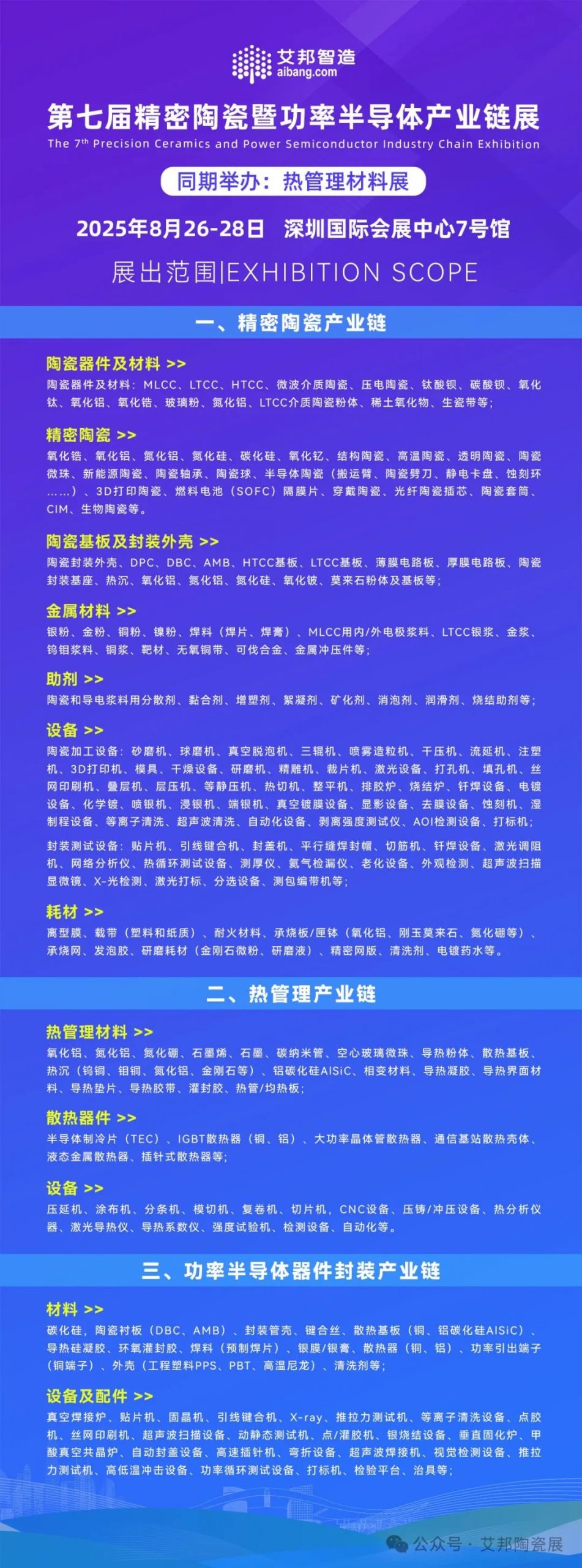
展会预定:
扫码添加微信,咨询展会详情
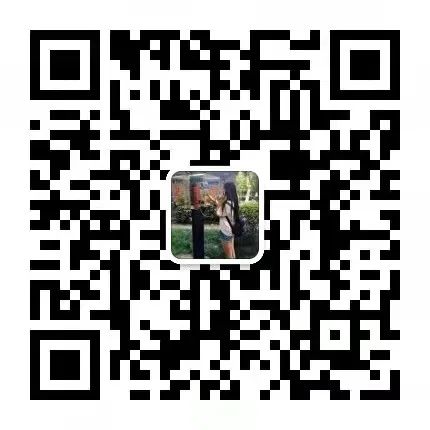
扫码添加微信,咨询展会详情
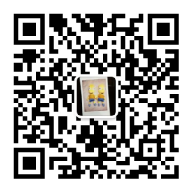
长按识别二维码关注公众号,点击下方菜单栏左侧“微信群”,申请加入交流群。
