随着LED技术的快速发展,功率型LED在照明、显示、汽车电子等领域的应用日益广泛。然而,功率型LED在工作时会产生大量热量,若散热问题得不到有效解决,将直接影响其光效、寿命和可靠性。在LED散热通道中,封装基板是连接内外散热通路的关键环节,需兼有散热通道、电路连接和对芯片进行物理支撑的功能。而DPC基板(直接镀铜陶瓷基板)凭借高导热、高精度线路和优异平整度,完美适配功率型LED封装需求。
一、DPC工艺流程
DPC 陶瓷基板制备工艺:首先利用激光在陶瓷基片上制备通孔 (孔径一般为 60 μm ~ 120 μm),随后利用超声波清洗陶瓷基片;采用磁控溅射技术在陶瓷基片表面 沉积金属种子层 (Ti/Cu),接着通过光刻、显影完成线路层制作;采用电镀填孔和增 厚金属线路层,并通过表面处理提高基板可焊性与抗氧化性,最后去干膜、刻蚀种子 层完成基板制备。
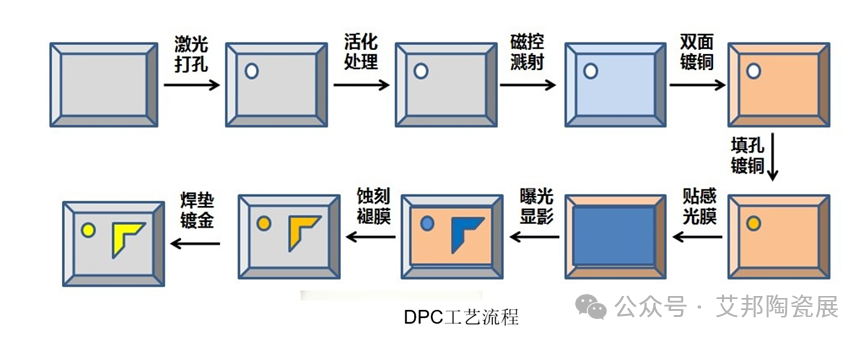
DPC工艺流程图
二、DPC工艺与功率型LED适配点
DPC基板具备线路精准度高、表面平整度高等特性以及与LED芯片材料相匹配的热膨胀系数,因此成为功率型LED封装的理想选择。不仅能够满足小尺寸、高密度封装的设计需求,还能在高功率、高温环境下保持稳定性能,为功率型LED的高效散热和长期可靠性提供了强有力的支持。因此,DPC适用于功率型LED覆晶/共晶工艺,以下是DPC工艺与功率LED的适配点:
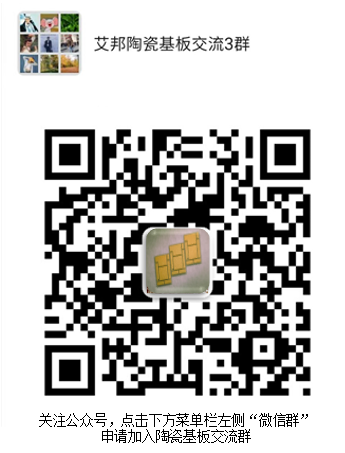
图 DPC基板用于LED封装
1、线路精度高:
DPC陶瓷基板采用半导体微加工技术,陶瓷基板上金属线路更加精细(线宽/线距低至30μm~50μm,与线路层厚度相关),因此DPC陶瓷基板非常适合功率型LED的应用需求 。
2、表面平整度高:
采用电镀生长控制线路层厚度(一般为10μm~100μm),并通过研磨降低线路层表面粗糙度,满足高温、大电流器件封装需求;
3、成本低:
低温制备工艺(300℃以下)避免了高温对基片材料和金属线路层的不利影响,同时也降低了生产成本。
4、便于封装:
采用激光打孔和电镀填孔技术,实现了陶瓷基板上下表面垂直互连,可实现电子器件三维封装与集成,降低器件体积;可有效满足倒装共晶、 COB (板上芯片封装)、CSP (芯片尺寸封装) 等技术白光 LED 封装需求。
5、高导热性
功率型LED在工作时会产生大量热量,若散热不良会导致光效下降、寿命缩短。DPC基板采用高导热陶瓷材料(如Al₂O₃或AlN),导热性能优异,能快速将热量从LED芯片传导至外部,确保LED稳定工作。
6、绝缘性好:
功率型LED工作电压较高,要求基板具有良好的电气绝缘性。DPC基板的陶瓷层绝缘性能优异,能够有效防止漏电和短路。
7、热膨胀系数小:
功率型LED在工作时会产生热胀冷缩,若基板与芯片材料的热膨胀系数不匹配,会导致热应力问题。DPC基板的热膨胀系数与LED芯片材料(如GaN、Si)接近,能够减少热应力,提高可靠性。
文章整理于网络
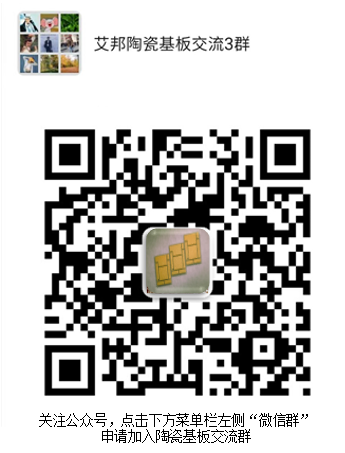
长按识别二维码关注公众号,点击下方菜单栏右侧“微信群”,申请加入陶瓷基板交流群
2025年8月26日-28日
展出2万平米、1,000个摊位、500多家展商、50,000名专业观众;汇聚IGBT/SiC功率半导体产业链;热管理材料产业链,精密陶瓷、电子陶瓷、陶瓷基板、薄膜/厚膜陶瓷电路板、陶瓷封装管壳、LTCC/HTCC/MLCC加工产业链、SOFC/SOEC隔膜等产业链上下游企业!
展会预定:
扫码添加微信,咨询展会详情
扫码添加微信,咨询展会详情
长按识别二维码关注公众号,点击下方菜单栏左侧“微信群”,申请加入交流群。
